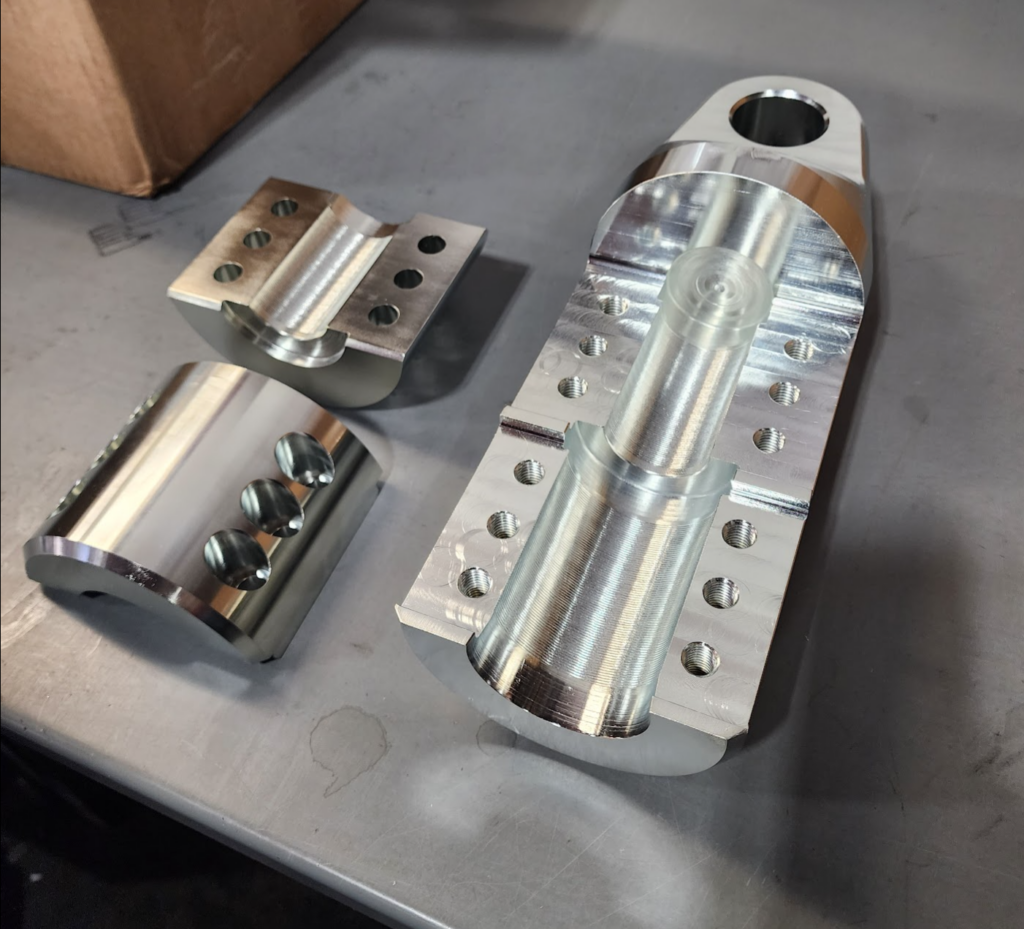
Badger Metal & Machine Fabrication’s capabilities range from tight-tolerance part manufacturing (above) to complex, turnkey machine-building projects (below). Image courtesy Badger Metal & Machine Fabrication.
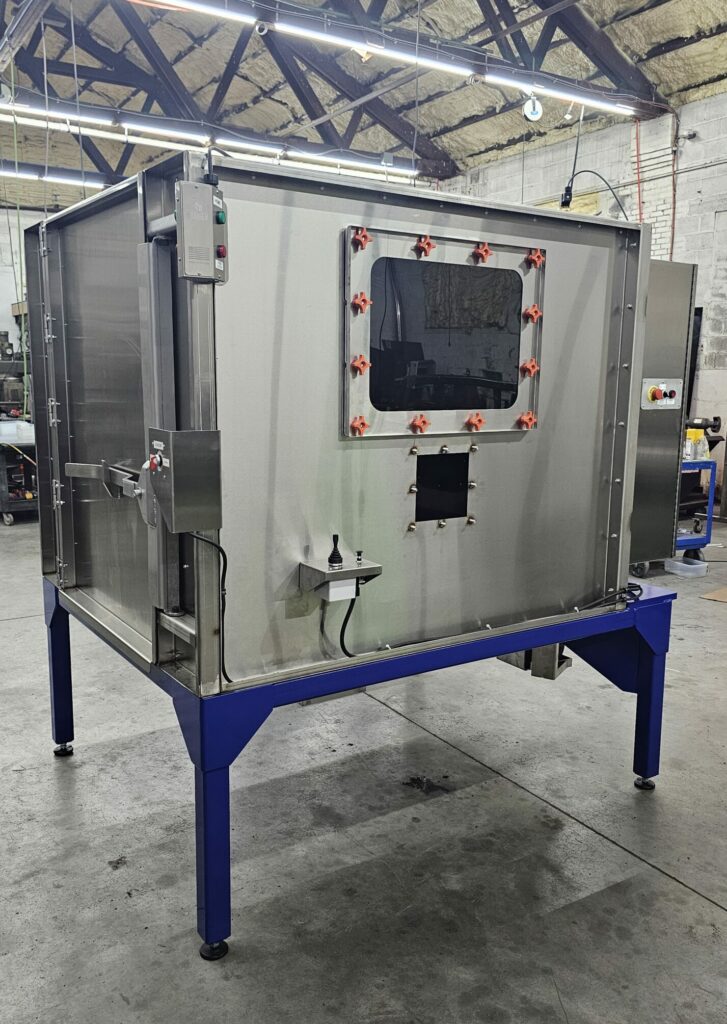
Image courtesy Badger Metal & Machine Fabrication.
Badger Metal & Machine Fabrication applies diverse capabilities to craft high-quality parts and build custom machines.
By Mark Shortt
RIVERDALE, N.J.—A dynamic metal fabrication company in northern New Jersey is making its mark with a rare skillset and enthusiastic embrace of cutting-edge manufacturing technology.
Badger Metal & Machine Fabrication, a sheet metal fabrication shop with an experienced staff of mechanical engineers, offers diverse in-house services to a customer base of primarily OEMs and design and engineering firms. The company’s capabilities span waterjet cutting, plate rolling, metal forming, and CNC milling and turning, as well as welding and laser engraving.
“As a job shop, we have the opportunity to fabricate a wide variety of components and are almost always working on something new and exciting,” said Abraham (Abe) Ingersoll, president of Badger Metal & Machine Fabrication, in an e-mailed response to Design-2-Part. “We are highly experienced in building machine enclosures and complex, precise weldments.”
Ingersoll said Badger helps its customers refine their parts for manufacturing, often recommending ways to improve the cost and quality of their products.
“Bridging the gap between the design team and the people and machines making the physical components is a crucial aspect of manufacturing that is often overlooked,” he said. “Whether our customer needs a simple component or a complex machine based on just an idea, we can make it happen.“
Capabilities for parts manufacturing, machine building
Badger Metal & Machine also designs and manufactures robot and CNC fixtures used by other production-focused manufacturers. But unlike most parts manufacturers, Badger is capable of manufacturing full-fledged custom machinery, as well as high-quality parts. In recent years, the company has successfully completed several complex, turnkey machine-building projects. The machines were completely designed and manufactured in-house.
“These custom machines are now running in our customers’ facilities, streamlining their processes, improving throughput, and reducing downtime,” Ingersoll said.
On the job shop side, Badger Metal & Machine recently added a 3kW plate laser to its fabrication shop, and also added a second and third laser welding system to keep up with demand, according to Ingersoll. In the last year, the company also added two more CNC mills to its machine shop. Badger employs 12 team members at its 10,000-square-foot production facility in Riverton.
“Currently, our main focus is on building quality parts for machine manufacturers, designers, engineering companies—mostly low-volume orders, a lot of ones and twos,” Ingersoll said in a recent Capacity Podcast interview with Sunny Han, CEO of cloud manufacturing software company Fulcrum. “We do a mix of precision sheet metal, CNC milling and turning, a lot of welding. We just got into wire EDM, [and we’re] into laser welding now.”
Identifying needs for new technologies
Whether it’s a 5-axis waterjet, precision bending equipment, or a new laser welding system, Ingersoll keeps a watchful eye out for new and innovative technologies that could benefit Badger’s manufacturing operations in some way, whether they have a current need for it or not.
“Especially with the new tech, it’s not always because you have a job for it—it’s because you see the need or see the potential for a need,” Ingersoll told Han, referring to Badger’s decision making process for purchasing capital equipment. “The newer shops that are adopting the new technology—and the older ones, too—are going to surpass everybody.
“Take laser welding, for instance. There’s nothing that can hold a candle to it. If you’re doing sheet metal and you don’t have laser welding in-house, you’re going to get left behind.”
The effectiveness of laser welding has led Badger to “almost phase out” the use of TIG welding on sheet metal, Ingersoll added. “We’re getting things done in a third of the time. It’s better quality, customers are happier. You can make a better part for less money in less time.”
As an early adopter of laser welding technology, Badger Metal produces “ultra-high-quality” welded sheet metal components, such as hoppers, chutes, and machine enclosures, Ingersoll told Design-2-Part in his emailed response. Laser welding not only enhances the overall strength and quality of the components, it reduces welding and post-weld processing time by up to 75 percent, he said.
According to Ingersoll, Badger Metal’s biggest strength lies in its extensive range of in-house equipment and experience, which enable its team to efficiently bring complex parts through production. “We offer exceptionally short lead times when required,” he said, adding that Badger taps into a large network of vendors to expedite parts that require external processes like heat treating or coating.
One of the company’s workhorses is a Flow Mach 500 5-axis waterjet cutting system, described by the manufacturer, Flow International Corp., as the “fastest, quickest, most accurate waterjet by design.” Badger uses the waterjet to produce high-quality parts with complex geometries—parts that were traditionally machined from large metal blanks on CNC milling machines. Its approach significantly reduces material usage and minimizes fixturing and programming time, Ingersoll said.
Badger’s welding department uses precision welding tables and fixture systems to fabricate large weldments, such as machine frames, with tolerances of ±0.010 inch across the entire structure. Its machine shop routinely achieves tolerances of ±0.0005 inch with its CNC mills, lathes, and wire EDM machines, he added.
Modifying legacy parts for modern fabrication
Working with its customers’ engineering teams, Badger also assists in modifying new and legacy parts for modern manufacturing equipment. Its team identifies potential improvements and presents them to its customers for review.
“Fabrication machinery is constantly evolving, and it makes sense that the parts we make should evolve as well. Features that were impossible or expensive just a few years ago are now achievable,” Ingersoll said.
The Badger team is happy to help prospective customers, even when it can’t provide the needed service.
“If a purchaser comes to us with a part outside of our capabilities, we strive to recommend other shops better suited to fulfilling their needs,” Ingersoll said. “Building up American manufacturing is a passion we all share at Badger, and we understand that helping other shops grow along with us is beneficial for the industry as a whole.”
Building a machine from scratch
In one case, a customer requested that Badger design and build a machine for post-processing aluminum castings. The existing machine, Ingersoll said, was “old, unreliable, and difficult to maintain, causing a major bottleneck in production.”
The new machine would need to be simple to use, easy to maintain, and highly reliable in its ability to safely process parts weighing up to 800 pounds. It also carried a strict lead time: The design and manufacture of the first machine would need to be completed in six months. To build the machine, Badger committed to using commercially available components wherever possible.
“The most challenging problem was designing moving assemblies that would endure long-term in a wet, dirty environment. The process involves high-pressure water and abrasive sand, both of which presented significant challenges that required creative solutions,” Ingersoll said.
Badger’s team worked with its customer’s management team and production floor operators to develop a workable design.
“With simplicity in mind, we designed this project around our standard tooling. No custom solutions were required,” Ingersoll said. “Once the rough design was established, our in-house engineering staff worked together through rapid iterations to refine the details and prepare for production.”
Badger brought to bear several of its manufacturing processes, including laser and waterjet cutting; brake forming; laser, MIG, and TIG welding, CNC milling and turning; and mechanical and electrical assembly. The primary material was T304 stainless steel, but steel and aluminum were also used where required, Ingersoll told D2P.
Badger’s team, combining decades of experience with cutting-edge machinery and processes, succeeded in developing a product that met its customer’s needs “perfectly,” he said.
“We also designed, assembled, wired, and programmed the control system and user interface. This project involved the entire shop, and each work center had at least some role to play. The team outdid themselves working together to achieve success for our customer.”