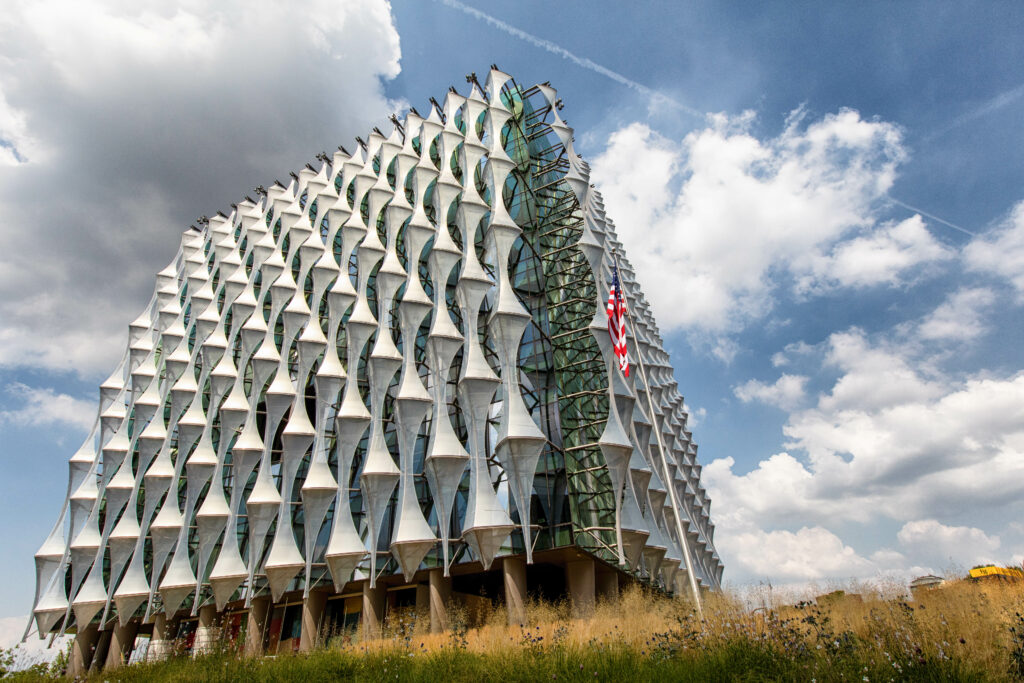
Kubes Steel cut, rolled, and pre-manufactured the shade sail supports that cover the entire façade of this U.S. Embassy building. (Photo courtesy Kubes Steel)
STONEY CREEK, Ontario, Canada—Kubes Steel Inc., is a versatile manufacturer with capabilities spanning structural steel fabrication, rolling and bending, and full-service custom metal fabrication.
The company specializes in rolling and bending steel—capabilities that honed over the past five decades. Today, Kubes owns “one of the industry’s largest collection of rolling and bending machinery,” according to Kubes Steel’s Chris Wyatt. “If a component has a rolled or formed element, we are top of class,” Wyatt said in an emailed response.
Kubes Steel is well known for its expertise in fabricating heavy industrial steel beams, hollow steel structures (HSS), and architecturally exposed structural steel (AESS). According to Wyatt, the company has fabricated large fabricated machined components for hydro turbines; rolled cylinders, such as pilings, casings, and tunneling, for construction projects; rolled extrusions for medical components; tolling for defense contractors and wind turbines; and welded components and frames for solar power.
The company’s full range of metal fabrication services also includes welding, machining, stress relieving, mechanical assembly, blasting, and painting. These services are provided in support of industries such as power generation (hydro, nuclear, oil and gas, solar, and wind); railway; steel making, construction, mining, medical, and defense, among others.
“Our skill set in rolling and bending has been honed over the past five decades, and it shows,” Wyatt said. “Many of our customers have purchased machinery to bring this service in house but find that it requires a skilled operator to produce good quality parts.”
If you’ve watched the Netflix series “The Diplomat,” you already know the quality of work that comes from Kubes Steel.
In the show, you see a U.S. embassy, but behind the screen, Joe Kubes and his team at Kubes Steel cut, rolled, and pre-manufactured the shade sail supports that cover the entire façade of the building. After preparing more than 190,000 curved components and sending them to London, the team at Kubes Steel got to see the fruits of their hard work on the big screen.
When Joe Kubes was in high school, he began working with his father, a talented artisanal steel manufacturer. After a while, the contracts grew, supporting the duo as full-time employees. When Joe took over the business, Kubes Steel was working with local steel mills as an industrial fabricator supplier. Joe knew that it was time and set his sights on something bigger, shifting business priorities to bringing his own vision to life.
Investing in steel rolling and bending machines changed the trajectory of the entire organization, Wyatt said. Instead of working with other suppliers to bend and roll steel, Joe fast-tracked delivery timelines, expanded his offerings, and entered a new era of business ownership.
Now, just over 50 years later, Kubes Steel is Canada’s largest steel bender. Equipped with induction bending equipment and one of the largest brake presses in the area, Kubes Steel manufactures rollercoasters, bridge components, and even the arm structures for Disney World’s Harmonious Spectacular at Epcot.
Because Kubes Steel serves a wide range of industries, it is largely insulated and protected from economic events or industry-wide downturns. Being adaptable, embracing new challenges, and anticipating market trends have been critical to the organization’s success from the very start, and they still serve it well today.
“With over 80 employees, Kubes Steel is so much more than ‘just a fabricator,’” Wyatt said. “It is an economic catalyst in Canada and helps support 80 households through long-lasting employment opportunities and reliable job growth.”