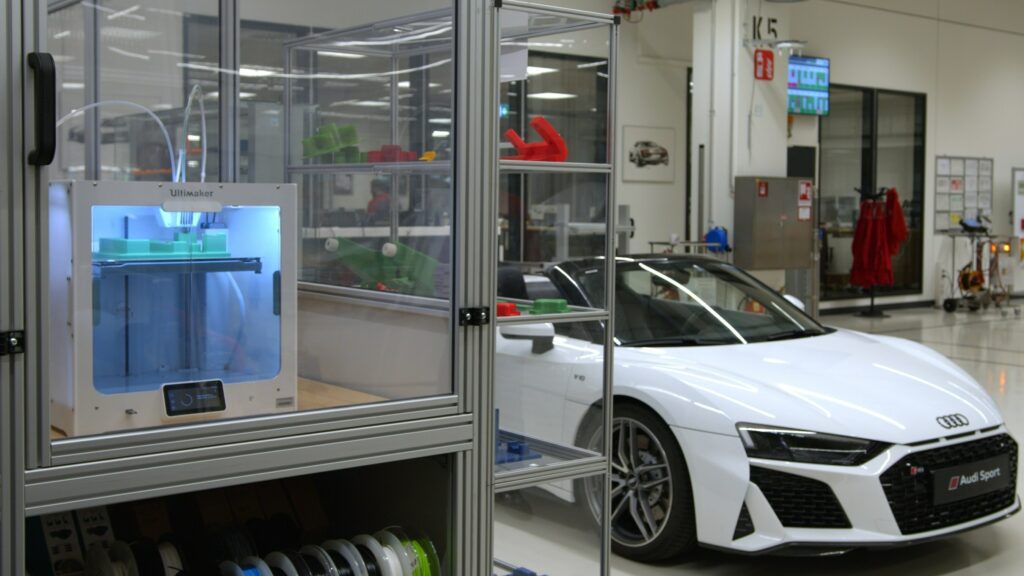
By leveraging Trinckle design automation software and UltiMaker’s 3D printers, Audi Sport simplified its design and production processes, significantly reducing costs and lead times. (Image: PRNewswire)
The automaker is leveraging tools from UltiMaker and Trinckle to improve its manufacturing workflow.
NEW YORK and GELDERMALSEN, Netherlands—When Audi Sport needed to rapidly create nearly 200 new tools to produce the Audi E-Tron GT at the manufacturer’s Böllinger Höfe facility in Heilbronn, Germany, traditional methods fell short. The conventional process of designing and outsourcing production of these essential components often took weeks to months, causing delays and inefficiencies in the assembly line, according to a release from 3D printing technology company UltiMaker.
UltiMaker, along with design automation software firm Trinckle (stylized as trinckle), produced a case study that highlights the impact that 3D printing and design automation software have had on Audi Sport’s manufacturing workflow.
Leveraging Trinckle’s Fixturemate software, Audi Sport designed customized fixtures for assembly in a matter of minutes, compared to the hours typically spent with traditional CAD software. The software, described as user-friendly, is reported to have simplified the design process, allowing for precise and easy-to-produce tools, jigs and fixtures.
Audi Sport then brought these designs to life through 3D printing. Equipped with UltiMaker S series 3D printers, the Audi Sport factory now includes a 3D printing room capable of producing the necessary tools in a single day—a feat that previously took weeks or even months through outsourcing, according to UltiMaker.
The benefits of this approach are said to extend beyond just speed. With access to the UltiMaker Marketplace and its wide range of third-party materials, Audi Sport can ensure the durability and functionality of its applications to withstand the rigors of automotive assembly while also protecting delicate components from damage. UltiMaker Cura simplifies the printing process, providing optimized print profiles for effortless preparation of parts, according to the release.
By embracing 3D printing for tools, Audi Sport has reportedly reduced costs by more than 80 percent while reducing lead times significantly, ensuring that workers have the tools they need when they need them. The combination of UltiMaker’s ecosystem and Trinckle’s software has made fixture design easier, “empowering anyone to create custom parts and reap the benefits of enhanced efficiency and productivity,” UltiMaker said in the release.