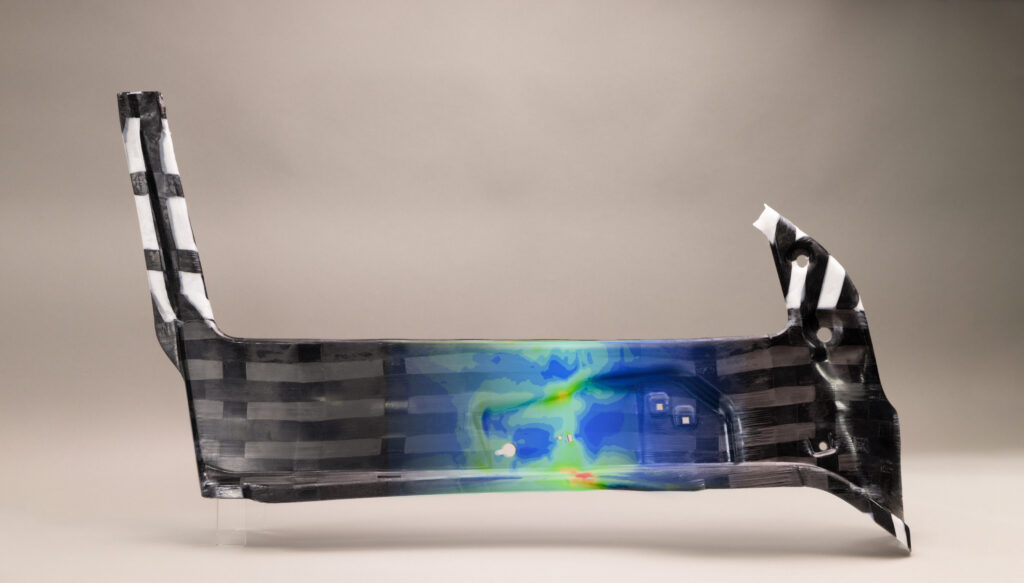
A beltline stiffener produced by the WEAV3D process. (Photo courtesy WEAV3D)
The partnership of WEAV3D, Braskem, and Clemson Composites Center won the Altair Enlighten 2024 Future of Lightweighting Award for a technical achievement that combines Braskem’s polypropylene sheets with WEAV3D’s lattice technology.
PHILADELPHIA—The Altair Enlighten 2024 Future of Lightweighting Award turned the spotlight recently to a partnership involving polyolefins producer Braskem, the advanced manufacturing and materials startup WEAV3D Inc., and the Clemson Composites Center at Clemson University. The three entities were named first place winners of the award for a cost-effective lightweight technology designed to enhance the performance of polypropylene (PP) for structural automotive applications, according to a release from Braskem North America.
The combination of WEAV3D’s composite lattice reinforcement—Rebar for Plastics®—and Braskem PP reportedly enables thermoplastic that is lighter and less expensive than conventional organosheet. It is said to unlock new opportunities for cost-effective replacement of sheet metal structures with thermoplastics throughout the vehicle.
“Braskem is honored to be recognized by Altair as the winner of the 2024 Future of Lightweighting category, which recognizes new material technologies that have significant potential to transform and advance vehicle lightweighting,” said Joel Carr, technical service and development engineering team leader at Braskem America, in the release. “The partnership between WEAV3D, Clemson Composites Center, and Braskem combined to create a truly innovative material that provides for more sustainable lightweight solution to help reduce vehicle carbon emissions—all while enhancing manufacturing process value through material cost savings. This is a win-win for our clients and the planet.”
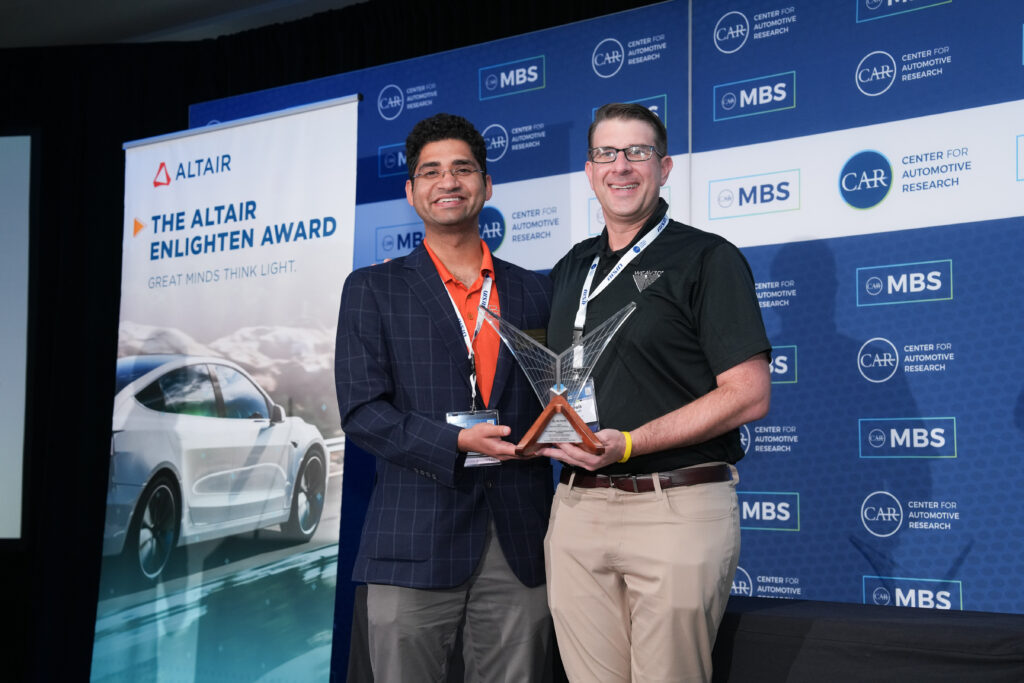
(Left to right) Sai Aditya Pradeep, former manufacturing applications engineer and project lead at the Clemson Composites Center, and WEAV3D CEO Lewis Motion accept the Altair Enlighten 2024 Future of Lightweighting Award. (Photo courtesy WEAV3D)
The Altair Enlighten Award honors sustainability and lightweighting advancements that successfully reduce carbon footprint, mitigate water and energy consumption, and leverage material reuse and recycling efforts. By showcasing technology innovations dedicated to sustainability, the Enlighten Award garners interest from industry, engineering, policymakers, educators, students, and the public alike. The award, presented annually in conjunction with the Center for Automotive Research (CAR), was presented in August at the CAR Management Briefing Seminars.
“We are incredibly grateful to Altair and CAR for selecting us for such a prestigious award,” said Christopher Oberste, president and chief engineer of WEAV3D Inc., in the release. “This award validates the technical development and commercialization progress we have achieved over the past several years and recognizes the importance of WEAV3D’s cost-effective lightweighting technology as part of the future of sustainable mobility. Using the right material in the right place keeps cost and waste low, while still delivering substantial weight savings and performance benefits to our automotive customers.”
Combining WEAV3D’s Rebar for Plastics with Braskem Polypropylene is said to provide multiple benefits versus conventional composite organosheet, including reducing sheet blank weight by about 50 percent and final part weight by approximately 23 percent. The combination is also reported to reduce costs by about 50 percent and to increase sheet yield from 25 percent to 45 percent by weight, resulting in a 62 percent reduction in trim waste.
Sai Aditya Pradeep, former manufacturing applications engineer and project lead for the Clemson Composites Center, said in the release that the collaboration leveraged Clemson’s “extensive experience in stamp-forming thermoplastic composites from the U.S. Department of Energy’s Ultra-Lightweight Door program.”
“We collaborated with WEAV3D and Braskem to develop an industry-first, high-rate structural automotive prototype that showcases WEAV3D’s tunable woven composite technology and Braskem’s cost-effective PP resin,” he stated.
WEAV3D, headquartered in Norcross, Georgia, originated as a technology startup within the Materials Science and Engineering department at the Georgia Institute of Technology. Its innovations in composite materials, manufacturing processes, and processing equipment are reported to enable companies in industries such as automotive, aircraft, wind turbines, and cargo transportation to produce parts that are lighter, stronger and less expensive.
The company’s patent-pending WEAV3D composite forming process is said to enable production of optimized lattice structures that can be combined with injection molding or thermoforming processes to create lightweight structural composite parts at a fraction of the cost and cycle time associated with traditional composite manufacturing.