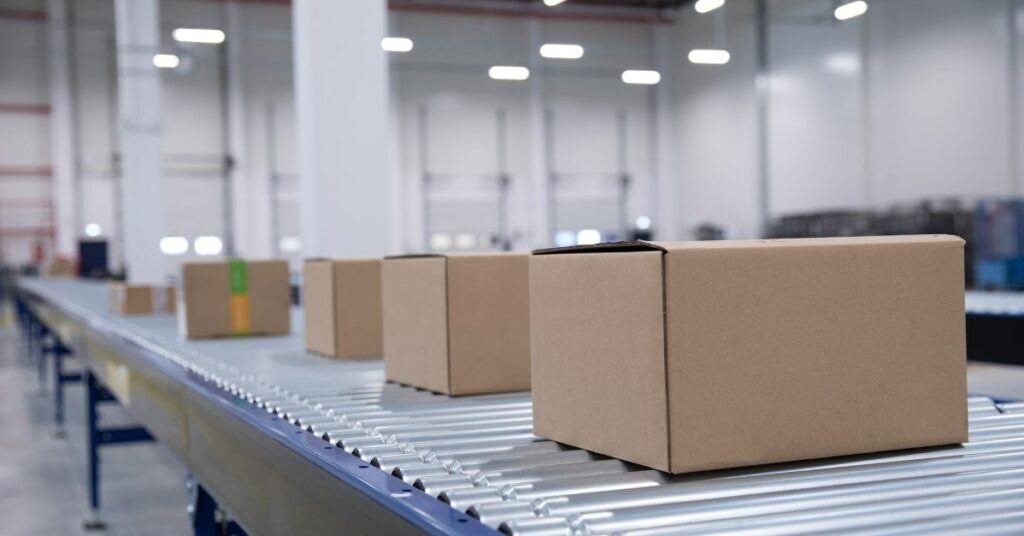
Ultimation forecasts an increase in automation as companies look to improve efficiency and accuracy of material movement and fulfillment processes. (Photo: PRNewswire/PRWeb)
Smart technologies are expected to help boost operational efficiency, according to a manufacturer of industrial automation equipment systems.
ROSEVILLE, Mich.—As they work to improve operational efficiency, manufacturers and distributors are increasingly incorporating smart technologies into the material handling operations of their production facilities and warehouses.
As a result, technologies such as robotics, automation, and artificial intelligence (AI) in material handling operations are expected to be among the top trends for manufacturers in 2025, according to a release from Ultimation Industries, a manufacturer of highly engineered automation and material handling equipment.
A division of Motion & Control Enterprises (MCE), Ultimation works to solve productivity challenges with special purpose machinery and industrial automation equipment systems. The company also provides direct-to-consumer products for a broad range of end-markets, including energy, automotive, logistics, and vertical farming.
“Companies of all sizes in the manufacturing, warehouse, and distribution sectors are realizing that they need new technologies and sustainable options to remain competitive in an increasingly demanding marketplace,” said Kali Wahrman, Ultimation’s general manager for e-commerce, in the release.
Based on interactions with its customers, Ultimation forecasts the following five material handling trends for the upcoming year.
Enhancing human labor capacity with automation and robotics
In the new year, companies are expected to continue to automate some material handling tasks to address the ongoing skilled labor shortage in the manufacturing, distribution, and warehouse sectors. Automated processes offer improved efficiency and accuracy of material movement and fulfillment processes. Robots, for example, are currently used to move material through a facility, retrieve products, or take items on or off a conveyor belt.
It’s also becoming more common for robots and employees to work side by side, with the robots handling tasks that are repetitive, involve heavy lifting, or are otherwise unsafe for humans.
Harnessing data for operational efficiencies
Companies are becoming more aware that the data produced by machines and equipment can help them resolve their biggest material handling challenges. Internet of things (IoT) technology brings together the data and information locked inside sensors, radio frequency identification (RFID) chips, and other sources and gives supply chain managers new insights into their operations.
For example, real-time collection of product and material data, such as condition, load capacity, temperature, and other metrics, can be used for better decision-making to improve process flows, minimize idle times, and reduce cost. “Smart” systems, such as barcoding technologies that integrate with existing enterprise resource planning (ERP) and inventory systems, are also being used to streamline processes and gain efficiencies.
Working smarter with machine learning and AI
Artificial Intelligence was all over the news in 2024, with a dizzying array of possibilities for supply chains. In 2025, companies with robust digitalization strategies are looking to AI and machine learning to further improve their productivity. Both AI and machine learning automate a variety of manual processes involving data and decision making.
For example, they can monitor equipment data to determine the optimal time to perform maintenance or study a facility’s energy use patterns to maximize efficiency. In the new year, material handling leaders are expected to prioritize technologies that increase fulfillment accuracy, streamline inventory management, monitor equipment performance, and optimize warehouse space, Ultimation said in the release.
Moving toward electrification and sustainability
Electrification isn’t just happening in the auto industry. It’s also a growing trend in material handling as companies look to convert older conveyor technology into more sustainable electronic options. For example, legacy conveyor systems that run constantly are being replaced with alternatives that only use electricity when they are actively moving cargo.
Another trend rooted in sustainability is lightweighting, which involves swapping out heavier materials for lighter alternatives that enhance system efficiency. Additive manufacturing, also known as 3D printing, can also play a role in sustainable operations. It can reduce waste and energy usage when compared to traditional manufacturing.
Maximizing facility footprints
In 2025, companies are expected to continue their efforts to optimize their facility footprints to improve process flow, operational efficiency, and flexibility. Conveyor systems with modular designs make planning simple if changes or expansions are required. Mix-and-match solutions across several different conveyor types, such as roller conveyors, belted conveyors, and key sorting elements, can easily be combined for a customized solution. Lifters and overhead conveyor systems are an affordable, effective solution that can be deployed to take advantage of otherwise unused vertical space, the company said.
Ultimation Industries offers products and services to help industrial companies improve the productivity and efficiency of their material handling operations. As a manufacturer of direct-to-consumer conveyor systems, Ultimation serves the automotive, food processing, vertical farming, heavy equipment, warehousing, fulfillment, and delivery industries. The company offers a line of proprietary automation systems and is reported to be the largest integrator of Jervis Webb Conveyor Systems.