The articles below are edited versions of releases about notable activities and advancements in the welding industry.
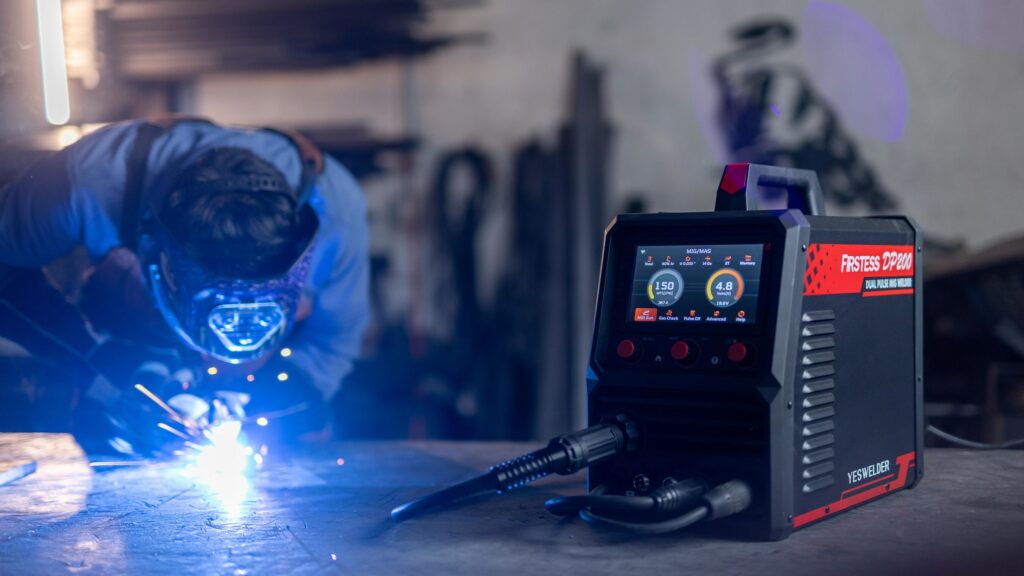
The Firstess DP200 features a multi-functional pulse welder system that offers various welding modes and flexibility, enhancing welding efficiency and adaptability. It also provides an adaptive compensation feature that is reported to dynamically adjust parameters to suit varying conditions, significantly reducing defects and enhancing the strength and reliability of the welds. (Photo: YesWelder/PRNewswire)
New Welding Machine Reported to Combine Industrial-Grade Precision with User-Friendly Design
NEW YORK—A multi-functional welder recently introduced by YesWelder is said to reflect the company’s vision to make welding accessible to everyone by providing high-quality products at affordable prices.
The YesWelder Firstess DP200, recently launched on Kickstarter, is described as a cutting-edge welding machine that combines industrial-grade precision with powerful performance and user-friendly design. This multi-process welding machine is designed to be accessible for seasoned professionals and beginners, and it is said to significantly lower the barriers to entry for welding.
“Thanks to its intuitive design and user-friendly features, even those with no prior experience can get started with ease,” the company stated in a release.
The Firstess DP200 welder is equipped with the patent-pending YesWelder PulseFlex™ System and patent-pending YesWelder AdaptivePulse™ technologies. Its user interface (UI) design, YesWelder IntuiWeld™, has already secured copyright registration, the company said.
The YesWelder PulseFlex™ System is reported to be a multi-functional pulse welder system that offers various welding modes and flexibility, enhancing welding efficiency and adaptability. By optimizing the pulse welding process, the system is said to ensure high-quality welds, reduce spatter, and enhance overall performance.
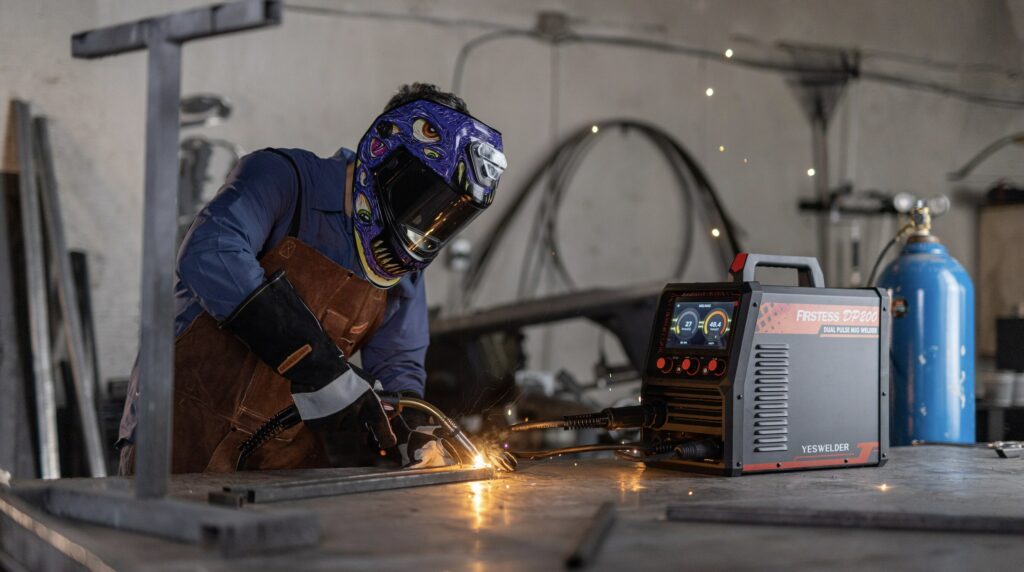
As it developed the DP200 from initial concept to final testing, YesWelder relied on real-world feedback from welders. (Photo: YesWelder/PRNewswire)
YesWelder AdaptivePulse™ is described as an innovative technology that provides precise control over the welding waveform, maintaining stability and consistency throughout the welding process. The adaptive compensation feature dynamically adjusts parameters to suit varying conditions, significantly reducing defects and enhancing the strength and reliability of the welds, the company stated.
The YesWelder IntuiWeld UI features a 7-inch display screen with dual-color options (black and white) to suit different scenarios. Its large display is easy to read, simplifying the adjustment of settings and the monitoring of welding data, the company said.
Community-driven development
According to YesWelder, the Firstess DP200 is more than just a welding machine—it’s a testament to the company’s commitment to its community. As it developed the DP200 from initial concept to final testing, the company relied on real-world feedback from welders. YesWelder’s focus on user input is said to ensure that the DP200 “not only meets expectations but exceeds them, offering a solution that feels tailor-made for welders. “
“This collaborative approach ensured that the machine addresses the actual needs of users,” the company said in the release. “Many of its thoughtful, user-friendly features—such as software upgradability, the ability to store up to 50 custom parameter sets with detailed notes (MIG/MAG), and comprehensive accessory options—are direct responses to suggestions from the welding community.”
The DP200 goes beyond being just a tool, according to YesWelder. It’s part of the company’s vision to open up the world of welding to more people, making the craft accessible and enjoyable for everyone.
“At YesWelder, we believe welding is more than a skill—it’s a way to create, to build, and to connect,” the company said in the release. “By breaking down barriers, we’re inviting more people to experience the joy and satisfaction that welding brings. Whether you’re just getting started or ready to level up, the Firstess DP200 is here to help you take that next step.”
Defense Contract To Support Demonstration of Automated Laser Welding Capabilities
The contract, valued at up to $44 million, will support development of Astra’s tactical launch system.
ALAMEDA, Calif.—Astra, a provider of launch services and spacecraft engines, was recently awarded a contract with a ceiling of up to $44 million by the U.S. Department of Defense’s Defense Innovation Unit (DIU). The contract supports Astra’s advancing and scaling the production capabilities of its unique tactically responsive launch system, the company said in a release.
Specifically, the contract award facilitates the continued development of Astra’s Launch System 2, including the demonstration of automated laser welding capabilities in the production of Rocket 4, advanced concepts of Launch System 2’s ground infrastructure, and the industrialization of Astra’s production facilities. Astra is currently working to achieve the prototype objective of launching Rocket 4 to orbit or suborbit.
“This is a major vote of confidence in Astra and the continued development of Rocket 4 and our next gen launch system,” said Astra Founder and CTO Adam London, Ph.D., in the release. “We are honored to partner with the DIU as we bring Rocket 4 to market with a renewed focus on reliability and scale.”
According to Astra, Launch System 2 is one of the lowest cost-per-launch dedicated orbital launch systems and is highly optimized for small constellation deployment, tactically responsive space (TacRS), point-to-point delivery, and national security and defense applications.
Astra intends to design and manufacture all of its rockets at its campus in Alameda, California, in its 250,000-square-foot manufacturing and testing facilities. These co-located, state-of-the art production and testing facilities have allowed Astra to rapidly iterate, reduce dependencies on third-party suppliers, and deliver for customers, the company said.
“This award is a testament not only to our team’s perseverance this past year, but also a validation of our vision for tactically responsive space,” said Chris Kemp, founder and CEO of Astra, in the release. “We’re proud to have so many partners who understand and support the importance of point-to-point space delivery for national security and defense applications.”
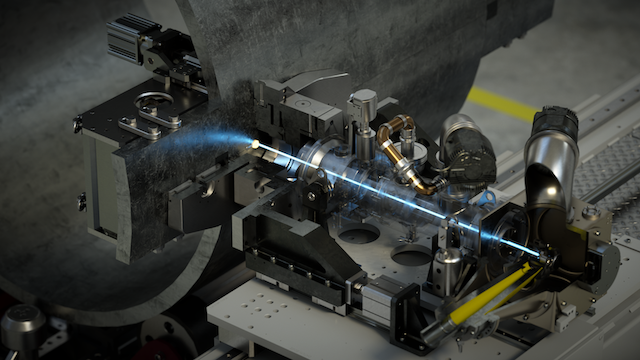
The Ebflow electron beam welding technology eliminates the need for a vacuum chamber through a local, coarse vacuum, which is established and maintained only where it is needed. (Photo courtesy Cambridge Vacuum Engineering)
Electron Beam Welding Technology Reported to Drastically Reduce Production Time of Small Nuclear Reactors
CAMBRIDGE, U.K. and AGAWAM, Mass.—An advanced electron beam (EB) welding technology developed by Cambridge Vacuum Engineering (CVE) is reported to have the potential to transform the speed at which small nuclear power stations can be built, according to a release from CVE.
In a trial conducted by Sheffield Forgemasters, Cambridge Vacuum Engineering’s Ebflow technology was deployed to cut the amount of time needed to weld a small modular reactor (SMR) pressure vessel demonstrator. The technology reportedly reduced the amount of time needed from more than a year to less than 24 hours, signaling a capability that could help reshape the future of nuclear reactor production worldwide, the release stated.
As part of a Government-funded project, Sheffield Forgemasters incorporated Ebflow, operating under local vacuum, into a bespoke, large-scale EB facility at its Brightside Lane site to complete four thick, nuclear grade welds on vessels with a diameter of three meters and a wall thickness of 200mm. As well as reducing welding time by a reported 99 percent, Ebflow delivered the superior quality and precision of welds needed to ensure SMRs operate safely. In doing so, the technology is said to have set “a new standard for weld-joining thick-walled components,” CVE stated in the release.
Ebflow is described as a highly advanced fusion welding process with applications across a wide range of industries, from oil and gas to nuclear power generation to ship building and more. The technology uses a focused beam of high-velocity electrons to join metal components together. The main difference from traditional welding methods is that no third-party material is introduced to facilitate joining. The technique is reported to enable unparalleled levels of accuracy and efficiency, making it suitable for the intricate welding requirements of primary components used in mission-critical energy applications—including mini nuclear reactors.
“Our partnership with Sheffield Forgemasters demonstrates the power of Ebflow and proves—beyond doubt—the benefits it can deliver when it comes to driving sustainable advancements in the energy sector,” said CVE Managing Director Bob Nicolson, in the release. “We all know the clock is ticking when it comes to climate change. As more governments worldwide sign up to net zero emissions by 2050, the energy industry must embrace technologies—like Ebflow—that can help speed up the deployment of low carbon energy production.”
Sheffield Forgemasters is reportedly the only company in the UK with the capability to manufacture the large forgings required for small modular reactors. Now, according to CVE, it has years of developmental lead on global competitors in welding thick-walled assemblies.
“The implication of industrialized electron beam welding technology within the nuclear industry is monumental, potentially taking high-cost welding processes out of the equation,” said Sheffield Forgemasters Senior Development Engineer and Project Lead Michael Blackmore, Ph.D., in the release.
Professor Jesus Talamantes-Silva, Research, Design and Technology Director at Sheffield Forgemasters, said, “We are delighted to have reached a significant milestone in assembling a nuclear vessel demonstrator, using electron beam welding for the first time at this scale, with 100 per cent success and no defects.”
Ebflow is described as a local vacuum electron beam welding system, which can be readily transported and operated on-site and applied to structures significantly larger than those that can be accommodated in a vacuum chamber. It eliminates the need for a vacuum chamber through a local, coarse vacuum, which is established and maintained only where it is needed.
“Ebflow facilitates very high joint completion rates in thick-section metals and is 20-30 times faster than conventional submerged arc welding: achieving 200mm per minute in 150mm thick steel—allowing for the fastest thick-section rates ever,” the release stated.
The technology is the result of years of research and development by specialists at CVE, which is headquartered in Cambridge, U.K., with regional offices in the U.S. (Massachusetts) and China.
Airborne Technologies Approved by Lockheed Martin as Certified Supplier for Resistance Welding
CAMARILLO, Calif.—Airborne Technologies (ATI), a company that specializes in manufacturing, repairing, and overhauling critical aerospace components, was officially approved by Lockheed Martin (LMCO) recently as a certified supplier for resistance welding. In a company release, ATI described the milestone as “a testament to ATI’s unwavering commitment to excellence and adherence to the highest industry and customer-specific standards.”
“The approval reflects the confidence that LMCO places in ATI’s technical expertise, operational integrity, and robust quality assurance processes,” ATI stated in the release.
The certification reinforces Airborne Technologies’ position as a key supplier of high-quality, mission-critical components within Lockheed Martin’s supply chain. It authorizes ATI to perform spot welding on Lockheed Martin’s products “in strict compliance with the American Welding Society’s specification and LMCO’s proprietary specification.” ATI is a subsidiary of All Clear Aerospace & Defense, a global aerospace services company.
“The ATI team is proud to achieve the milestone of becoming an approved Lockheed Martin resistance welding supplier,” stated Anthony Grant, vice president and general manager of engineered products for AllClear, in the release. “This certification reflects both Lockheed Martin’s and ATI’s shared commitment to quality and reliability. We look forward to continuing our partnership with Lockheed Martin, providing sustainment solutions to keep our customers’ fleets mission-ready worldwide.”
Airborne Technologies said it maintains “a strong focus on delivering the highest quality products to its customers in the defense and commercial sectors.” The company is a Lockheed Martin-Certified Parts Program licensee. It has Boeing ANSI/ASQC Q9002 certification, as well as AS9100D and ISO 9001:2015 registrations compliance, the company stated.
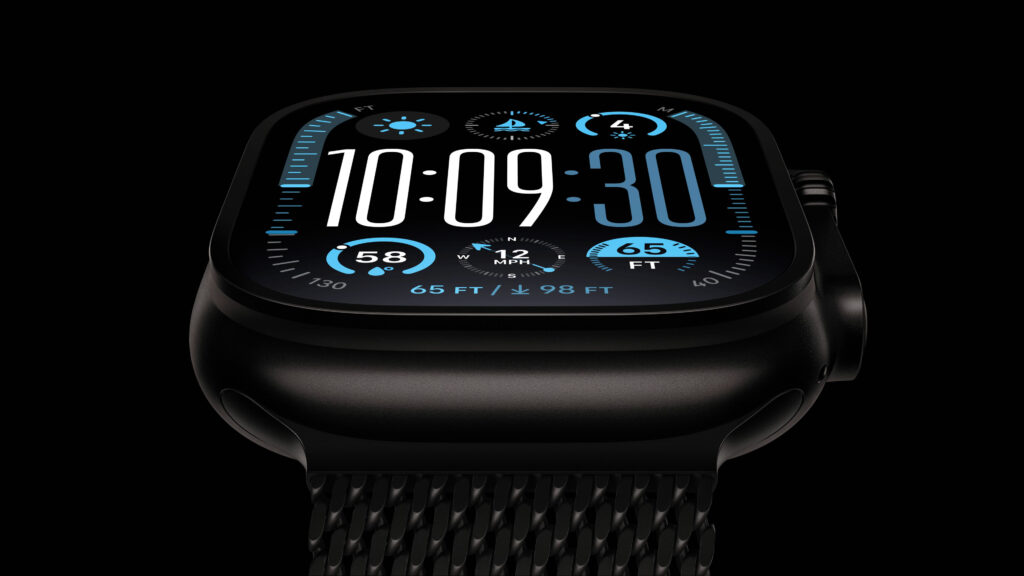
The Apple Watch Ultra 2 features a stunning black titanium finish and an aerospace-grade titanium band, manufactured using processes that include laser welding. (Photo: Business Wire)
Laser Welding Is Key in Creating New Titanium Sports Watch
CUPERTINO, Calif.—Those who are familiar with the Apple Watch Ultra® 2 know that its latest versions include a handsome black titanium finish and a corrosion resistant metal band, the Titanium Milanese Loop. These arresting new features are made possible, in part, by precision laser welding and custom finishing processes.
Apple describes its durable sports watch as “the most rugged and capable Apple Watch®.”
“Apple Watch Ultra 2 is the ultimate sports watch, with features that support athletes at every level of their training and performance—and throughout their day and night,” said Jeff Williams, Apple’s chief operating officer, in a company release. “The breakthrough insights in watchOS 11 make Apple Watch Ultra 2 even more powerful, and it’s now available in a stunning satin-black titanium finish users will love for its striking look and durability.”
The new black titanium finish for Apple Watch Ultra 2 is achieved through use of custom blasting and coating processes. After blasting, a diamond-like carbon physical vapor deposition coating was deposited onto the grade 5 titanium to make it scratch-resistant and durable, the release stated.
The Titanium Milanese Loop is the first metal band for the Apple Watch Ultra. The lightweight band is designed for use in water activities and reportedly inspired by mesh historically used by divers. According to Apple, it is “woven from the same aerospace-grade titanium as the case.” The band is manufactured via a custom process that includes weaving, flattening, and laser welding, as well as grinding and finely polishing the titanium wire.
The tailor-made process is said to result in “precise, interlinking lozenge shapes that provide a luxurious drape, complete with a dual-button, parachute-style buckle secure enough for all water sports.”
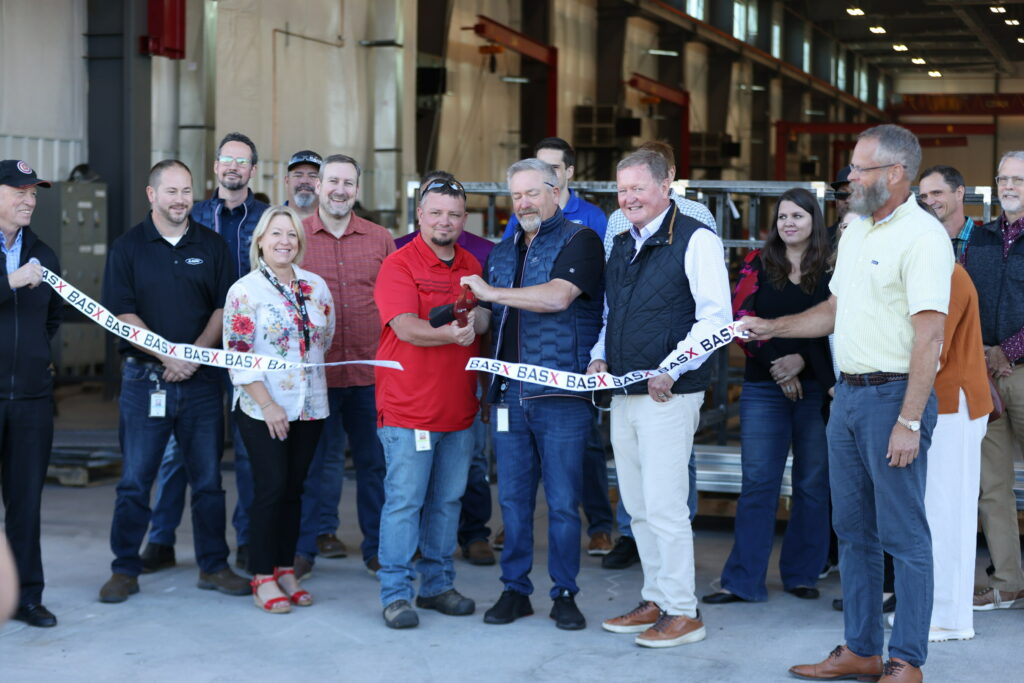
Members of BASX leadership, Redmond city counselors, the Redmond Chamber, REDI, and community partner Opportunity Foundation, take part in a ribbon cutting ceremony in front of BASX’s new weld shop in Redmond, Oregon. (Photo: PRNewswire)
Manufacturer of Data Center Cooling Systems Opens State-of-the-Art Weld Shop in Oregon
A new robotic welding cell, scheduled to be operational in early 2025, will enable BASX to weld large subassemblies of up to 10 tons.
REDMOND, Ore.—A newly completed, 36,000-square-foot weld shop at BASX company headquarters in Redmond is outfitted with state-of-the-art welding technology in a climate-controlled environment, marking a major expansion in the company’s production capabilities.
BASX, founded in 2014 in Central Oregon and acquired by AAON in 2021, is a manufacturer of high-efficiency data center cooling systems, cleanroom systems, and custom HVAC systems.
The company’s new weld shop is equipped with advanced air filtration systems, including an AAON make-up air unit and multiple air scrubbers, to ensure exceptional air quality for its workers. To enable efficient movement of materials across the facility, the space also features two 5-ton overhead cranes and six half-ton cantilever jib cranes, BASX stated in a release.
A 75-foot-long dual-zone robotic welding cell is scheduled to be installed and operational in early 2025, enabling the welding of large subassemblies up to 10 tons. For now, a key highlight of the facility is its cutting-edge tube laser, capable of precision cutting and profiling round and square tubes, as well as C-channel and I-beam profiles up to 27 feet in length, the company said.
The weld shop is expected to create significant job opportunities in the Central Oregon region, with the capacity to fill an additional 30 welding positions. Positions range from entry-level to experienced roles, with professional opportunities in various growing departments within the company.
“This new facility is a major investment not just in our company, but in the future of Central Oregon,” said AAON Vice President and BASX President Dave Benson, in a statement. “We can now deliver even higher levels of quality and efficiency while providing more job opportunities for the community. We’re proud to support local manufacturing growth and look forward to seeing the impact this expansion will have on both BASX and the region.”
According to BASX, the shop’s innovative capabilities will support the company’s growth and solidify its position for ongoing expansion. In addition to the 30 new welding jobs, BASX is actively hiring across various departments to support its continued success, the company said.
Beam Rotator Enables Better Weld Positioning for Large Structural Parts
KANARRAVILLE, Utah—The size differential between a lightweight, laser-welded watch band and a massive, welded steel beam couldn’t be more dramatic. What these two parts have in common is the need for accurate weld positioning, which, in both cases, is essential to ensuring the quality of the weld.
A company in Kanarraville, Utah, recently developed a new technology for welders of heavy steel beams that is reported to optimize weld positioning (see New Beam Rotation System Reported to Optimize Weld Positioning, Improve Operator Safety).
BZI®’s R&D group, Innovatech®, stated in a release that its Beam Champ® 30 beam-rotating system improves welders’ access to all sides of the beam, reducing the risks associated with beam handling and enabling safer and more efficient welding. Customers have reported experiencing a 20 percent improvement in productivity since they began using Beam Champ in their operation, the company said.
The Beam Champ 30 is reported to address practical needs like beam placement, removal, and secure positioning. It cradles the beam on a chain, rotating it within two or more Beam Champ units. One of its advantages over previous beam rotators is a support arm that holds the beam securely in place during welding or configuration, BZI said in the release.