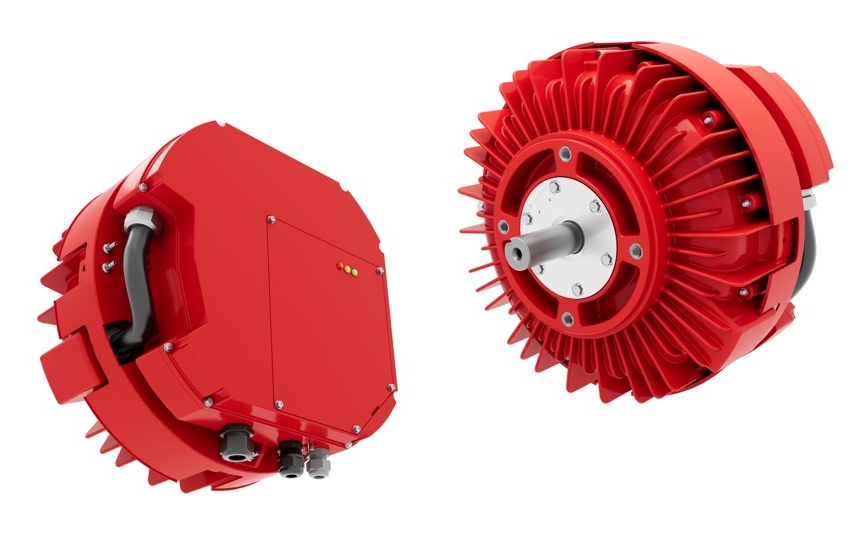
Front and back views of the Infinitum Aircore Heavy Duty motor system. (Photos: Business Wire)
Infinitum’s high-efficiency system has a form factor that is reportedly 50 percent lighter and 60 percent shorter in length than conventional motor and drive systems.
ORLANDO, Fla.—Infinitum, the creator of an energy-saving air-core motor, introduced its Aircore Heavy Duty at the AHR Expo in February. The high-efficiency motor system is designed to power the world’s most demanding, mission-critical HVAC fan and pump applications with reduced energy consumption, emissions, noise, and waste, the company said in a release.
The Aircore Heavy Duty features an integrated variable frequency drive. It is reported to power heavy loads sustainably, with up to 25 percent more efficiency, maximum power density, and high reliability. The motor system has a compact form factor that is 50 percent lighter and 60 percent shorter in length than conventional motor and drive systems, according to Infinitum.
“Our new Aircore Heavy Duty brings our award-winning motor system design to the world’s highest-emitting HVAC fan and pump applications, including those that are increasingly used to cool data centers handling AI workloads,” said Ben Schuler, founder and CEO of Infinitum, in the release. “Our talented team has once again raised the bar for efficiency, serviceability, and reliability to power the world with less energy, material, and waste.”
Built with a rugged exterior for protection against dust, dirt and water, the Aircore Heavy Duty is said to operate reliably in harsh outdoor or wet environments, maintaining high efficiency over a wide range of operating points. It is available in a range of power, bearing, and NEMA MG1 shaft and frame sizes suitable for demanding, heavy duty applications. Such applications include HVAC equipment, vertical-inline pumps, and coolant distribution Units (CDUs) used in data centers handling AI workloads, and in other mission critical facilities, the company said in the release.
The Aircore Heavy Duty includes features designed to support “rightsizing,” as well as improved communication, controls, serviceability, and flexible mounting.
Customers can specify a motor with the application’s exact HP/RPM requirement, thereby reducing the power budget per motor and freeing up electrical infrastructure for other critical needs in the facility. The system supports a wide variety of communication protocols, including Modbus RTU, BACnet MSTP, and analog. It enables users to configure and fine-tune operational parameters, while monitoring motor performance, carbon emissions, energy consumption, heat, and vibration.
For improved serviceability, the Aircore Heavy duty has a modular design that is said to make repairs fast and simple. It also offers flexible mounting with a compact form factor that optimizes space, reduces wiring needs, and facilitates direct mounting to pump applications, increasing efficiency by 10-15 percent, the company said.
Like other Infinitum motors, the Aircore Heavy Duty motor replaces the copper wound iron stator found in traditional motors with a lightweight, printed circuit board (PCB) stator that is reportedly 10 times more reliable. The motor uses 66 percent less copper and no iron in the stator, and produces significantly less noise. Infinitum motors are manufactured in a sustainable facility from components that can be remanufactured and reused so that they stay in service and out of landfills, the release stated.
“With its newest Aircore Heavy Duty model, Infinitum is continuing to serve the larger sustainability picture,” said Blake Griffin, of Interact Analysis, in the release. “The motor appears well suited to improve overall system efficiency while addressing broader electrical infrastructure concerns. In my opinion, this motor is poised to help customers improve on sustainability, usability, and the bottom line.”