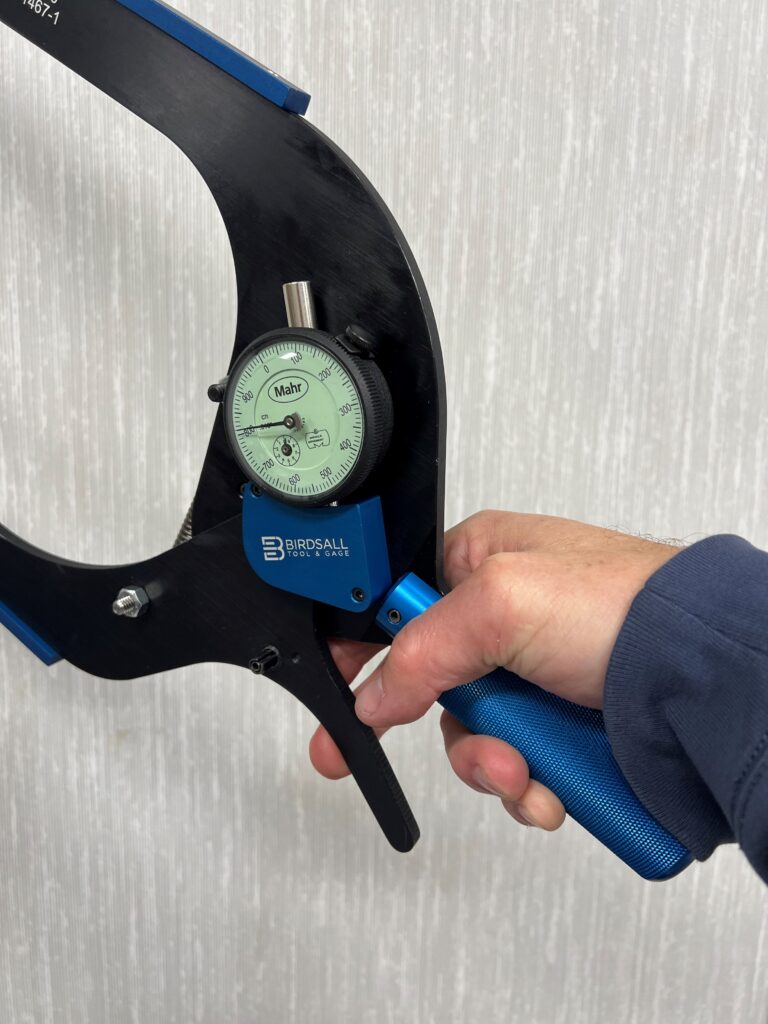
Birdsall Tool & Gage, a provider of custom tool and gage design and manufacturing, can machine gages to +/- 50 millionths, the company said. (Photo courtesy Birdsall Tool & Gage)
Birdsall Tool & Gage offers diverse capabilities for custom design and manufacturing of tools, gages, fixtures, and inspection equipment.
By Mark Shortt
FARMINGTON HILLS, Mich.—Quality has always been a driving force for Birdsall Tool & Gage, a company whose products help its customers improve their measurement and inspection procedures. Birdsall Tool & Gage was founded in 1970 in Livonia, Michigan, where the owner began the business in a garage.
Today, the company is based at a 12,000-square-foot facility in Farmington Hills, where it provides custom tool and gage design and manufacturing, along with prototype and production 3D printing, electrical discharge machining (EDM), and 5-axis milling.
“The gages and tooling are used to check parts,” said Birdsall Tool & Gage CEO and co-owner Todd Mielke, in an emailed response. “Moreover, we can make anything in metal or 3D printed materials for prototype or low volume production. Our tool design leadership can also machine parts.”
Birdsall Tool is certified to ISO 9001:2015 for the design, build, manufacture, and distribution of special tools, gages, fixtures, masters, and inspection equipment, according to its certificate of registration. Mielke is one of three co-owners of the firm. Jordan Birdsall, who heads the sales and estimating department, and Abigail Felice, senior administrator, are also co-owners.
The company can machine gages to +/- 50 millionths, Mielke said, and it can jig or surface grind “to a measure that creates a comfort level for our customers.”
Mielke said Birdsall Tool has the skills to design a tool to check any part feature that needs validation. The skills required to design and build a fully functional tool are unique and powerful, he said, because although customers know how to make their parts, they are often “not sure how to check and validate production quality.”
“It’s one thing to have a gage to check a part; it’s another to have one designed to last and include multiple materials and methods for ultimate customer value,” he said.
In addition to quality and continuous improvement, another value that’s important to the people at Birdsall Tool is trust. On the company’s website, a quote attributed to an unknown source reads, “A team is not a group of people who work together. A team is a group of people who trust each other.”
Mielke said Birdsall Tool’s leadership team understands the “tyranny of the urgent” in the tooling and gage industry, where the unexpected often happens. It’s also an industry where price often determines purchasing decisions. But for Birdsall Tool, success in winning projects is not just based on good pricing, he said.
“We also separate ourselves from the competition by building trust. Trust must be earned, and the best way to earn it is with transparency. We distinguish ourselves by providing more transparency on our job process, which builds trust.”
That transparency is supported by Birdsall’s online system that connects with its customers, providing real time project status without phone calls and email. Its new manufacturing management information system (MIS) connects Birdsall’s accounting function with quoting and projects management.
“Now, we can see the percent completed on every job and project online. We can know when we will be complete with our customer’s project,” Mielke said. The information, he added, helps give the company a competitive advantage.
One company asked Birdsall Tool if they could reverse engineer a caliper gage for a large train wheel because the gage manufacturer had gone out of business years before. No drawings were provided—just an old gage that needed to be reproduced. It had to be able to handle hot forging temperatures and be robust enough to operate in a tough environment, Mielke said.
Using tooling that included a laser cutter, a mill, and a jig, as well as processes such as surface grinding, laser marking, and EDM, Birdsall Tool met the customer’s expectations, and then some.
“Not only did we design and build the prototype successfully, but we were also asked to make 12 more,” Mielke said. “Going beyond just designing gages, we provided a solution and built trust.”
Birdsall Tool has diversified its capabilities by expanding into the realm of 3D printing. The company employs a Markforged X7 3D printer to produce composite parts that are reinforced with continuous carbon fiber, making them exceptionally strong and stiff, yet lightweight. Offering strength comparable to 6061 aluminum at less than half the weight, the parts are well-suited for applications like tooling and manufacturing equipment.
The X7 3D printer can print parts in Onyx™, a chopped carbon fiber-reinforced nylon that can be reinforced with additional layers of continuous carbon fiber or Kevlar® fiber. Parts printed with these materials “are work-capable and ready the same day for a fraction of the cost” of aluminum parts, according to the company’s website.
The X7 is reported to offer “breakthrough quality and precision in 3D printing,” according to the website, which described the X7 as a “top-of-the line industrial grade platform with a dual nozzle print system that supports continuous carbon fiber and Kevlar reinforcement.”
“The X7 conducts laser inspections of the parts mid-print to ensure dimensional accuracy for the most critical tolerances. We are able to hold 0.010 inch tolerances on most dimensions. We can also add a secondary operation to include threaded inserts, and custom machining of dimensions for tighter tolerances,” the company’s website stated.