Why U.S. OEMs are bringing production closer to home
As U.S. imports from low-cost Asian countries and regions decline, U.S. OEMs and product manufacturers continue to bring production operations and supply chains closer to home. But is the onshored manufacturing model—commonly known as “Made in USA”—built to last?
Recent trends in reshoring, foreign direct investment (FDI), and domestic investments in U.S. manufacturing are highlighting the growing momentum of onshored manufacturing (reshoring and new investments in domestic manufacturing operations and supply chains) and suggesting that it could continue well into the future.
Research released in November by global management consultancy Bain & Company revealed an acceleration in strategic reshoring moves by businesses worldwide—to shift operations and supply chains closer to their home markets. It also shines light on the emerging trend of “split-shoring,” where businesses balance a mix of offshore production with other key manufacturing activity close to home, the company said in a release announcing the results.
Bain’s operations survey gathered views from 166 CEOs and COOs. Ninety percent of the respondents manage businesses with revenues in excess of $1 billion—more than half at companies with revenues above $5 billion, and two-fifths at companies with more than $10 billion in revenues, the company said in the release.
The survey found that the percentage of CEOs and chief operating officers who reported their companies are planning to bring supply chains closer to market rose from 63 percent of those surveyed in 2022, to 81 percent in 2024—a sharp 18 percent increase. Meanwhile, only 36 percent reported further investment in offshoring. However, the findings also show that reshoring efforts have much further to run, as only 2 percent of companies reported having fully completed their plans.
What’s disrupting the previously well-established business incentives for low-cost offshore manufacturing?
Factors such as geopolitical turbulence, rising costs, and pressures for reduced carbon footprints are fueling the trend toward onshoring. By working to shorten their supply chains, companies are also helping to strengthen the resilience of American manufacturing.
“We believe the current acceleration of reshoring across key markets worldwide is a crucial trend that demands CEOs’ attention,” said Hernan Saenz, Bain & Company partner and global head of the firm’s Performance Improvement practice, in the November 2024 release. “The multiple disruptions companies have grappled with since the pandemic mean the question for company leaders is no longer whether to reinvent supply chains, but how to do that so their operations are made more cost-competitive, resilient, sustainable, and agile in responding to evolving markets and customer needs.”
Deglobalization, U.S. Inflation Reduction Act Are Fueling Trends
Bain’s analysis indicates that reshoring is also being reinforced by deglobalization trends. Apparent concerns over decoupling of economic blocs contributed to a rise of more than 25 percent in the proportion of companies seeking to reduce dependence on China. Survey results show that the proportion of companies reporting moves to shift operations out of China rose from 55 percent in 2022, to 69 percent in 2024.
In the United States, where 39 percent of respondent businesses are based, the findings also point to reshoring as having been further stimulated by the 2022 Inflation Reduction Act (IRA). The IRA offers U.S. companies subsidies and tax credits that incentivize reshoring and near-shoring to boost domestic manufacturing and job creation—particularly in sensitive markets, such as those for semiconductors, clean energy technologies (such as solar panels and wind turbines), and electric vehicle supply chains.
Moves toward reshoring of semiconductor manufacturing have also been intensified by the U.S. CHIPS Act, which put in place tax incentives and $52 billion in funding to stimulate U.S. domestic production of chips—as well as surging AI-driven demand for graphics processing units (GPUs).
Bain’s recent Global Technology Report forecasts that demand for key GPU components could increase by 30 percent or more by 2026, potentially triggering an AI-induced chip shortage.
“The powerful forces driving the patterns of re-shoring, near-shoring, and split-shoring that our findings show will persist and confront company leaders with the challenge and opportunity of transforming their supply chains for reshaped global markets,” said Adam Borchert, partner in Bain & Company’s Performance Improvement practice and global lead of its Supply Chain practice, in the release. “We are helping clients to navigate these shifts and build supply chains that meet market needs, are resilient and future-proofed, while strengthening management capabilities to adapt to further change in an uncertain world of constant turbulence.”
Kearney’s 2024 Reshoring Index Identifies ‘Made in America, For America’ as a Lasting Trend
The report found that U.S. consumers are starting to ‘buy American,’ with rates increasing 5 percent between 2022 and 2023.
CHICAGO—Last April, the global management consultancy Kearney released its 11th annual Reshoring Index, a unique barometer tracking the extent to which America is reshoring manufacturing after decades of offshoring.
The 2024 report, Made in America: Here to Stay? focuses primarily on import and export flows between the United States and 14 Asian low-cost countries and regions (LCCRs), including mainland China, as well as import trends with Canada and Mexico.
The 2024 Kearney Reshoring Index finds a U.S. market increasingly importing goods made closer to home and less on goods from low-cost countries and regions, continuing trends that have been set in motion over the past few years, Kearney said in a release.
“While it sounds like an election year bumper sticker, the phrase ‘Made in America, for America’ could describe the foreseeable future of industrial manufacturing in the Western hemisphere,” noted Patrick Van den Bossche, a Kearney partner and lead author of the annual Reshoring Index report.
“However, that doesn’t mean mainland China and other producer nations are sitting idly by as more and more nearshored goods flow into the U.S. market. Our research shows an emerging correlation between the uptick in U.S. imports from Asian LCCRs other than mainland China, and the rise in imports these countries see from mainland China. Mainland China is now running trade surpluses with Vietnam, India, and Thailand, which in turn are running widening surpluses with the U.S.”
The Index shows that nearshored and reshored industrial production efforts taking place in the U.S., Canada, and Mexico continue to take market share away from Asian manufacturers, including mainland China.
According to Kearney’s Reshoring Index, U.S. imports from 14 Asian low-cost countries and regions declined from $1,022 billion in 2022 to $878 billion in 2023, while domestic manufacturing gross output (MGO) stayed essentially flat.
The majority of the drop in Asian LCCR imports was caused by a whopping 20 percent reduction in Chinese imports. However, for the first time since the inaugural 2013 Reshoring Index, some Asian LCCRs other than mainland China—including Vietnam and Malaysia—also saw a dip in imports.
The report found that imports from Canada have steadily increased since the pandemic, keeping pace with Asian LCCR imports. South-of-the-border trends detailed in Kearney’s 2023 report also continued and expanded in the new Index. Last year, for the first time since 2013, Mexico surpassed mainland China as the largest exporter to the United States. Mexican manufactured goods imported into the US grew by 32 percent, from $320 billion to $422 billion, since the pre-COVID period.
“U.S. investments in reshoring remain strong, but despite receiving considerable support from both the private and public sectors, domestic manufacturing still faces considerable hurdles, including a lack of skilled workers, labor costs, and infrastructure challenges,” noted Mexico-based Omar Troncoso, a partner in Kearney’s consumer and retail practice and co-author of the Index. “Our research nonetheless shows that the vast majority of leaders looking to bring their manufacturing operations closer to the domestic market are considering the U.S.
“This year’s peaking Reshoring Index shows strong continued interest from CEOs in reshoring and nearshoring activities, underscoring what now appears to be a decisive shift in strategic business operations toward manufacturing products closer to the U.S. domestic market. In addition, mainland China’s growing presence in Mexico is testimony to mainland China’s intent to remain a fixture in the U.S. imports picture.”
Patrick Van den Bossche added, “That said, U.S. companies and consumers are starting to truly ‘buy American,’ as shown by our U.S. self-sufficiency index (SSI), which tracks how what’s made in the United States for the U.S. market compares against what’s imported and stays in the U.S. market.” The SSI gradually declined from 2013 to 2020 but started flipping modestly in 2021 and increased by 5 percent between 2022 and 2023, the release stated.
“The movement of making goods for the U.S. market closer to that market is now well established, and strong continued interest from CEOs and their stakeholders in reshoring activities underscores what now appears to be a decisive shift in strategic business operations toward repatriating manufacturing to the United States,” the release stated. “To echo the popular song, ‘Born in the USA’ seems to be taking hold.”
Launched in 2013, the Kearney Reshoring Index is a unique barometer for tracking the extent to which America is reshoring manufacturing back from Asian countries that have benefitted for decades from US companies offshoring their manufacturing operations. The Reshoring Index is determined by dividing the import of manufactured goods from the 14 Asian LCCRs by the US domestic gross manufacturing output to calculate a manufacturing import ratio (MIR). The Reshoring Index reflects the year-on-year change in the MIR.
Geopolitical Risk, Industrial Policy Are Driving Reshoring and FDI, Reshoring Initiative Says
SARASOTA, Fla.—Reshoring and foreign direct investment (FDI) job announcements in 2023 continued to climb, adding 287,000 jobs, the second-highest year on record, according to the latest annual report of the Reshoring Initiative.
Released last July, the report found that electric vehicle (EV) batteries, semiconductor chips, and solar energy [components and equipment]—all essential goods supported by U.S. industrial policies—account for 39 percent of the job announcements.
“Recent trends in reshoring and foreign direct investment (FDI) are demonstrating significant strength and longevity,” the Reshoring Initiative stated in a release summarizing the report. “Geopolitical risk and climate change have aligned corporate strategy and U.S. industrial policy, leading to a notable increase in U.S. manufacturing investments. These trends are largely driven by efforts to shorten supply chains and bolster domestic resilience.”
The Reshoring Initiative cautioned that future progress in reshoring and FDI will have to depend heavily on policies that enhance long-term U.S. manufacturing cost-competitiveness, rather than relying solely on subsidies, which had already begun to wane when the report was released last July.
According to the Reshoring Initiative, geopolitical risk remains the top driving force in reshoring and FDI trends.
In Europe, the ongoing conflict in Ukraine was expected to continue redirecting FDI from Europe to the U.S., primarily due to concerns over natural gas and electricity availability and pricing. European-origin announced jobs rose from 13 percent of the total in 2021 and 2022 to 34 percent in 2023, with a projected increase to 37 percent in 2024, the release stated.
The October 7, 2023, attack on Israel by Hamas is expected to continue influencing FDI trends moving forward, although it was too late to impact 2023 data. Nearly all cases from Israel are FDI—its companies have long understood the value of having assets in the United States, according to the release.
Rising tension between the U.S. and China over Taiwan is a key factor in industrial policy, leading corporate strategists to increasingly consider reshoring as a critical component of their long-term planning.
According to the Reshoring Initiative, 20 percent of the new manufacturing jobs created by reshoring, FDI, or nearshoring from 2010 to the present were a result of reshoring; 72 percent were from FDI, and 8 percent were created by nearshoring. Jobs per year peaked in 2022 at 12,500, primarily due to Taiwan Semiconductor, and dropped to 650 in 2023.
The success or failure of recruiting and training millions of workers is expected to determine the outcome of the current reindustrialization momentum, in either direction. Trends are described as “moderately positive,” as manufacturing apprenticeships were up 83 percent in the last 10 years.
“About 49 percent of cases in 2023 mentioned skilled workforce availability as a reason they reshored, essentially tied for second with proximity to customers,” the Reshoring Initiative stated.
In summary, the trends in reshoring and FDI are said to “indicate a robust movement towards strengthening U.S. manufacturing amid global uncertainties.”
“Strategic policies and geopolitical developments will continue to shape the landscape, driving investments that enhance supply chain resilience and economic security,” according to the Reshoring Initiative.
The Reshoring Initiative’s annual report includes data on U.S. reshoring and FDI by companies that have shifted production or sourcing from offshore to the United States.
“We publish this data to show companies that their peers are successfully reshoring and that they should reevaluate their sourcing and siting decisions,” said Harry Moser, founder and president of the Reshoring Initiative. “With 5 million manufacturing jobs still offshore, as measured by our $1.2 trillion per year goods trade deficit, there is potential for much more growth. We also call on the administration and Congress to enact policy changes to make the United States competitive again.”
For the First Time, Solar Trackers With 100 Percent Domestic Content Are Delivered to U.S. Market
Through its local manufacturing and domestic content initiatives, Nextracker is working to set a new standard for American manufacturing, job creation, and supply chain resilience.
FREMONT, Calif.—The solar tracker technology developer Nextracker recently achieved a significant milestone in supply chain localization, as the company announced in December that it had shipped and delivered—in the United States—the industry’s first U.S.-manufactured solar trackers that are expected to achieve “100 percent domestic content value for solar trackers under the Inflation Reduction Act (IRA).”
Nextracker stated in a release that SB Energy’s Pelican’s Jaw project, currently under construction by SOLV Energy, is the first project to receive the domestic content trackers. The supply chain milestone is said to reaffirm Nextracker’s industry leadership and commitment to American manufacturing and jobs, while providing operational excellence for customers and partners.
The company began investing in local manufacturing infrastructure in 2021 to establish a secure supply chain, following disruptions during the global pandemic. Together with its manufacturing partners, Nextracker has now expanded or opened more than 25 U.S. factories with more than 30 GW of annual capacity, the release stated.
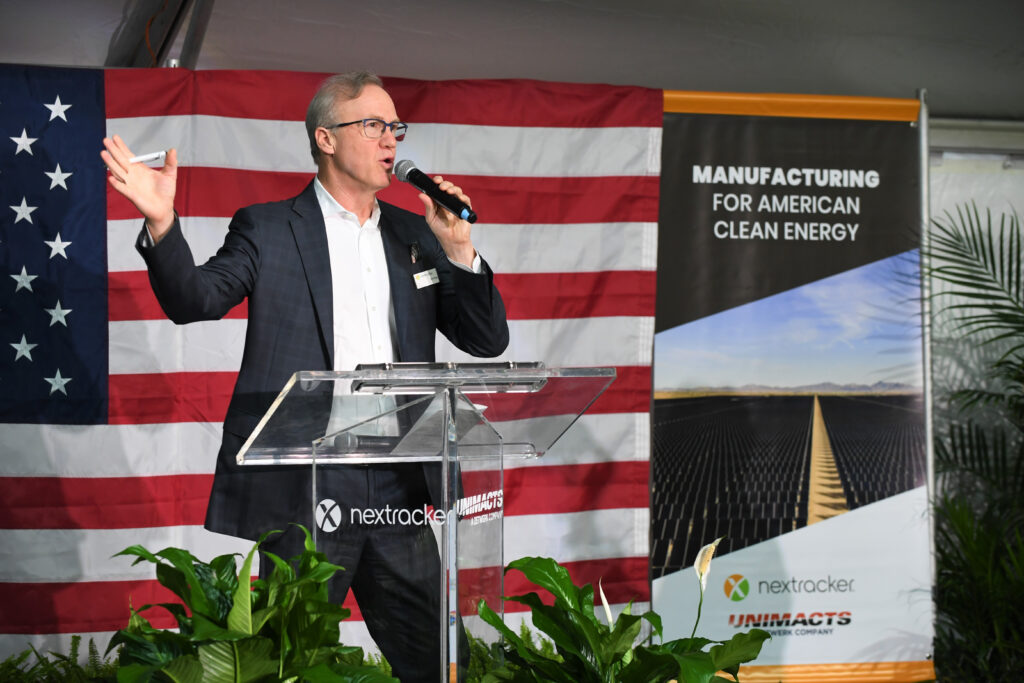
Nextracker Founder and CEO, Dan Shugar speaking at steel manufacturing plant opening. Critical steel components used in Nextracker’s solar trackers are fabricated at this Las Vegas Unimacts facility. (Photo: Nextracker)
Nextracker’s robust local supply chain is reported to significantly reduce lead times with top quality products, providing customers with superior performance, shipping logistics, and flexibility throughout construction and the entire project lifecycle.
“Delivering the industry’s first trackers with 100 percent domestic content value is a huge milestone for our customers, our supply partners, and Nextracker,” said Dan Shugar, Nextracker founder and CEO, in the release. “It demonstrates our ability to ramp and scale operations that directly benefit our customers—and sets a new standard for local supply chain resilience and operational excellence.
“By systematically focusing our manufacturing partnerships close to our customer project sites, we secure the supply chain and provide superior on-time delivery and cost savings for project development and construction,” he continued. “We also significantly de-carbonize our products by incorporating clean steel manufactured in the United States.”
Abhijeet Sathe, Co-CEO, SB Energy, added that SB Energy is “proud to drive growth of domestic manufacturing for renewable energy” through its projects.
“Our Pelican’s Jaw project will be the first to utilize Nextracker’s 100 percent U.S. domestic content solar trackers. We applaud Nextracker for their leadership in creating a robust U.S. supply chain to support our projects with greater supply security and create high paying, domestic manufacturing jobs.”
Solar power has become the leading source of new power generation, creating well-paid jobs both in the United States and globally, according to the International Energy Agency. The American Clean Power Association reports that, as of 2023, the U.S. solar industry supports 279,000 jobs, driving significant economic growth in states like Arizona, California, Florida, Pennsylvania, Tennessee, and Texas.
“I attended Nextracker’s manufacturing plant dedications in Texas, Pittsburgh and Las Vegas, where U.S. workers are building high quality solar products that will help power renewable energy projects across the country,” said George Hershman, CEO of SOLV Energy, in the release. “Nextracker will supply the first 100 percent U.S. domestic content trackers to Pelican’s Jaw, a 570 MW solar and 954 MWh storage project that SOLV is building and operating for SB Energy. Their leadership in domestic manufacturing supports shorter lead time, on-time delivery, and a smoother installation process for our project teams and client-partners.”
Nextracker’s calculation of the domestic content percentage was based on May 2024 U.S. Department of Treasury guidance, with simplified safe harbor domestic content calculation tables, according to a company release.