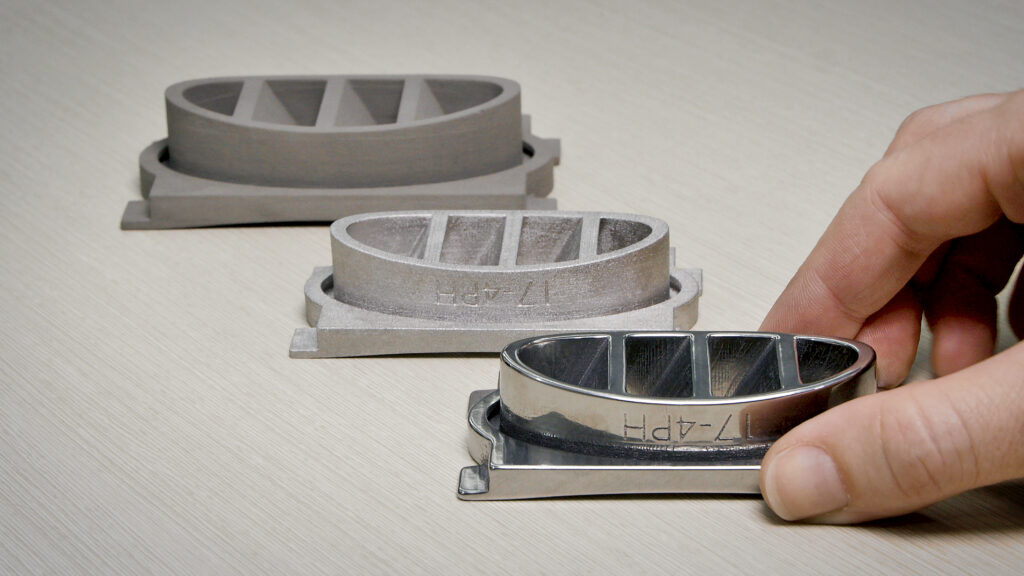
DSB Technologies is now forming metal parts, such as the vent application shown here, with metal binder jetting technology from Desktop Metal. The part at the top shows a “green” 17-4PH stainless steel part out of the printer, and the middle part shows the same part immediately after sintering in a furnace. The final part is shown polished. (Photo: Business Wire)
DSB Technologies uses traditional and additive technologies to process more than 8 million pounds of powder into parts annually. Now, the company is using Desktop Metal’s X-Series metal binder jetting lineup.
BOSTON—Additive manufacturing technologies company Desktop Metal, Inc., reported that Wisconsin-based DSB Technologies (DSB) has adopted Desktop Metal’s complete X-Series metal binder jetting product lineup, including Live Sinter software.
DSB Technologies specializes in producing high-quality metal parts via sinter-based technologies such as powder metallurgy (PM) and metal injection molding (MIM). Now, the company is using Desktop Metal’s InnoventX, X25Pro, and X160Pro to develop and deliver customer parts in a range of metals, including 316L and 17-4PH stainless steels, and 4140 and M2 Tool Steel, according to a release from Desktop Metal. The company is also said to be planning to adopt Desktop Metal binder jetting for aluminum in the future.
“Binder jetting really is a forming technology that gives us unlimited design potential,” said DSB Technologies Chief Operating Officer Paul Hauck, in the release. “We can go from a very simple shape to very complex things you can’t produce in hard tooling, taking complexity beyond what’s possible with metal injection molding. Binder jetting creates applications never produced before, and we want to be a leader in that.”
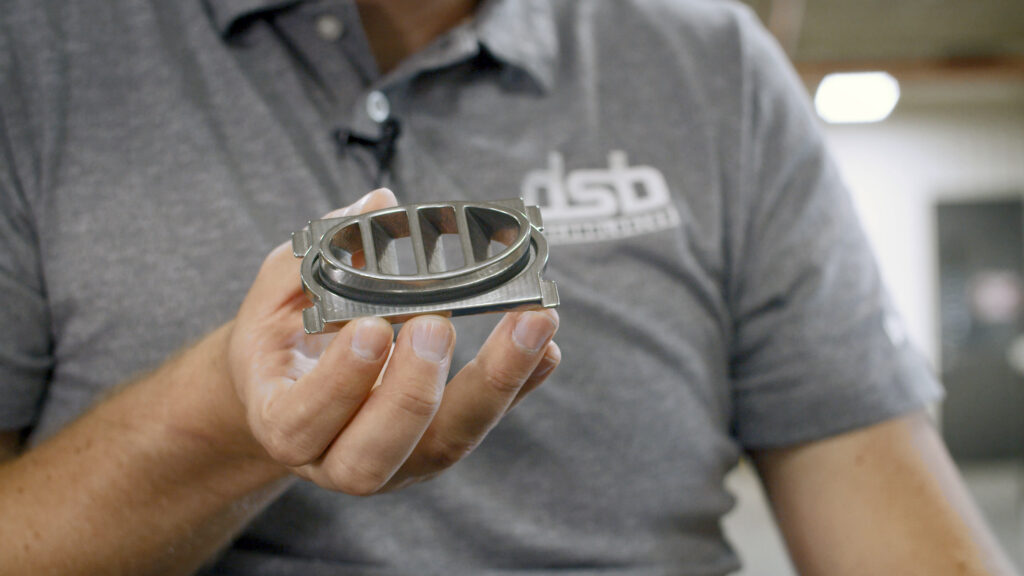
DSB Technologies is now working with customers on new metal part applications and designs, such as this vent application, made possible with metal binder jetting technology from Desktop Metal. (Photo: Business Wire)
DSB Technologies, based in Janesville, Wisconsin, currently serves the aerospace, automotive, defense, electronics, industrial, medical, and sports equipment markets. The company is home to more than 30 high-temperature continuous sintering furnaces—believed to be North America’s largest installed capacity. It also employs post-processing technology to support volume production in metal binder jetting. Of the eight million pounds of metal powder processed by DSB annually, about 90 percent comprise grades of stainless steel, according to the release.
What is metal binder jetting?
In binder jetting, an industrial printhead selectively deposits a binder into a bed of powder metal particles, creating a solid part one thin layer at a time. When printing metal powders, the final bound metal part must be sintered in a furnace to fuse the particles together into a solid object. Desktop Metal said its printers deliver high densities of greater than 97 percent for most metals, in line or better than MIM or gravity castings, depending on the metal.
Binder jet 3D printing technology is widely viewed as a desirable and sustainable production method, largely because of its high speed, low waste and cost, and material flexibility. Desktop Metal printers also binder jet sand and ceramics in high-volume, serial production applications, the company said in the release.
“The exciting part about binder jetting is the path from concept to part is all digital,” Hauck said. “You’re not sending a CAD file over to a tool shop that then creates a reverse image. So, you’re taking as few as eight weeks, and maybe as many as 16 or 20 weeks, out of that process.”
DSB has been phasing in Desktop Metal’s binder jetting technology over the past few years. First installed in 2021, the InnoventX lab-sized printer is used for material development and testing initial sintering parameters. The X25Pro, installed in 2022, allows the team to scale those successful tests up to application development in a mid-size machine that is also capable of bridge production. The X160Pro, installed in 2023, is reported to offer the largest build volume to take applications to serial production.
Live Sinter™ simulation software is critical
While the PM and MIM sectors have long operated with trial and error when sintering powder metal parts, Live Sinter is said to be changing the game of what’s possible with powder metal production. According to Hauck, the software is highly effective in reducing iterations and saving time.
“We now have very useful scientific analytical tools that enable successful outcomes,” Hauck said. “It’s helping us solve application problems, get successful outcomes, and get there faster.”