The following article was contributed by All Metals Fabricating, Inc.
ALLEN, Texas—The traditional industry of custom sheet metal fabrication was a sum of straightforward processes. Metal fabrication meant welding, cutting, machining, and assembly.
The industry has evolved by magnitudes since da Vinci’s first sketch of a modern sheet metal technique in 1485. The industry also represents the foundation of aerospace, construction, energy, and the automotive industry.
In response, metal shops have adapted by diversifying their portfolio. In this article, you will learn what metal fabrication is and how the process works.
What is metal fabrication?
You use many products, daily, that form parts of the metal fabrication sector. Mailboxes, roof gutters, phone casings, and air-conditioning ducts/furnace flues are all examples.
Metal fabrication takes sheet metal from its recycled or manufactured state into new products. Most metal fabricators work with sheet metal. Sheet metal is industry-standard sheets that are cut, folded, and shaped into end products. Sheet metal is used for both mass production and custom products.
How does metal fabrication work?
Metal fabrication uses complex machinery and manufacturing processes to produce high-quality products. Sheet metal typically arrives from a wholesaler or metal mill. Sheet metal is cut, folded, formed, bent, engraved, and more. Standard tools that a metal fabricator will work with include lasers, punch presses, and press brakes.
High-quality products require clean cuts and no discoloration, and so they will often be manufactured using a laser cutter. Intricate patterns are also better performed with a laser cutter. Laser cutting can handle a wide variety of metals, including carbon steel and titanium.
Metal fabrication involves many different types of metals. More than 3,500 different grades of steel alone exist, over 75 percent of which have been developed in the last 20 years. Metal is highly adaptable. A wooden framed house must be crafted from undamaged recycled pieces and fresh timber. Yet, four recycled steel cars can be fabricated into a 2,000-square-foot house.
The metal fabrication process
Product engineers start the process by sending out plans and sketches to different fabricators to get quotes. The fabricators come up with a cost estimation and timeline based on their experience and the potential project.
From these quotes, product engineers select one fabricator for that particular end product. Some end products can have several different fabricators involved in different elements. The fabricator then orders materials for the project—typically sheet metal, bars, rods, and tubes.
Once the parts arrive, the fabricators begin to work. For custom sheet metal fabrication, the fabricators may play a role in the design process as unique products need specific techniques to achieve the right result. Highly skilled fabricating shops are usually able to produce any product after deducing the best manufacturing process for it.
The final step of the manufacturing process involves assembly and finishing. These processes prepare the product for use, whether with joining techniques or coatings. Methods like graining with a belt sander or putting a vibratory sanded finish are two raw metal finish options. Other common finishes include powder coated or various plating specifications.
The processes involved
The process of metal fabrication involves special machines, some of which are unique to metal materials. In total, there are many processes involved in metal fabrication. Here are a few examples of the processes involved in sheet metal fabrication:
- Cutting – Shear, CNC punch presses, lasers, waterjet, plasma
- Bending – Press brakes, folding machines, panel benders
- Welding – Mig, Tig, robotic, laser
- Hardware insertion – Haeger Presses
- Grinding and Graining – cleaning up welds, belt sanding to achieve a nice, grained finish
The benefits of metal fabrication
Metal fabrication is a highly skilled and potentially complex manufacturing process. Fabrication is expensive, so it is often reserved for high-quality products.
Below is a shortlist of essential reasons why metal fabrication could be the right choice for your manufacturing project.
The final appearance of your product is the key to profit. Many high-quality manufacturers, such as tech companies, have opted for a metal design. Metal gives smartphones and computers durability and a modern, sleek look.
The durability of metal products is naturally superior to plastic. Not to mention that metal can withstand higher temperatures. If the manufacturer has taken into account expansion under heat, the heat will usually not damage the product.
Especially in high volume manufacturing, metal is far more cost-efficient than other processes. Process replication can reduce the manufacturing cost per unit. The method of sheet metal fabrication is also more versatile, allowing for a wider variety of approaches. Other materials cannot withstand many processes that can be carried out on metal.
Custom sheet metal fabrication
Metal fabrication is a complex manufacturing process, but it is highly versatile and adaptable. With the right fabricator, the process can result in a high-quality, distinguished product. Ultimately, those products can be cheaper to manufacture. Sheet metal fabrication gives you more control over the end product.
Custom sheet metal fabrication is highly flexible. Still, some processes will not work with certain materials or will be limited by product design. Therefore, it is crucial to contact a professional metal fabricator for advice and guidance during the design process to confirm your plans.
About All Metals Fabricating
All Metals Fabricating (https://www.ametals.com/) is an Allen, Texas-based contract manufacturer that specializes in custom sheet metal fabricating, precision machining, electromechanical assembly, and powder coating. The company’s services range from product design to turnkey assembly and delivery of the end product.
An earlier version of the article appeared as a blog post on All Metal Fabricating’s website.
Source:
https://www.ametals.com/post/everything-you-should-know-about-custom-sheet-metal-fabrication
Sheet Metal Fabrication Services Market Predicted to Grow by $3.3 Billion from 2024 to 2028
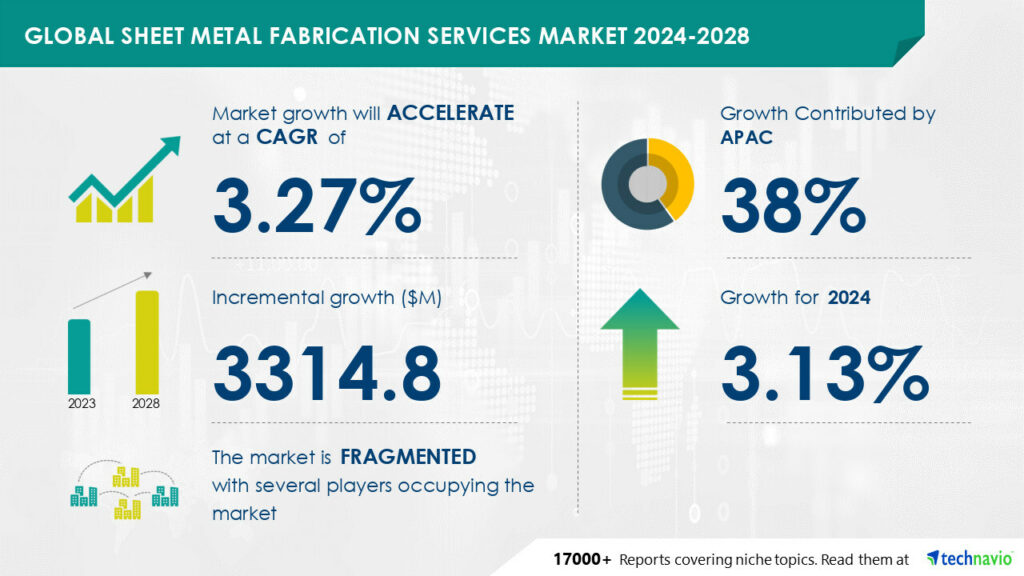
In its 2024 market research report, the technology research and advisory company Technavio reveals some of the key trends fueling an anticipated $3.3 billion growth of the global sheet metal fabrication services market through 2028. (Infographic: Technavio)
Increasing demand for fabricated metal parts in major end-user industries is expected to boost growth of the global market, according to Technavio.
NEW YORK— Sheet metal fabrication, focused on creating metal products from flat metal sheets, is a thriving industry. Rising demand for fabricated metal parts in major end-user industries is driving growth of the global sheet metal fabrication services market, according to global technology research and advisory company Technavio.
The company said in a July 2024 release that it estimates the market will grow by USD 3.31 billion from 2024 to 2028, registering a compound annual growth rate (CAGR) of 3.27 percent during the forecast period.
Sheet metal fabrication services involve the creation of metal products from flat metal sheets using the long-established processes of cutting, punching, stamping, forming, bending, welding, and finishing. These services, provided by contract manufacturers, are well known for creating panels, brackets, enclosures, and components made from metals like steel, aluminum, silver, foil, and plate. Manufacturers in the electrical and electronics, industrial machinery, HVAC, automotive, and aerospace industries are among the major end-users of the fabricated metal parts.
Technavio noted significant demand from the automotive industry for sheet metal fabrication services, due to its extensive use of fabricated metal parts in various vehicle components.
Such parts include bus bars, terminals, electrical contacts, brackets, lead frames, shields, clips, and press-fit pins. Among the applications for these parts are fuel delivery systems, chassis, batteries, motors, lights, engines, seating, alternators, steering wheels, security systems, brake systems, and fuel systems, the company said.
Significant markets for sheet metal fabrication services also include the construction and infrastructure sectors, which rely on the services for metal reinforcements in skyscrapers, railway bridges, residential units, and industrial shades. “Ductwork, rain gutters, and other applications further expand the market,” the release stated. Another big market is the defense sector, which continues to invest in sheet metal fabrication for defense equipment, satellites, and rockets.
Key market trends fueling growth
One of the trends reported to be spurring the growth of the sheet metal fabrication services market is the adoption of 3D printing technology, also known as additive manufacturing. The innovative technology constructs 3D objects using digital files and builds the product in thin layers.
Traditional manufacturing techniques are subtractive in nature, leaving high amounts of wasted material in their wake and adding costs for reclaiming scrap. However, 3D printing optimizes material usage and reduces raw material and capital costs. The process is also known to enable production of complex geometries that are challenging to manufacture through traditional methods.
In the context of sheet metal fabrication, 3D printing is reported to be particularly beneficial for creating dies used in machine tools for punching processes. Dies, such as V-shaped, U-shaped, and 90-degree angle production, are expensive and have long lead times, delaying the metal processing process. But with the advent of 3D printers, dies and tools can be produced quickly and cost-effectively using fiber-reinforced polymer, the release stated.
Despite ongoing growth in the market, a shortage of skilled workers poses a significant challenge to the sheet metal fabrication services sector. This is particularly true in welding. Technavio described the shortage of welders as a pressing issue that is currently affecting the U.S., India, and China acutely. The American Welding Society predicted a deficit of 400,000 welders in the United States alone by 2024.
“The manufacturing sector’s lack of qualified labor results in increased labor costs due to overtime and longer production cycles, leading to inferior quality products and extended lead times, negatively impacting fabricators’ revenue,” the release said.
Companies in the industry today are embracing innovation by adopting capabilities such as building information modeling (BIM), industrial automation, and digitization through technologies like artificial intelligence, on-demand manufacturing, and robotics, including collaborative robots.
“Emerging technologies like plasma cutting, 3D printing, robotics, machine learning, and 3D bending technology are transforming the industry,” the release stated.
At the same time, the market continues to face challenges arising from intense competition and the need to maintain sustainable practices and operational efficiency. While sustainable practices, including the use of environmentally benign materials and energy-efficient manufacturing processes, are becoming increasingly important, capabilities in building information modeling and on-demand manufacturing are “transforming the industry by enabling faster and more accurate production,” the release said.
Steel Tube Institute To Focus its 2025 Priorities on Industry Trends
Talent, tariffs, and commercial building transitions will guide the organization’s efforts
CHICAGO—The Steel Tube Institute (STI), an organization that brings together key producers in the steel industry to advance the use of steel tubing, recently identified three primary priorities for 2025 that reflect anticipated changes to the manufacturing and steel industries. According to a release from the Steel Tube Institute, the priorities— skilled trade jobs, tariffs, and commercial building adaptations—coincide with the change in the U.S. presidential administration.
Steel Tube Institute leadership identified these priorities as significant to the future of the steel and construction industries during its Annual Fall Meeting. The organization said it plans to focus its efforts on “helping to ensure appropriate attention is given to future-proofing multi-use buildings with steel electrical conduit, training future skilled trade professionals, and incentivizing domestic steel conduit production.”
Future-proofing commercial buildings
Commercial real estate is expected to rebound in 2025 as global economic growth and lower inflation bring stability to the market, a recent Deloitte study found, giving new life to buildings that have remained vacant in the years since the pandemic.
The STI anticipates that changes to the way older commercial buildings—especially high-rises—are used will necessitate changes to how those buildings are wired. These changes, coupled with growing pressure to demonstrate sustainability, are said to make a strong case for the use of steel conduit in electrical raceways.
“There is a shift in the way multi-use buildings are being used,” said Steel Tube Institute Executive Director Dale Crawford, in the release. “Companies who are returning to the office after working remotely are looking for buildings that meet their customers’ demand for efficiency and sustainability.”
For example, using steel conduit raceways in the construction of battery bank floors within multi-use buildings helps to ensure that floors can be efficiently powered. This ensures a reliable energy source for companies transitioning to this new trend, according to STI.
A key focus for STI will also be educating engineers on the appropriate use of stainless-steel conduit, the preferred system for protecting electrical wiring in corrosive environments or in dry, damp, or wet locations. Steel Tube Institute’s recently-launched stainless steel subcommittee will lead the organization’s efforts to promote the appropriate applications for stainless steel conduit.
North American reshoring and its impact on skilled trade jobs
A renewed interest in domestic manufacturing is expected to boost local economies and create hundreds of thousands of high-paying skilled labor jobs, which are becoming increasingly appealing to young professionals. Steel Tube Institute said it will continue to promote the benefits of these jobs to attract top talent in manufacturing and electrification.
“The push to trade gasoline-powered cars, natural gas heating, and gas stoves for their electric counterparts will drive demand for skilled electricians,” said Crawford. “This is why the Steel Tube Institute and its member companies are advocating for a new generation of skilled tradespeople to support electrification across industries.”
The Steel Tube Institute and its member companies are educating the public on their investments in automation and safety technology. A career in skilled labor is once again attractive for its good pay and strong benefits but also as a safe work environment. The Institute, along with its member companies, are also promoting the low barrier to entry for the field; apprentices are paid as they make their way through an apprenticeship and education.
“Manufacturing can truly be more than a job, but a lifetime career with the flexibility to find the type of work that fits one’s personality and lifestyle,” said Crawford. “We hope the rising generation sees the choices that are available to them outside of college and the gig economy.”
Tariff enforcement
Promoting domestic steel production has long been a priority for STI, and that remains a priority under the new U.S. presidential administration. The Steel Tube Institute, along with its Canadian counterparts, supports tariffs on imports for items that can be produced domestically. The organization and its member companies are prioritizing their support for more funding for commercial enforcement for customs and border protection.
As innovation continues to add complexity to products, customs and border protection agents must be equipped with the resources to properly implement tariffs.
“STI has broadened its bylaws to join forces with its Canadian counterparts to ensure continued quality and clean practices are appropriately enforced as steel products are imported from foreign manufacturers,” the release stated.
The Steel Tube Institute remains committed to advancing the use of steel tubing and supporting the evolving needs of the market. Through collaboration with key producers in the steel industry, the organization said it plans to “continue to promote the benefits of steel conduit raceways for future-proofing commercial construction, support the growth of the skilled-labor force, and advocate for stricter tariff enforcement on imported products.”
The Steel Tube Institute began in 1930, when a group of manufacturers joined forces to promote and market steel tubing. “Their goal was to mount a cooperative effort to improve manufacturing techniques and inform customers about their products’ utility, versatility, and competitive advantages,” STI said in the release. “This, along with providing a forum for the discussion of issues impacting the industry, remains the focus of Steel Tube Institute’s efforts.”