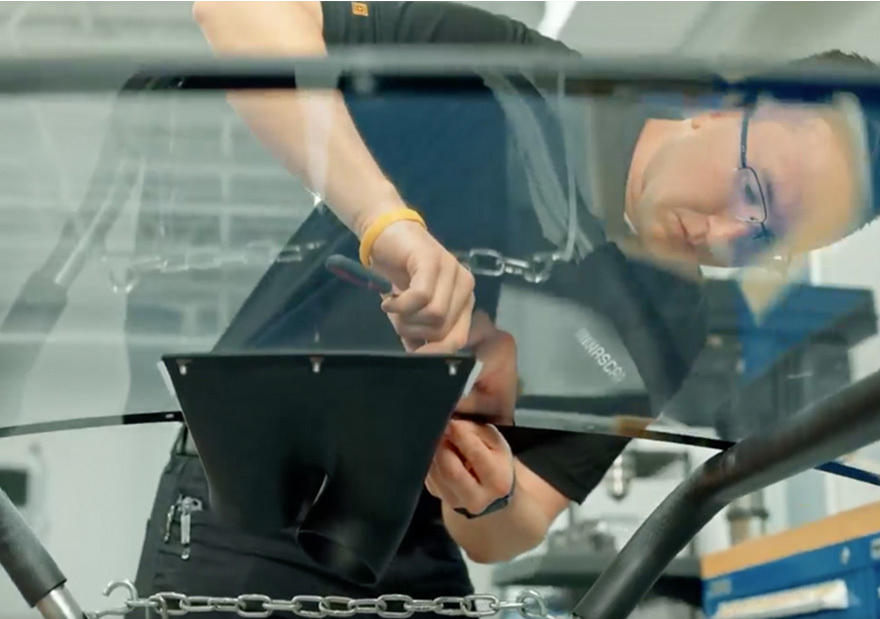
Stratasys has become the official and exclusive 3D printing partner for NASCAR. Here, an engineer attaches a 3D printed duct used to keep drivers cool during races. (Photo: Business Wire)
Under a multi-year agreement, NASCAR will use Stratasys 3D printing technology exclusively for accelerated design and production of parts and tools across NASCAR.
EDEN PRAIRIE, Minn. & REHOVOT, Israel, and DAYTONA BEACH, Fla.—Stratasys recently announced an expanded long-term technical partnership with the National Association for Stock Car Auto Racing (NASCAR), making Stratasys the official 3D printing partner of NASCAR and cementing its role as a critical technology provider, according to a release from Stratasys.
Under the multi-year agreement, NASCAR will exclusively use Stratasys 3D printing technology for the design and production of parts and tools across NASCAR, replacing previous technologies used alongside Stratasys technology. The motorsports innovator is printing the parts and tools in a new state-of-the-art 3D printing lab at the NASCAR Research and Development Center in Concord, North Carolina.
The R&D center features multiple Stratasys technologies, including F370, 450mc, and F900 FDM printers and an NEO800 SL printer to support research and development, parts production, and tooling for NASCAR’s three national series.
According to Stratasys, NASCAR engineers will benefit from the agility of 3D printing, which allows for faster design cycles and on-demand production of custom components, keeping them at the cutting edge of performance and safety.
“Partnering with Stratasys allows NASCAR to push the boundaries of performance and accuracy like never before,” said John Probst, executive vice president and chief racing development officer at NASCAR, in the release. “Their 3D printing technology empowers us to quickly iterate and optimize components, ensuring that our staff have the best possible machines to stay ahead in this high-stakes environment. Stratasys has proven to be a valuable partner, and this agreement represents our commitment to staying at the forefront of motorsports innovation.”
As part of the expanded partnership, Stratasys will increase the existing FDM® (Fused Deposition Modeling) capabilities within the NASCAR R&D center, allowing for larger-scale parts production. In addition to FDM technology, NASCAR will integrate Stratasys NEO® stereolithography (SL). These technologies will support a variety of applications, from aerodynamic testing to prototyping and production parts with high-precision tooling, and are expected to further enhance the design and manufacturing flexibility that 3D printing brings to the sport, the release said.
Engineers at NASCAR worked with Stratasys on parts for NASCAR Cup Series cars. Now, every vehicle on the track is reportedly using 3D printed parts.
For example, NASCAR worked with Stratasys Direct Manufacturing for on-demand production parts using the H350 SAF printer, with plant-based Nylon11 material, to produce a cold air inlet vent at the top center of a windshield. The vent forces air into the car to cool the driver.
NASCAR also leveraged FDM printers in the NASCAR R&D Center to produce a NACA duct with ULTEM® 9085 black material. The duct, located on the car’s lower engine panel, is used to vent hot air out from the engine bay.
“Our partnership with NASCAR allows Stratasys to showcase the unique advantages of 3D printing in motorsports,” said Rich Garrity, chief business unit officer at Stratasys, in the release. “From on-demand manufacturing of custom components to speeding up the design cycle, we’re helping NASCAR with faster production times and enhanced part performance. Furthermore, our work in high-performance environments like NASCAR spurs innovation in the production of commercial vehicles, demonstrating the broader impact of additive manufacturing across the automotive industry.”