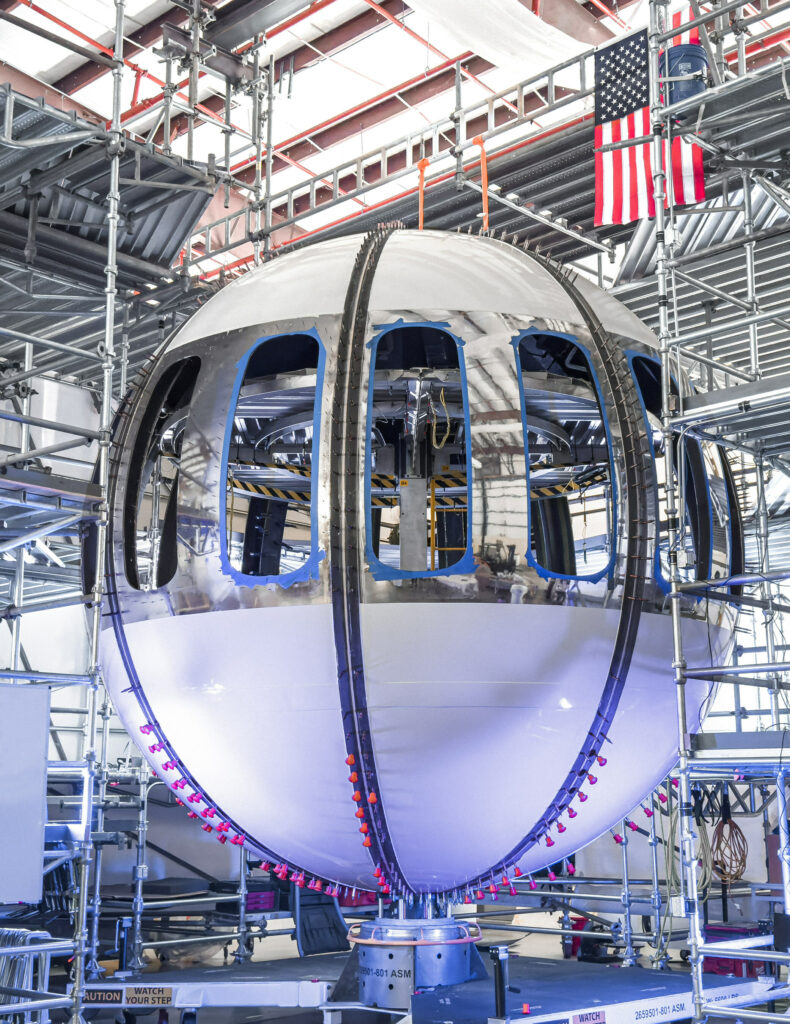
Manufacturing of the Spaceship Neptune test capsule is performed at Space Perspective’s Melbourne, Florida facility, followed by component integration at its capsule assembly facility at Mission Control near Cape Canaveral. (Photo courtesy Space Perspective/PRNewswire)
Foreign and domestic manufacturers are increasingly choosing to manufacture in the U.S.
By Mark Shortt
The United States continues to experience a record-breaking surge of reshored manufacturing and foreign direct investment (FDI), with international geopolitical risks and domestic industrial policy driving the trend, according to the latest data report from the Reshoring Initiative.
The Reshoring Initiative is an organization dedicated to bringing manufacturing back to America. It identified more than 800 cases of reshoring and FDI during the first half of 2023 (1H 2023), the most recent period for which figures were published. That influx of manufacturing created some 182,000 new jobs in the United States, the Initiative said in its 1H 2023 Report.
The risks of geopolitical disruptions are causing companies to “reevaluate supply chain priorities,” the report said. It cites Chief Executive magazine’s 2023 survey as confirming “geopolitical risk exposure” to be the top driver of reshoring manufacturing to America. The Reshoring Initiative defined geopolitical risk (GPR) as the “probability in one year of a major disruption in trade, resulting in the cessation of imports from that country to the U.S. as a result of an adverse geopolitical event.”
To help manufacturers weigh the risks of geopolitical disruptions, the Reshoring Initiative developed a Geopolitical Risk measure. It is planning to include the geopolitical risk factor in an updated version of its Total Cost of Ownership (TCO) Estimator, expected to be available early in 2024.
Long a useful tool for identifying hidden costs of offshoring, the TCO Estimator will be revised to “use geopolitical risk to calculate the expected value of lost margin on revenue lost due to stocking out of a component or product.” Including that cost in the total cost estimate can help companies decide whether it makes sense to bring their manufacturing to the U.S., according to the report.
The latest available reshoring and FDI job numbers for 2023 are reported to demonstrate “exceptional progress for U.S. manufacturing after decades of offshoring.”
“If this progress can be combined with an industrial policy that supports greater cost competitiveness, we will continue our rapid strengthening of U.S. supply chains,” the Reshoring Initiative said in a release highlighting data from the report.
The multi-year rise in reshoring is reflected in OEMs’ sourcing and siting decisions. While some OEMs have decided to source domestically, others are building new factories in America. Much of the construction is triggered by the incentives offered in a trio of newly enacted laws designed, in part, to spur domestic manufacturing: the Chips and Science Act, the Inflation Reduction Act, and the Infrastructure Investment and Jobs Act.
“In the first quarter of 2023, average spending on U.S. factory construction was more than double the average from the past 17 years,” according to the 1H 2023 Report.
These incentives have ignited a boom in U.S. manufacturing investment, the bulk of it directed toward constructing new facilities for production of electric vehicles (EVs) and EV batteries, semiconductor chips, and solar panels and modules.
Also gaining traction are investments in domestic manufacturing of broadband network electronics products and hardware systems, supported by more than $42 billion in funding by the Bipartisan Infrastructure Law’s Broadband Equity, Access, and Deployment (BEAD) Program. Companies such as Nokia, Adtran, Ciena, Calix, and Prysmian Group have announced plans to manufacture broadband network products in the U.S., supporting broadband service providers by meeting the Build America, Buy America provisions of the BEAD Program.
In an interview with Design-2-Part in January, Reshoring Initiative President Harry Moser tapped the brakes on expectations that the numbers of manufacturing jobs resulting from reshoring and FDI would continue at the present record-breaking rate. The 1H 2023 report projected year-end totals exceeding 1,600 cases of reshoring and foreign direct investment, along with 365,000 new jobs.
“We have preliminary end of year statistics, and the second half was not as strong as the first half, and so the total is definitely down from 2022,” Moser said. “I think it’s going to turn out that the chips and battery announcements have fallen off, especially in the second half.”
Moser attributed the second half fall-off to the high costs of building factories to produce chips and EV batteries, coupled with the fact that the government and companies can only invest so much in construction of factories that can cost anywhere from a billion to tens of billions of dollars.
“The froth in the market, the exuberance, the billions and billions of dollars and the hundreds of thousands of jobs from government funding is going down,” he explained. “That’s where we haven’t done the analysis yet.”
However, underlying data remains “very positive,” Moser said, adding that repeated surveys of companies have shown, unambiguously, that between 60 and 80 percent of the companies say they are reshoring.
“We’re down to the underlying factors—people making engines and tools and real, regular old things that we’ve been making forever, but making them here. The surveys all say that companies are doing that—they’re bringing it back,” he said. “I believe that we’ll at least plateau at a good level, and ideally, start up from that to new peaks, but maybe it’s going to take a couple of years to get to those new peaks.”
Electronics Manufacturer Planning to Reshore from China
In January, a Hauppauge, New York-based manufacturer of connected devices made waves at CES 2024 (formerly known officially as the Consumer Electronics Show) by announcing it will move its electronics manufacturing operations from China to the United States, beginning this year.
Orbic Electronics Manufacturing’s plans to reshore electronics production are part of the company’s Project Patriot initiative, a business strategy to create “Made in America” products while bringing more than 1,000 new, skilled jobs to Suffolk County, New York. Orbic makes a variety of connected devices—including smartphones, tablets, mobile hotspots, and laptops—that are available through wireless network operator Verizon.
The project is supported by the Suffolk County Industrial Development Agency (SCIDA), which preliminarily approved a transaction to assist Orbic in transitioning its operations from China to New York. A $30.8 million investment is expected to help bolster Suffolk County’s thriving manufacturing sector, Orbic said in a release.
“This project is a testament to the Suffolk County IDA’s mission to advance the United States’ manufacturing industry and show the world that Suffolk County is the home of innovation and prosperity,” said Suffolk County IDA Acting Executive Director Kelly Murphy, in the release. “Orbic Electronics is an incredible addition to our thriving roster of more than 2,000 manufacturing companies throughout Suffolk County.” (For more on Orbic, see “Mobile Device Maker to Move Electronics Manufacturing Operations from China to U.S.”)
Irrigation Equipment Manufacturer to Invest More than $50 Million to Expand, Modernize Nebraska Facility
Also in January, a manufacturer of irrigation and infrastructure equipment announced plans to invest more than $50 million over the next two years to expand and modernize its Lindsay, Nebraska facility. Lindsay Corporation Senior Vice President, Global Operations Rich Harold said that as part of its operational excellence journey, Lindsay will be “designing and implementing the factory of the future.”
“This investment will create additional value for our customers, employees, and other stakeholders by allowing us to improve efficiency, enhance product quality through better monitoring and adjustment of production systems, be more responsive to cyclical market needs, address labor availability challenges, and achieve best-in-class performance and service,” Harold said in a release.
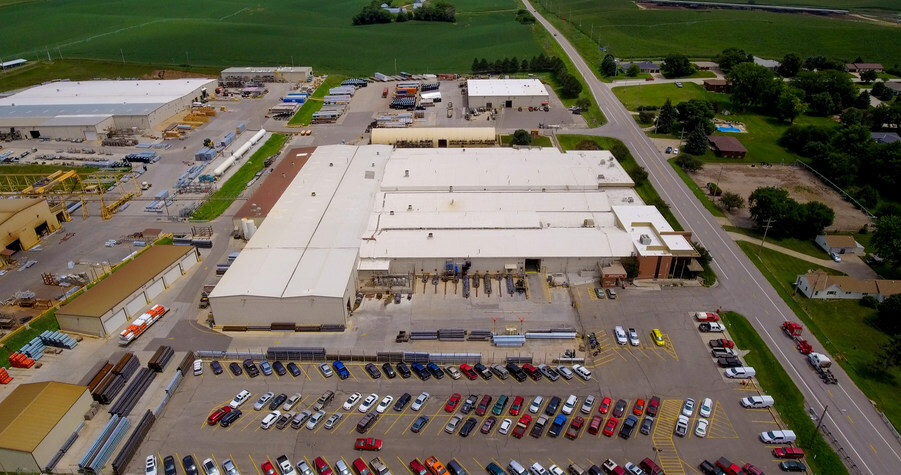
The Lindsay manufacturing facility will undergo a significant expansion to improve efficiency, enhance product quality, and achieve best-in-class performance and service. (Image courtesy Lindsay Corp./PRNewswire)
Lindsay Corporation plans to modernize its facility by implementing Industry 4.0 technologies, including data connectivity, analytics, artificial intelligence, and adding automation and robotics. The facility will house new equipment and the latest advancements in galvanizing, a core process for manufacturing pivot irrigation systems and road safety products. Lindsay will also expand the facility footprint by 40,000 square feet to allow for increased capacity and capabilities in metal forming, the company said in the release.
The investment is reported to be the largest in Lindsay’s history. The company said it expects to begin capital spending in the second quarter of fiscal 2024 and complete the facility modernization by the end of 2025.
Also active in the transportation industry, Lindsay Transportation Solutions manufactures equipment to improve road safety and keep traffic moving on the world’s roads, bridges, and tunnels.
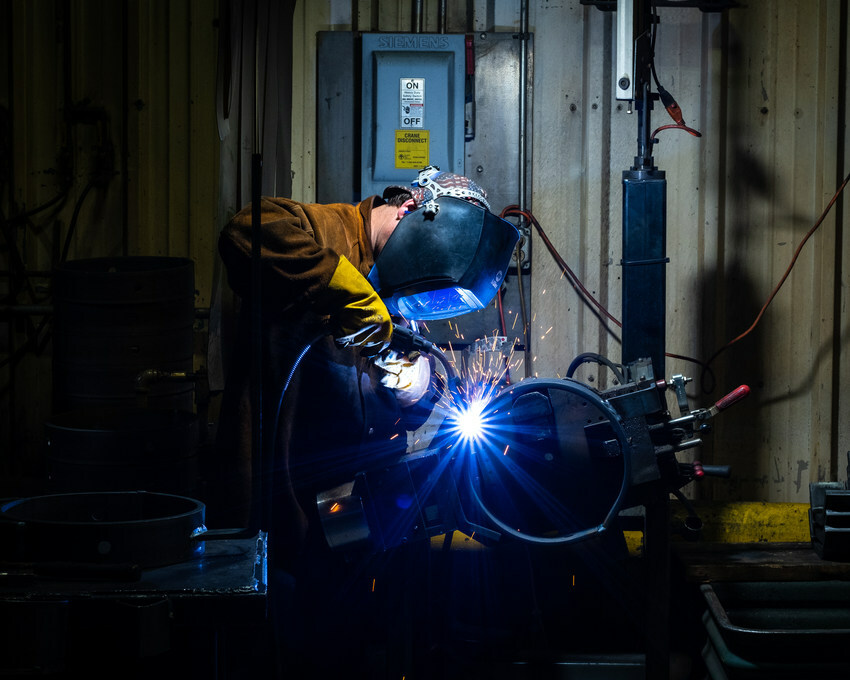
Lindsay Corporation employee Craig Engel completes complex welding work on site at the Lindsay, Neb., manufacturing facility. The plant will undergo a historic expansion and renovation beginning in 2024. (Image courtesy Lindsay Corp./PRNewswire)
A Tighter, More Collaborative Design-to-Manufacturing Process
A key advantage of onshore manufacturing is the closer proximity of manufacturers—and their engineers—to the teams that designed the products they’re making. When design and manufacturing teams can communicate more easily and more frequently, design iterations are likely to go more smoothly. One company that’s reaping the benefits of such an arrangement is Space Perspective, a company with visions of making space travel “more accessible than ever before.”
The Titusville, Florida-based company manufactures Spaceship Neptune, a carbon-neutral spacecraft designed to take tourists to the edge of space in a spherical, pressurized capsule propelled by a giant balloon, the SpaceBalloon™. Space Perspective succeeded in flying a capsule simulator to space under its SpaceBalloon in 2021. The company reports that since achieving that feat, its teams have been “working on the design and manufacturing of the capsule to resume testing.” The aerospace manufacturer released the first images of its completed test capsule structure in December, highlighting the benefits of a tightly collaborative design-to-manufacturing process.
Space Perspective said the test capsule is scheduled to fly in uncrewed test flights that are expected to pave the way for crewed test flights later this year. The company is planning to use the data gathered during the uncrewed test flights to inform its development of a commercial-grade capsule, according to a release from Space Perspective.
The company said that it developed Spaceship Neptune to be “the most accessible, most sustainable, and safest spacecraft on or above our planet.” Its capsule is reported to remain secured to the SpaceBalloon during the entire flight, from liftoff to splashdown. In this way, it is different from other spacecraft that require the crewed compartment to separate from one flight system mid-flight and transfer to another flight system. This is said to create a “seamless and safe flight, at a fraction of the cost of other space travel options.”
The spacecraft is also reported to feature “the largest windows ever flown to space,” enhancing the experience of viewing Earth from space.
Space Perspective considers itself unique in that it performs most of the manufacturing in-house. Manufacturing for the capsule is done at the company’s Melbourne, Florida facility, followed by component integration at its capsule assembly facility at Mission Control near Cape Canaveral, according to the release.
The company called it a “monumental achievement” to design and manufacture a spherical capsule structure capable of providing panoramic views and operating in numerous different environments. The achievement is seen as a testament to the integrated, collaborative work performed by three of the company’s engineering teams—Structures, Manufacturing, and Design.
Space Perspective Founder, Co-CEO, and Chief Technology Officer Taber MacCallum called the critical internal partnership “one of the greatest iterative collaborations I have ever seen.”
“I’m incredibly proud of our Engineering team,” McCallum said in a statement. “The entire company is hugely motivated by reaching this milestone together and seeing Spaceship Neptune come to life before our eyes so spectacularly.”
Space Perspective builds the balloons for its Spaceship Neptune at a factory on Florida’s Space Coast. The company officially opened the factory, described as a “700-foot long, state-of-the-art manufacturing facility,” last August. At the time of its opening, the Seely SpaceBalloon™ Factory employed 23 people and was aiming to “produce one space balloon a week,” according to Richard Tribou, who reported on the opening for the Orlando Sentinel in his piece, “Space Perspective Opening Out-of-this World Balloon Factory in Florida.”