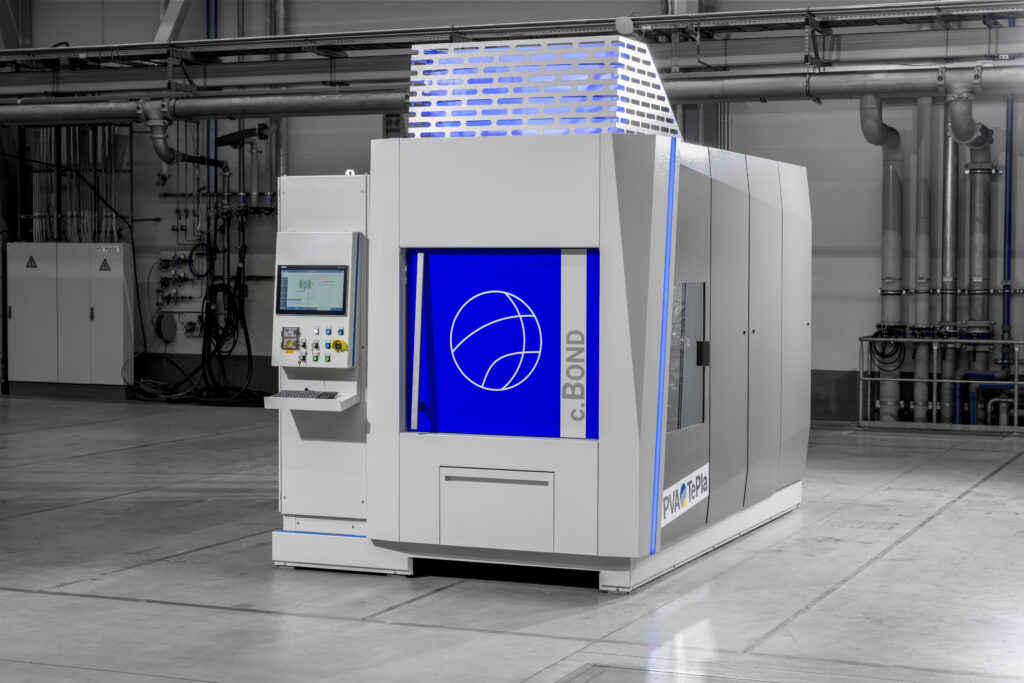
The technique ensures precise and uniform bonding by using advanced software and feedback sensors. (Photo courtesy PVA TePla)
An innovative process is reducing diffusion bonding time of aluminum and aluminum alloys by up to 50 percent, energy use by 30 percent, and improving quality.
By Del Williams
Contract manufacturers and design engineers in the aerospace, semiconductor, high-power electronics, and energy industries have been turning to diffusion bonded metals to produce new cutting-edge innovations.
Diffusion bonding is an essential joining method used to achieve a high-purity interface when two similar or dissimilar metals require superior structural integrity, and a traditional brazing approach fails to yield quality results. The process involves applying high temperature and pressure to metals mated together in a hot press, which causes the atoms on solid metallic surfaces to intersperse and bond.
Today, much of the innovation occurring in either high-demand or high-quality industrial sectors involves aluminum as one or more of the layers of metals that are bonded. Aluminum, and its broad family of alloys, is prized as a lightweight metal with strong structural integrity, high electrical and thermal conductivity, corrosion resistance, and a malleability that makes it easy to shape.
Aluminum’s unique blend of lightness, strength, and purity makes it indispensable across various industries. In aerospace, its high strength-to-weight ratio is crucial for structural components. For semiconductor equipment, aluminum enables the fabrication of intricate, contamination-free channels essential for gas and fluid flow, avoiding the impurities inherent in traditional joining methods like brazing or welding.
Furthermore, aluminum’s compatibility with diffusion bonding allows for the creation of complex cooling channels in high-power electronics, injection molds, and specialized heat exchangers—designs often impossible to achieve through conventional machining.
Unfortunately, the characteristics of aluminum present a challenge for the traditional diffusion bonding process, which involves the application of radiant heat into the metal layers while in a vacuum furnace. Aluminum tends to reflect radiant heat and has a relatively low melting point in relation to the temperatures that must be achieved for proper diffusion bonding.
Engineers cleverly confronted the issue by developing a conductive heating method that more rapidly reaches bonding temperature. This new approach offers an alternative to traditional diffusion bonding by circumventing the slow process of radiant heating structural assemblies in a vacuum environment.
The c.BOND machine utilizes precisely controlled heat conduction, instead of radiation, to enable high speed production of aluminum-to-aluminum, or aluminum-to-dissimilar material parts. After several years of developmental research, the c.BOND tool can now reduce total diffusion bonding process time essentially in half, thus reducing the energy required during processing by as much as 30 percent. This also improves the quality of the bond in certain instances.
Expediting Aluminum Diffusion Bonding
In the traditional diffusion bonding process, a vacuum furnace provides radiant heat to the surface of the part. Subsequently, the heat is conducted through the assembly and transmitted to the faying surface where required. However, when radiation becomes the dominant form of heat transfer, particularly at relatively lower temperatures in vacuum, below 600°C, aluminum’s thermal conductivity is time consuming.
Aluminum excels at conducting heat, particularly at lower temperatures, making it ideal for applications requiring efficient heat dissipation, such as in electronics and automotive components.
“Aluminum’s high reflectivity poses a challenge in traditional diffusion bonding. It’s like trying to heat a mirror with a spotlight—the energy is reflected away instead of being absorbed into the material [using the traditional diffusion bonding process],” said Horst-Gunter Leng, product manager for PVA TePla, a global manufacturer of industrial furnaces and PulsPlasma nitriding systems.
Horst-Gunter Leng added that diffusion bonding of aluminum requires superior temperature control throughout the process. To prevent overheating of the load, slow heating rates traditionally are applied, leading to long process times.
In addition, aluminum alloys have a narrow processing temperature range for successful bonding. When temperatures fall outside that critical temperature band, a poor bond is produced.
To overcome the existing challenges of bonding aluminum, PVA TePla and its partner initiated an extensive development program and came up with an innovative solution: integrating heating elements directly into the press platens.
“This approach speeds up the bonding process, and significantly enhances efficiency by directly transferring heat to the aluminum components,” Horst-Gunter Leng explained.
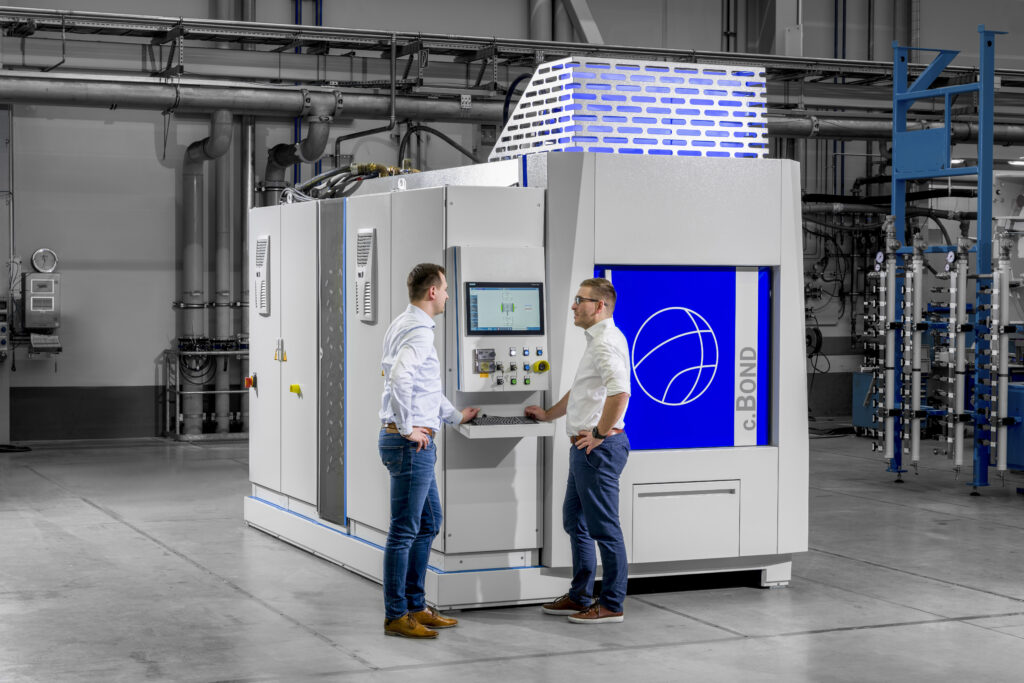
This innovation in diffusion bonding is crucial in industries like aerospace and semiconductors, where aluminum’s light weight and conductive properties are valuable but can be challenging to bond traditionally. (Photo courtesy PVA TePla)
The culmination of extensive research and development, the c.BOND machine features a unique combination of direct conduction heating through the top and bottom platens, which are in contact with the assembly. This innovative design is said to ensure bi-directional homogenous heating and more precise temperature at the bonding interface, where it is required.
The c.BOND machine uses a hot-press tool with advanced software and feedback sensors to achieve micrometer-precise pressure control across the entire component surface. This ensures uniform bonding over large areas. Furthermore, the system allows for selective heating of specific areas, preventing unnecessary heat exposure to other parts of the component.
The high-vacuum atmosphere within the chamber eliminates contamination and prevents voids in the bonded joint.
“With the [c.BOND], the time to heat the part to the ideal temperature for bonding is cut in half compared to traditional radiant heating. With less processing time required, the energy requirements are reduced by up to 30 percent as well,” said Horst-Gunter Leng. He noted that multilayer stacking is also possible, which can further increase productivity.
The c.BOND technology demonstrates significant quality improvement of bonded aluminum components. The technology improves temperature homogenity in the load by 70 percent, which enhances bonding across the the entire surface. The technology also improves the parallelism of parts by 50 percent, which enhances the accuracy of geometric dimensions, tolerances, and product specifications.
According to Horst-Gunter Leng, the c.BOND furnace technology by PVA TePla is commercially available today for high volume production. The innovative furnace technology incorporates another feature unique to the industry, utilizing PVA TePla’s proprietary automatic bonding software (ABP).
— Horst-Gunter Leng, product manager for PVA TePla
“With the automatic bonding software, you place your parts in the furnace, input a few parameters such as the size of the bonding area, and the software calculates automatically the optimum processing parameters. No specific diffusion bonding knowledge from the operator is required,” said Horst-Gunter Leng.
He noted that the recipes can be modified according to the type of material being bonded, the thickness of the material, its surfaces, and other factors. During the process, the software continuously monitors the process in real-time and adjusts parameters accordingly.
A c.BOND unit is installed at a national research facility in Germany, The Günter Köhler Institute for Joining Technology and Materials Testing (ifw Jena). The Institute is an independent, non-university industrial research institution that conducts research in diffusion bonding, additive manufacturing, brazing, welding, laser processing, material science, and other forms of bonding.
The c.BOND system is compact, requires minimal maintenance, and enables high-volume production of aluminum components for diverse industries. Its benefits are being realized in aerospace, where it creates lightweight yet strong aircraft components. In the semiconductor industry, it provides a cleaner alternative to brazing, eliminating the risk of solder contamination. There is also growing demand for diffusion-bonded aluminum heat sinks, crucial for cooling high-power silicon carbide (SiC) electronics.
Diffusion bonding also has applications for conformal cooling. The concept is to bond layers of sheet metal that contain machined channel/microchannel structures. When combined, the channels provide a path for heat dissipation. Current applications include power electronics for effective heat management and rapid cooling of molds utilized in injection and blow molding processes.
With the size of components continually getting smaller in sectors like semiconductors and electronics, controlling the amount of time—and, by extension, heat—introduced into the part becomes more critical.
“As the features [of the internal channels] become more miniaturized, it becomes even more important to control the heating during the diffusion bonding process to avoid any distortion in the part,” said Horst-Gunter Leng. “If you can shorten the cycle time, you introduce less heat into the part. This will facilitate creating parts with conformal cooling channels that have finer and finer features.”
Diffusion bonding is increasingly valuable for joining dissimilar metals, such as aluminum to steel or titanium. This allows engineers to design components and assemblies with the best properties of each metal.
For example, one metal might offer superior corrosion resistance while the other provides greater strength. This “packaging” of dissimilar metals opens up new possibilities in design, particularly for overall weight reduction of design and enhancing performance in challenging environments.
When joining dissimilar surfaces, a liquid-phase diffusion bonding process is utilized, particularly when the bonding interface extends beyond R&D sized samples. This often involves an interlayer of an alloy that typically melts at the faying surfaces. When the interlayer includes aluminum, the c.BOND can deliver controlled heat to increase the bonding speed.
Although the c.BOND technology is designed to improve the diffusion bonding of aluminum, PVA TePla can design the machine around the specific needs of the customer. It can be customized for the alloy, including copper, which has many applications in specialized heat exchangers or for products used in the microelectronics industry. The company is exploring options to modify the c.BOND to achieve even higher temperatures above the current maximum of 800°C, according to Horst-Gunter Leng.
As diffusion bonding of aluminum gains importance across industries, contract manufacturers and design engineers must embrace the latest advancements to remain competitive. By adopting fast, energy-efficient diffusion bonding technologies for aluminum and other materials, they can unlock higher production volumes, reduce costs, improve or achieve global sustainability targets, and realize increased profitability.
Del Williams is a technical writer based in Torrance, California.