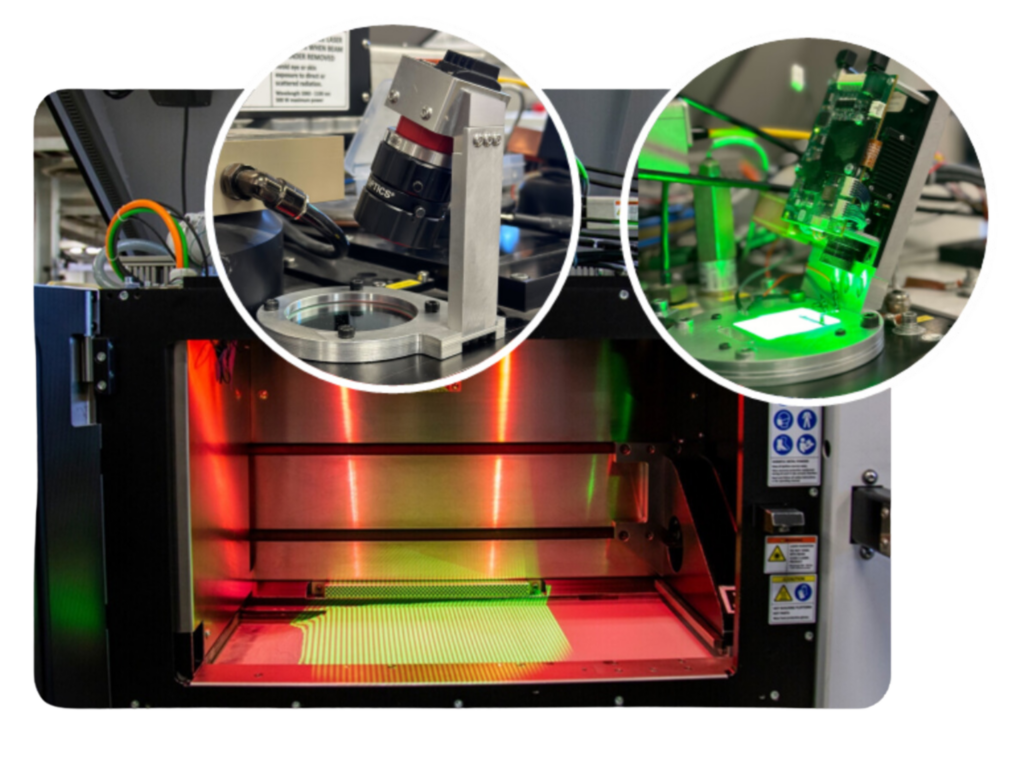
Fringe Inspection is an in-situ inspection technology which uses a camera and projector, mounted outside of the build chamber, to quantify what is happening in every layer of the build process. Fringe Inspection uses a well-known technology called fringe projection to create a unit-based heightmap of the layer to identify build anomalies to perform root-cause analysis and improve and/or control the process.
Phase3D’s technology is said to save time and costs by detecting anomalies in real-time, reducing lead times and scrap.
YOUNGSTOWN, Ohio—Noah Mostow, Business Development Manager at Chicago-based Phase3D, is determined to revolutionize in-situ monitoring (ISM) for additive manufacturing (AM). According to a release from America Makes, his vision is to make AM inspection technology so intuitive that even recent high school graduates could operate AM machines—no Ph.D. or decades of experience required.
Central to this plan is the company’s Fringe ISM technology, which measures and quantifies each build layer in real-time for powder-based AM processes. Mostow is confident that this innovative technology has the potential to transform operations in manufacturing facilities.
Solving challenges in AM monitoring
Real-time anomaly detection in ISM has proven invaluable for powder-based AM processes. However, existing ISM technologies often struggle to keep up with the rapidly evolving AM landscape. Conventional methods, such as CT scans, require extensive post-build inspections to validate part safety and specifications, which often creates more questions than answers. Mostow believes that Phase3D offers the solution with its integrated, reliable process.
“Our technology is designed to be accessible to everyone. Engineers shouldn’t need to run machines—we should be able to operate additive machines safely and effectively at production scale,” said Mostow. “Today, you may know how to run the machine, but when an issue arises, what do you do with that? Phase3D is breaking down those barriers so we can know exactly what happens during the process.”
How Fringe Inspection works
Fringe Inspection begins by aligning with each customer’s specifications. It uses a camera and projector, mounted outside the build chamber using available ports, to create a detailed heatmap. The system records and monitors the entire build process layer by layer, from powder spreading to melting, and quantifies how much powder was spread across the entire layer.
According to Mostow, this unique ISM tool saves time and costs by detecting anomalies in real-time, reducing lead times and scrap, streamlining parameter selection, and signaling when printer maintenance is necessary.
“It all boils down to time and money, which are the most important factors for any business. Our technology performs root cause analysis quickly, which is key for parameter development and product advancement,” he added.
Standardizing AM processes
Mostow also foresees that Fringe Inspection will address another significant technological gap: process standardization across laser powder bed fusion machines. This lack of standardization often leads to longer lead times.
“We need to quantify what’s happening during the process so that whether the machine is in Youngstown, Ohio, Denver, Colorado, or even on a naval ship in the middle of the ocean, the measurements are consistent,” Mostow explained.
Advancing AM inspection through strategic collaboration
In addition to its advanced inspection capabilities, Phase3D’s strategic partnerships have helped bolster its Fringe Inspection product suite while contributing to the broader AM industry. Notable collaborations include partnerships with DMG MORI, NASA, Oak Ridge National Laboratory, the Department of Defense, and America Makes.
Recently, Phase3D was awarded a Phase 1 contract through the Small Business Technology Transfer program, in collaboration with the U.S. Air Force Research Laboratory. The company is working with the University of Dayton Research Institute to conduct advanced research into AM quality inspection. The project aims to integrate data from various sensors to identify correlations between build anomalies and part defects, ultimately reducing scrap rates and enhancing project lead times, machine utilization, and overall yield.
“We aim to gain better control over the process, understand what’s happening, and improve it—improvements that directly benefit the end user. We believe our data is the key to unlocking this understanding and improving the entire process for all AM users,” said Mostow.
Shaping the future of AM component inspection
Phase3D is at the forefront of developing an accurate method for component inspection, addressing a longstanding challenge in the AM industry. By focusing on real-time monitoring and providing actionable insights, the company ensures more precise defect identification, leading to improved efficiency, quality, and innovation. These advancements not only benefit individual businesses but have the potential to strengthen the entire AM ecosystem. As AM continues to grow, Phase3D believes that prioritizing quality is essential for maintaining U.S. competitiveness in the global market.
“The industry often focuses on speed and scale over quality. It’s crucial to prioritize quality assurance and real-time inspection, and to educate on what’s achievable today,” Mostow concluded.
Source: