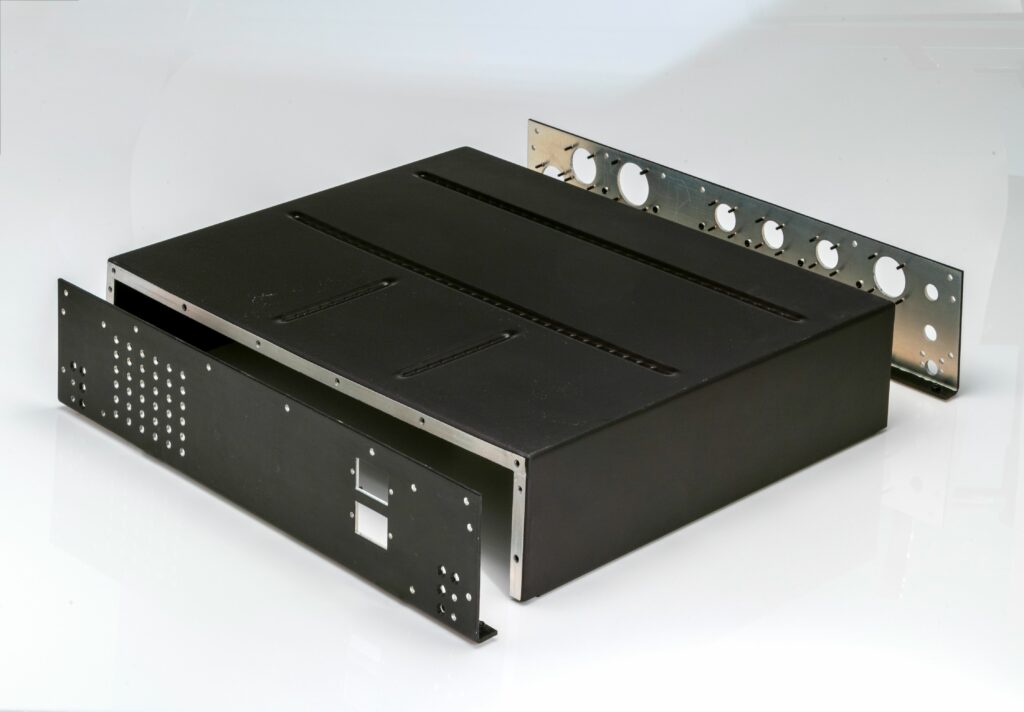
An electronics enclosure produced by Mika Metal Fabricating. (Photo courtesy Mika Metal Fabricating)
Mika Metal Fabricating’s core competencies include the manufacturing of complex enclosures and boxes.
WILLOUGHBY, Ohio—Mika Metal Fabricating is a custom sheet metal fabricator that combines manufacturing excellence with a strong set of core values.
Under the leadership of its chairman, Scott Shelfer, and president, Ryan Thomas, Mika Metal Fabricating is dedicated to improving “efficiencies that will drive down costs and reduce turnaround times and build a culture that puts Fans (customers) First, supports Team Always, and serves the Greater Good while ensuring long-term Sustainable Success for the organization,” the company’s website stated.
Mika Metal Fabricating has a long history of quality craftsmanship that dates back to 1939, when it began operating as B&F Metal Fabricating in South Euclid, Ohio, under the direction of Fred J. Mika. The company became a custom sheet metal fabrication shop in 1941, going on to produce metal ammunition boxes for Cleveland Tank Company during World War II, according to Mika’s website.
Today, the company provides custom sheet metal fabrication and design services to numerous high-end industries, including medical and surgical; electronics; electrical and power distribution; utilities and telecommunication; and vending machines and self-service kiosks.
In addition to partnering with customers on product development and assisting with design for manufacturing (DFM), Mika Metal Fabricating provides a full complement of fabrication services, including laser cutting and etching; CNC punching; press brake forming; drilling, tapping, and counter sinking; spot welding; MIG and TIG welding; and hardware insertion. The company also performs assembly, powder coating, screen printing, hand stamping, kitting, and fulfillment services.
“Mika’s capabilities provide tight tolerances for simple parts and components up to complex, turnkey assemblies,” said Rebecca Cole, the company’s director of sales and marketing, in an emailed response.
Mika Metal Fabricating employs approximately 27 full-time team members, bringing in temporary workers to scale up when needed. “By teaming tenured industry veterans with future sheet metal professionals, we combine tribal knowledge with energy and exuberance for the benefit of all to learn and continue growing, no matter where they are in their professional journey,” the company’s website stated.
One of Mika Metal Fabricating’s core competencies is its manufacturing of complex enclosures and boxes, according to Cole.
For the electronics industry, the company makes PCB box assemblies, enclosures, and related components. For the electrical and power distribution markets, Mika fabricates stationary and portable power storage and distribution cabinets, as well as inverter and enclosures.
The company supports the utilities and telecommunications industry with fabricated fiber optic hub enclosures, metering pole boxes, mounts, and related components. It also supplies the medical and surgical markets with medical gas zone valve enclosures; medical gas control panels and conversion kits; and reflective panels, plates, brackets, and housings for phototherapy devices.
One of the ways Mika helps customers reduce costs is through its expertise in design for manufacturing (DFM), particularly in the early phases of new product development, Cole said.
“Advanced expertise in design for manufacturing (DFM), held by senior members of the engineering team, is combined with the knowledge of junior engineers implementing and using software such as SolidWorks—all of which benefits customers by driving out costs and improving final outcomes,” she explained.
Mika Metal Fabricating’s 80,000-square-foot facility includes 60,000 square feet of shop floor space. The company’s 19-member shop floor staff has an average tenure of 20 years, Cole said, and it represents diverse skills contributed by workers with various levels of experience.
“This much production experience, combined with the extensive knowledge held by our estimating and manufacturing engineering personnel, complemented recent high school and college interns who worked across departments to offer fresh insights into the latest manufacturing tools and resources while gaining valuable tribal knowledge,” Cole said. “Some processes, such as silk-screening, differentiate our offering because we have mid-career, highly skilled operators who have learned this nearly lost art in the industry.”
Mika recently enhanced its manufacturing capabilities by bringing in-house an Amada Ventis 4kW Fiber Optic laser cutter (2023) and two Amada HRB 1003 Hydraulic Press Brakes, one with an auto-crowning feature. Other recent additions are a Lissmac Steelmaster Wet Metal Finishing and Deburring Machine, and a Teena Spot Welder.
Cole noted that in addition to the new equipment, Mika Metal Fabricating has undergone extensive updates and renovations since coming under new ownership in 2020. Office and conference room areas were updated with fresh paint, as well as new ceiling tiles and lighting. The production area was significantly reorganized to provide more efficiency and better throughput of parts and materials.
“Wi-Fi installation on the shop floor allowed for the implementation of web-based job tracking technology utilizing bar code scanners,” she said. “Outdated incandescent lighting was replaced with LED bulbs, cushioned mats were placed at every workstation, and fire extinguishers and eye wash stations were installed throughout the shop floor, leading to increased employee satisfaction and improved safety conditions.”
Mika also collaborated with start-up app developer Reimagine Training (reimagine.training) in 2023 to create, beta test, and launch a mobile employee onboarding and training platform specifically geared towards manufacturers, fabricators, and machine shops, Cole said.
One customer in the micro-market industry approached Mika for help in solving challenges that arose, in part, from the outdated design of its self-service kiosk offerings. Cole explained that the application was a self-service, point-of-sale kiosk for use at on-site mini markets often found in hotels or corporate break areas.
The oversized, angular shape of the customer’s product line contrasted unfavorably with its competitors, who were introducing sleeker, smaller-footprint and more aesthetically pleasing models, Cole said. As a result, the customer’s market share was eroding and revenue was declining. Its goal was to unveil two completely redesigned units at an upcoming industry expo, scheduled to take place in four months.
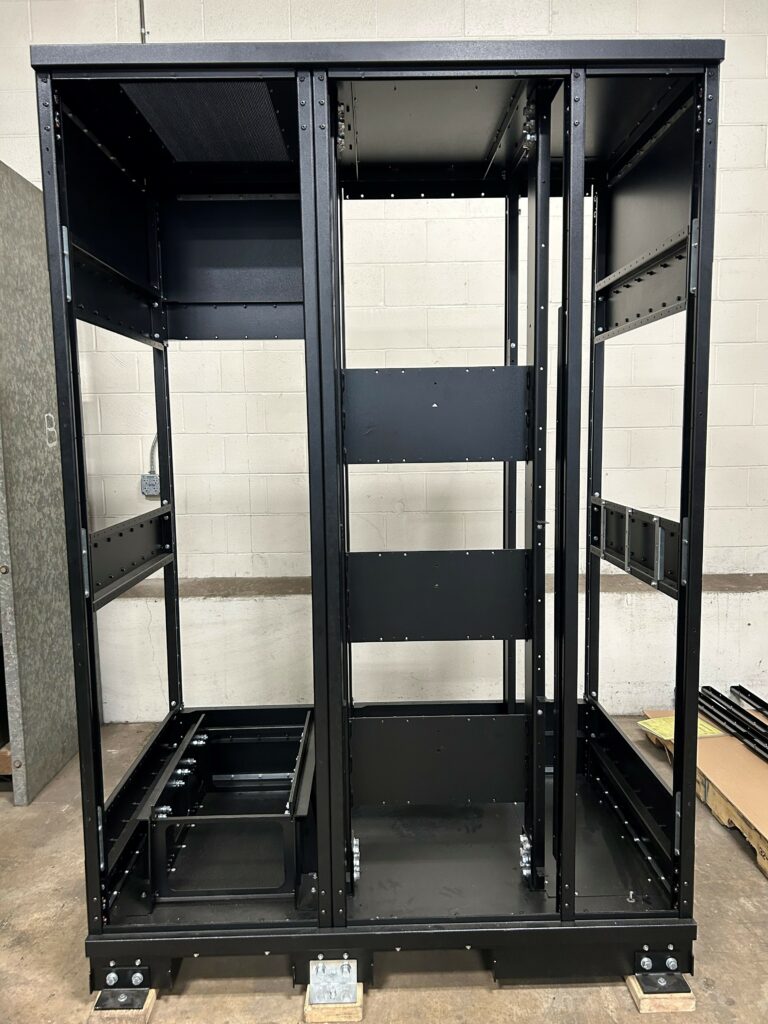
A large, stationary power distribution unit manufactured by Mika Metal Fabricating. (Photos courtesy Mika Metal Fabricating)
A major engineering challenge was to develop a smaller, lighter, and aesthetically pleasing unit that featured rounded design elements while offering tamper resistance. It needed to remain easy for repair and for other users to access internal components. The finished product also needed to accommodate a standard LED screen, theft-deterring camera, ethernet port, credit card reader, and optional bill validator.
An aggressive delivery target meant that time was of the essence. The customer’s engineering team reached out to Mika’s team with concept renderings, asking them to provide initial Design for Manufacturing recommendations for minimizing features that could increase costs.
By applying Mika’s DFM recommendations, the customer was able to present a print package, followed by several more rounds of design iterations.
“We made prototypes and continued to refine the design until they landed on a version that accommodated all the necessary features,” Cole said. “The project was finished in time for their show and received very positive feedback from their customers.”.
Mika reached deep into its manufacturing toolbox to fulfill the project’s requirements, leveraging processes such as laser cutting, CNC punching, bending, and welding. The company also performed grinding, hardware insertion, masking, and powder coating.
Ultimately, Mika helped its customer reduce the size of the unit from 27 ⅞ inches by 17 ⅝ inches x 13 ¾ feet, with a weight of 62 pounds, to 32.28 inches by 14.38 inches by 9 ⅞ feet, with a weight of 44 pounds.
“The final product was much lighter, with a less boxy profile that accommodated all necessary features, providing better competitive advantages for their offering,” Cole said.