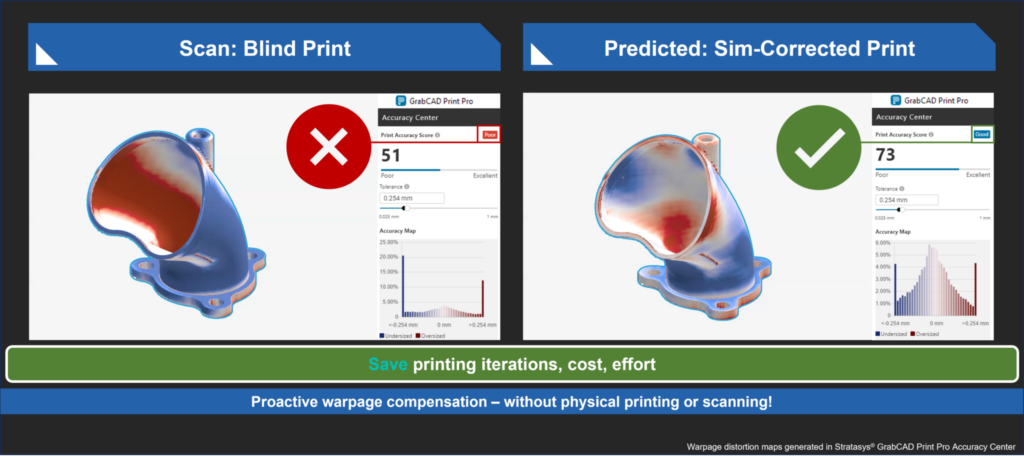
A comparison of blind print results to simulation-corrected print results. (Image courtesy America Makes/AlphaStar)
AlphaSTAR’s award-winning technology is said to accurately model, predict, and prevent common issues for polymer and metal applications before the start of production.
YOUNGSTOWN, Ohio—The challenges associated with building quality parts quickly and consistently remain a major industry hurdle and are limiting the widespread adoption of additive manufacturing (AM), according to a release from America Makes, a public-private partnership for additive manufacturing technology and education.
In response, practitioners are actively seeking new ways to overcome this technological gap to improve production and reduce costs. According to Luis Morales, corporate and strategic business development director at AlphaSTAR Technology Solutions, one viable solution is the company’s predictive digital twin simulation technology.
AlphaSTAR, an engineering software company based in Irvine, California, is leading the charge by providing innovative physics-based simulation technologies to address the industry’s needs.
“Simulation sciences have been around as long as manufacturing itself. People have always sought to predict the outcomes of their production processes,” Morales said in the release. “However, simulation technology has had to evolve to adapt to more advanced means of manufacturing, including many of the new modalities that AM has introduced. There’s been a confidence and technological gap, and those are areas that we can fill.”
AlphaSTAR has more than 35 years of manufacturing technology experience and is the developer of its GENOA 3DP, an award-winning Integrated Computational Materials Engineering (ICME) tool for additive manufacturing materials and processes. Its advanced technology is reported to accurately model, predict, and prevent common issues for polymer and metal applications before the start of production, enabling faster and more successful part production.
Without advanced simulation tools like AlphaSTAR’s Genoa3DP, component manufacturing and testing are highly iterative, time-consuming, and wasteful. Current methods to build accurate parts require expensive equipment, such as scanners and monitoring devices, to measure defects and anomalies. They also require numerous reprints to detect part failures, further complicating an already complex process.
The existing process lacks insight into the thermo-mechanical properties of the finished product until it is physically built, making it challenging to print accurately the first time. To solve these critical manufacturing challenges, AlphaSTAR believes the answer lies in intelligent, predictive software.
“We can virtually test and manufacture a part before it goes into production, assuring a manufacturer that the outcome of a print process is much closer to their end goal, offering clear advantages over the brute force, or hand-waving, approaches commonly employed to resolve printing issues,” noted Morales.
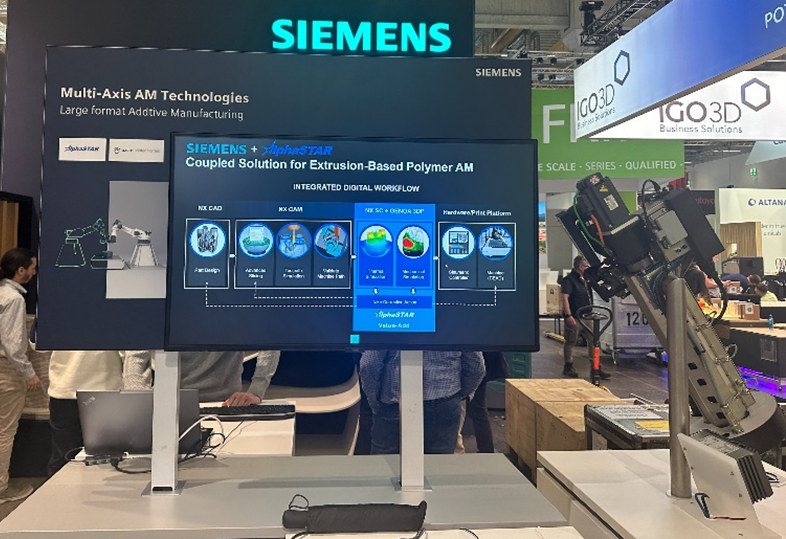
An LFAM use case on display at Formnext 2024. (Image courtesy America Makes/AlphaStar/Siemens)
Advancing simulation technology: beyond niche and into the mainstream
AlphaSTAR’s continued development of and growth in predictive digital twin technology has historically been strategically aligned with the U.S. Department of Defense’s (DoD) initiative to invest in advanced technologies that enhance U.S. industrial competitiveness. The company has verified and validated its technologies with various DoD-affiliated agencies—including the Defense Logistics Agency and the Missile Defense Agency—to support this effort. Recently, however, AlphaSTAR has prioritized projects focused on commercialization across applications.
Broadening its scope, AlphaSTAR has accelerated its commercialization efforts by focusing on delivering value to enterprise customers in verticals such as defense and aerospace, energy, consumer, automotive, and industrial. This means improving the ease of use, interoperability, scalability, and feature sets that make the solution more readily consumable by the end user.
For example, AlphaSTAR recently debuted a use-case study showcasing its polymer large-format AM (LFAM) simulation capabilities in fabricating 3D-printed houses. In partnership with a leading vendor in this market, AlphaSTAR’s technology simulated the construction of an entire 3D-printed housing structure, detected potential anomalies, and took corrective action. It accomplished all this before production even took place, ensuring the continued production of high-quality builds.
However, when it comes to deriving the benefits of AlphaSTAR’s simulation capabilities, it’s not a one-size-fits-all opportunity. AlphaSTAR’s solutions are customizable and adaptable for a variety of materials, use cases, and production settings. This is where partnering with a diverse set of ecosystem players comes into play and pays off.
Leading AM simulation through cooperative collaboration
As it stands, manufacturers looking to gain greater insight into qualifying and certifying their material and process are tasked with coalescing multiple providers, who offer a litany of tools that are often not designed to be complementary or connected. AlphaSTAR asserts that the road to resolving this issue and achieving customer satisfaction is paved with cooperative effort.
Designed with interoperability in mind, AlphaSTAR’s tools can provide a direct benefit to end-users who want to get the most out of their AM investments by integrating its simulation tools into their existing infrastructure.
AlphaSTAR is an ecosystem partner with the 3D printing machine manufacturer Stratasys through Stratasys’s GrabCAD Print Pro platform. It is also filling a key polymer simulation technology gap in the end-to-end AM platform of CAD/CAM engineering software giant Siemens. The fruits of these strategic relationships were on display during the Formnext conference in Frankfurt, Germany, where AlphaSTAR was featured in the Siemens booth as a technology partner.
“The technological advancements made through our collaborations with these industry leaders are a testament to how important it is to strike partnerships,” noted Morales. “Because when we can demonstrate a better end-user experience and productivity gains for our common customers by implementing our value-added simulation solutions, everyone wins.”
Alongside its strategic business partnerships, AlphaSTAR has collaborated with America Makes, the National Additive Manufacturing Innovation Institute, for several years, serving as a leading expert in advancing the ecosystem’s knowledge and promoting awareness of advanced AM technologies. Recently, the company’s CEO, Kay Matin, was appointed as an America Makes Ambassador, underscoring AlphaSTAR’s commitment to driving innovation and pushing additive manufacturing forward.