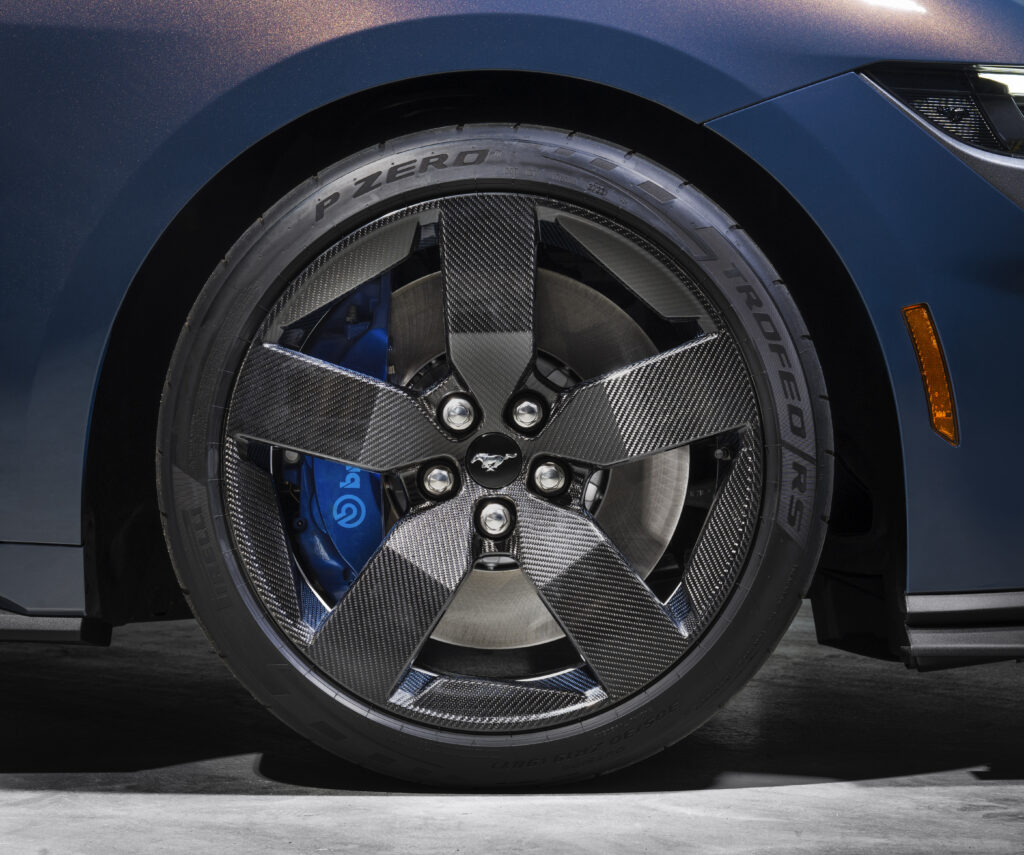
A carbon fiber wheel on the 2024 Ford Mustang Dark Horse. Carbon Revolution developed a proprietary thermal barrier coating system that tailors its plasma spray deposition technology to provide thermal protection for carbon fiber wheels. (Photo courtesy Ford Motor Company)
Manufacturers are leveraging innovative technologies from carbon fiber wheels to state-of-the-art wind tunnel testing systems to design and produce high performance vehicles.
By Mark Shortt
Automotive manufacturers were among the early adopters of automation and robotics as tools for increasing production efficiency and quality. Although these tools remain a core capability in many plants, they’re now being complemented by a host of other innovative technologies focused on the same improvements.
Today’s auto manufacturers and suppliers are employing state-of-the-art technologies from carbon fiber parts manufacturing to 3D printing, protective coating, rolling road wind tunnel testing, and advanced stamping presses for all-electric vehicles. Companies are also increasingly integrating artificial intelligence (AI) into their design, development, and production processes.
“AI is integrated into various stages of product development, from design to the assembly of the vehicle,” said Vivek Kumar, automotive project manager at market intelligence firm GlobalData, in a release. “The incorporation of AI enhances the creation of alternative and more efficient vehicle designs, streamlines prototype development, optimizes production and assembly processes, and improves vehicle testing. Additionally, AI plays a crucial role in supply chain management, ensuring a seamless and efficient workflow throughout the entire development cycle.”
Manufacturers are finding AI to be of particular benefit in making improvements to the efficiency of their manufacturing processes.
“The integration of AI in automotive manufacturing has significantly boosted production efficiency,” Kumar added. “Manufacturers use AI-generated design algorithms to explore multiple design possibilities, optimizing vehicle weight, strength, packaging, and performance. This leads to the creation of lighter, more efficient vehicles.”
The use of carbon fiber wheels on automobiles has historically been limited to supercars and high-performance racing applications. But as technologies for manufacturing them evolve, the durable, lightweight wheels are penetrating new markets and becoming available on a wider range of vehicles.
One of those vehicles is the 2024 Ford Mustang Dark Horse, a street- and track-cable performance car with improved aerodynamics and a powerful 5.0-liter V8 engine. In a release introducing the Mustang Dark Horse, Ford Motor Company CEO Jim Farley called the car “a track-capable Mustang that puts a new level of performance, styling, and American engineering in the hands of everyday customers who still want the thrill and excitement of a V8 sports car.”
The Mustang Dark Horse is expected to “deliver the highest level of performance in the all-new Mustang family,” according to Ford. It features what the automaker described as a “unique 5.0-liter Coyote V8 engine, specially modified with piston connecting rods” that were first seen in the 760-horsepower Ford Performance Mustang Shelby GT500. The car also features a “six-speed TREMEC manual transmission that connects to the driver through a standard 3D-printed titanium shift ball,” the release stated.
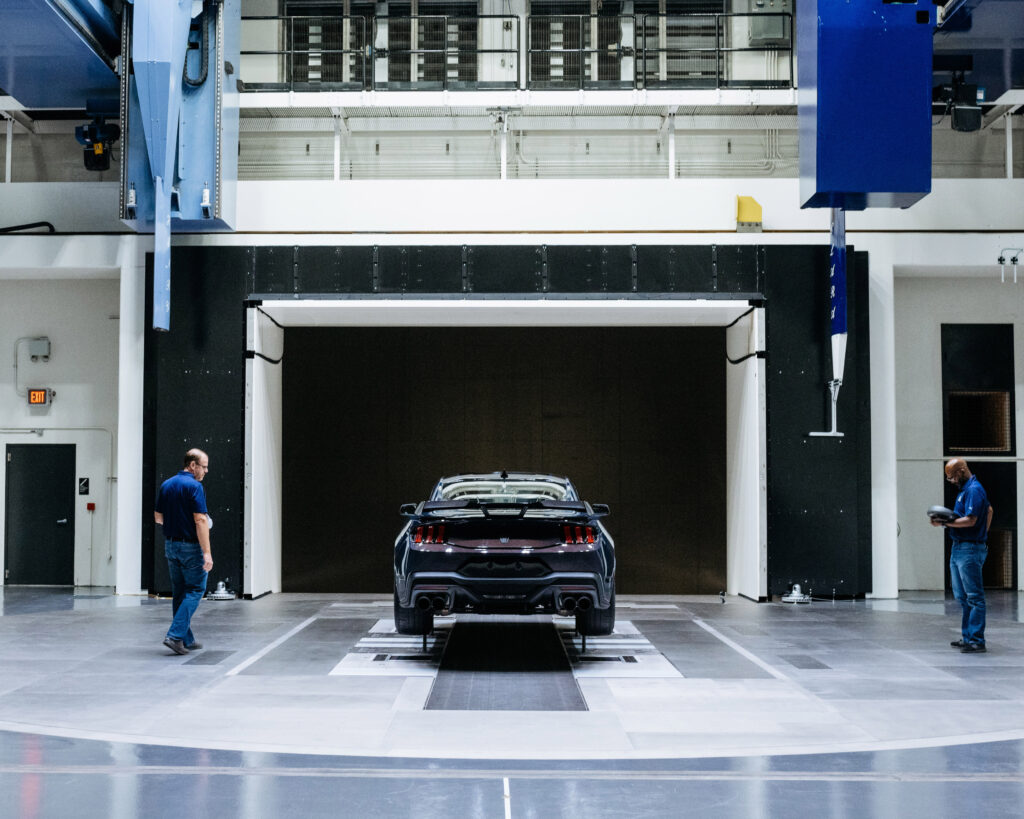
Ford’s Rolling Road Wind Tunnel features a five-belt system that replicates real-world drag through a rolling road aerodynamic tunnel. (Photo courtesy Ford Motor Company)
“We’ve taken the all-new Mustang, the best of our new 5.0-liter V8 performance, and added power, improved the aero, tires, steering, and provided an interactive cockpit to create a Mustang that goes beyond any 5.0-liter Mustang before it,” said Ed Krenz, Ford Mustang chief nameplate engineer, in a statement.
At an average weight of 20.1 pounds, the Mustang Dark Horse’s carbon fiber wheels are “roughly 37 percent lighter, on average, than Dark Horse aluminum wheels,” according to Ford. The weight differential is responsible for higher fuel efficiency, and it’s made possible by Ford’s collaboration with Carbon Revolution, a Tier 1 OEM supplier and global manufacturer of lightweight, advanced technology carbon fiber wheels for the automotive industry.
Carbon Revolution used a process inspired by aerospace technology to protect the 2024 Mustang Dark Horse wheels from brake heat. Aerospace manufacturers have long treated turbine blade materials with ceramic coatings to improve their durability in conditions of extreme heat. Similar technology is also used in “top-tier open-wheel racing environments,” Ford said on its website.
Carbon Revolution reportedly leveraged a “plasma arc spray process to deposit a combination of ceramic and metal materials inside the front wheels.” The process is part of a proprietary thermal barrier coating system developed by Carbon Revolution that can tailor its plasma spray deposition technology to provide thermal protection for carbon fiber wheels, Ford said in the release.
Rolling Road Wind Tunnel Bolsters Aerodynamic Design, Testing
Another technology that aided Ford’s development of the Mustang Dark Horse is an in-house Rolling Road Wind Tunnel (RRWT) that enables the automaker to “bring the road to the vehicle, rather than the vehicle to the road,” the company said in a release.
By combining the latest wind tunnel technology with the equivalent of a vehicle-sized treadmill, Ford’s Rolling Road Wind Tunnel supports aerodynamic R&D and testing for the next generation of Ford electric, hybrid, and gas vehicles. It is reportedly capable of simulating wind and road surface speeds of 200 mph.
“The amount of air moved by our wind tunnel is enough to fill a K-Class blimp in just over five seconds,” said Ford North America Wind Tunnels Engineering Supervisor John Toth, in the release.
The Rolling Road Wind Tunnel is said to provide a significant benefit that earlier wind tunnel designs lacked—more accurate data for wind drag and downforce. Both of these variables are key factors when optimizing vehicle designs for range and efficiency. The wind tunnel also enables Ford to perform more in-house testing that simulates open-road conditions, which can help reduce design costs and accelerate the design process, the company said.
“The closer we can get to reality in the lab, the better and faster we can create more energy- efficient vehicles with great on-road and track stability,” Toth continued. “Testing while the wheels and tires move is instrumental to improving aerodynamics for track-ready vehicles, like Mustang Dark Horse, which has to balance both aerodynamic drags and downforce.”
The Rolling Road Wind Tunnel reportedly features a new five-belt rolling road system that replicates real-world drag through a rolling road aerodynamic tunnel. Each of the four wheels is situated on its own belt to test for optimal aerodynamic performance. The fifth belt is a larger belt that runs under the center of the vehicle, the company said.
“A crane is used to switch between the five-belt and single-belt systems—an industrial-sized plug-and-play,” the release stated. “The single belt, which operates at up to 200 mph, opens up a new breed of testing for high-speed performance vehicles.”
Increasing Downforce
Tailored aerodynamics are a key step in the development of new vehicles, according to Ford.
To create more efficient passenger vehicles and trucks, the goal is to achieve low drag. But vehicles that prioritize track-ready performance, such as the Mustang Dark Horse, require a different calculus.
“Aerodynamicists will trade low drag for increased downforce, which helps cars stick to the road or track and improves handling feel while cornering,” the company said in the release.
At the time of its introduction, the 2024 Mustang Dark Horse had “the most downforce of any 5.0-liter Mustang when equipped with the available handling package,” according to Ford.
Available on the vehicle is a Gurney flap—an extra plate attached to the rear wing to help generate additional downforce. Also available are three vertical plates, called strakes, that come off the underbody near each front wheel. By helping to disrupt airflow, the strakes generate greater downforce on the underside of the vehicle. This can help the car stick better in corners at higher speeds, the company said.
The Mustang Dark Horse, overall, is said to incorporate multiple changes and additional features. Among them are a redesigned front bumper, a lower valence, a spoiler, and unique wheels.
“The front design is optimized to potentially increase air flow for engine cooling, brakes, and air intake, while also reducing front lift,” the release stated. “On the Mustang Dark Horse, the lower air spoiler and splitter is unique, allowing the car to be tuned for greater downforce.”
According to Ford, the upgraded handling package “provides a unique splitter, spoiler, and wheels.” Although these changes may seem small, they can make a big difference when hitting the road or track with performance in mind, the company said.
“We spent approximately 250 hours in the wind tunnel developing the 2024 Ford Mustang, which includes Dark Horse,” said Program Aerodynamicist for Mustang and Bronco, Jonathan Gesek, in the release. “The aerodynamics of Mustang Dark Horse, along with several other factors, have created the most track- and street-capable 5.0-liter Mustang to date.”
Carbon Fiber Wheels Boost Efficiency, Performance of Corvette Models
Carbon Revolution’s carbon fiber wheels are also available on General Motors’ 2024 Chevrolet Corvette C8 E-Ray, the Corvette C8Z06, and the newly revealed Corvette ZR1.
The E-Ray is the first all-wheel drive Corvette and the first Corvette to use electric power in addition to its V8 engine, according to a release from Carbon Revolution. In the release, Carbon Revolution CEO Jake Dingle said the company’s lightweight wheel technology is “synonymous with the Corvette E-Ray’s philosophy of maximizing efficiency and performance.”
“The world is shifting to electrification and new mobility, and Carbon Revolution wheels are an ideal solution for carmakers looking to improve efficiency and performance of electric vehicles,” Dingle stated. “The E-Ray will transform the C8 Corvette’s efficiency by offering hybrid power. The addition of Carbon Revolution wheels enhances the E-Ray’s performance and efficiency through a significant reduction in unsprung, rotational mass.”
Carbon Revolution’s five-spoke, single-piece carbon fiber wheels are reported to reduce rotating, unsprung mass on the Corvette E-Ray by 41 pounds versus the forged aluminum option. One option for the wheels is to paint them in a Carbon Flash metallic finish. Additional options include a visible carbon fiber weave that features Carbon Revolution’s Diamond Weave Technology™, and a visible carbon fiber weave with a red strip and branding option, according to a company release.
On the Corvette ZR1 halo car, Carbon Revolution’s one-piece carbon fiber wheels are substantially lighter than aluminum wheels, reportedly lowering the ZR1’s rotating, unsprung mass by 42.8 pounds (19.4 kg) across the vehicle. Dingle said in another company release that the wheel’s performance during testing reflected “the talent and experience of Carbon Revolution’s product and manufacturing engineering teams in meeting GM’s weight, durability, strength, and aesthetic standards.”
“The thin, split-spoke design of our wheels for GM highlights what is possible with carbon fiber,” Dingle said in the release. “When you compare [it] to some of our earliest designs, coupled with the highest load rating yet for a performance car, you can see how much we have progressed with our world-leading technology. The final product is one that our team is very proud of that enhances the Corvette ZR1’s performance.”
To address complex load paths in the wheel’s hub geometry and around the bolted joint, the Carbon Revolution team developed a unique internal fiber architecture. This advancement, along with Carbon Revolution’s patent-pending Diamond Weave Technology™, proved critical to achieving GM’s lofty targets for “strength, weight, and durability in a thin, split five-spoke design,” according to the release
The ZR1’s front wheels are 20 inches tall and 10 inches wide; the rear wheels, 21 inches tall and 13 inches wide—identical to the measurements of the E-Ray. “The rear wheels are the world’s widest carbon fiber wheels, alongside Carbon Revolution’s rear wheel for the eighth-generation Corvette Z06 and the E-Ray,” the release stated.
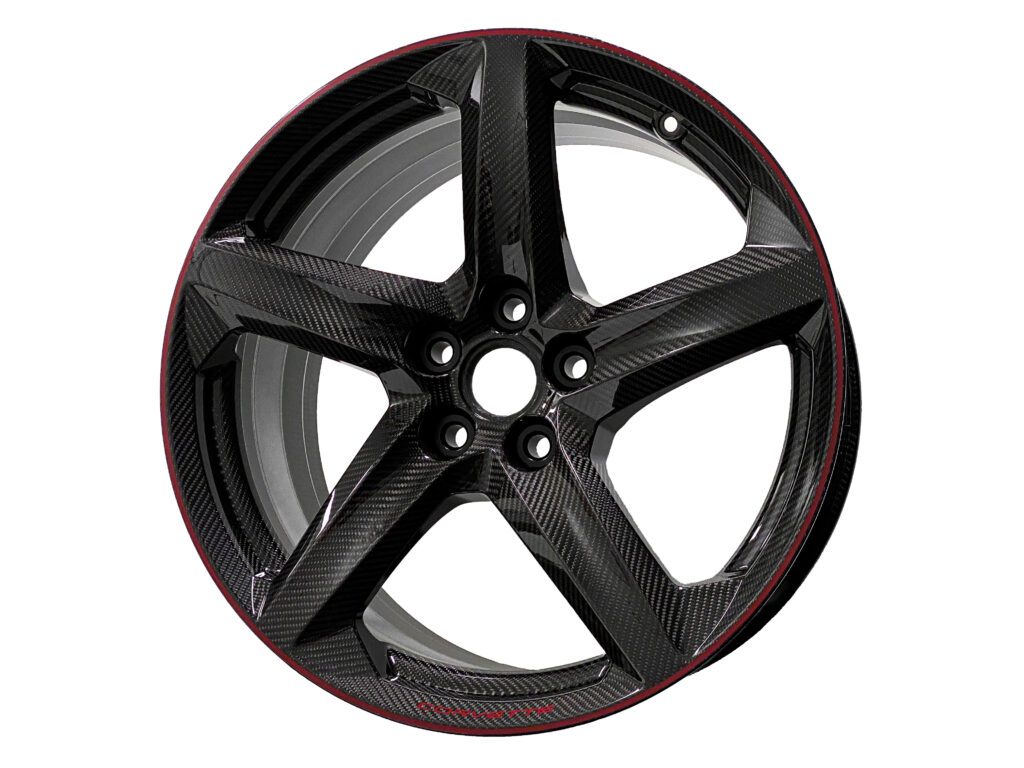
A wheel with a visible carbon fiber weave featuring Carbon Revolution’s Diamond Weave Technology. (Photo courtesy Carbon Revolution)
Growing Demand in New Mobility Markets
Since its founding in 2007, Carbon Revolution has steadily gained traction as an industry innovator. While working to advance its technology, the company has secured contracts with automakers Ferrari, Renault, and Jaguar Land Rover, as well as Ford and General Motors. The company received the 2023 Vehicle Engineering Team Award (VETA) from the SPE Automotive Division for its technical excellence in supplying single-piece carbon fiber wheels for the 2024 Chevrolet Corvette E-Ray.
Carbon Revolution also received awards for supplier innovation and OEM collaboration at the 2024 Automotive News PACE Awards. The supplier was recognized for the superior innovation and technological advancement of its lightweight carbon fiber wheels, and for its collaboration with GM in designing and supplying carbon fiber wheels for the C8 Corvette Z06 and E-Ray.
Now, with the automotive industry in the midst of a steady transition to electric vehicles, Carbon Revolution is aiming to meet growing demand in new mobility markets. The company is banking on the potential of its lighter weight carbon fiber wheels to alleviate a formidable obstacle to greater adoption of electric vehicles—range anxiety.
Weighing as little as half the weight of aluminum wheels, the company’s carbon fiber wheels are reported to deliver “up to a 5 percent to 10 percent increase to vehicle range, if associated weight reduction were to be reinvested in battery mass,” according to a company release.
“Carbon Revolution’s wheels provide significant unsprung mass reductions, which can greatly improve efficiency and reduce road noise while also helping lead global automakers to comply with the Corporate Average Fuel Economy (CAFÉ) targets set by the National Highway Traffic Safety Administration (NHTSA),” the company said in the release.
“We see an enormous addressable market for Carbon Revolution’s disruptive efficiency technology, with adoption already underway with major car manufacturers,” Dingle said in a release announcing a business combination agreement with Twin Ridge Capital Acquistion Corporation in November 2022. “Carbon Revolution’s technology provides an effective next-generation solution to the challenges of transitioning the global automotive industry to new mobility. We have a strong track record working with leading OEMs and a world-class team with a passion for our work.”
Inside BMW’s High-Tech Press Shop
The press shop marks the beginning of the automotive production process. Large steel coils are unloaded from trucks using a large overhead crane inside the shop. The steel coils are then fed into the Coil Line, where the steel is cut into individual “blanks” (rectangular cutoffs or special shapes) at up to 70 strokes per minute. These blanks are then ready to be fed into the Press Line.
The Press Line consists of five press (stamping) stations. The line is equipped with servo technology, which enables BMW to significantly increase the output performance of the presses.
An overhead crane moves the correct press tool (die) into each station. The blank is fed into the first press station and transferred from one station to the next by a robot-like automation technology, referred to as the “crossbar feeder,” for additional forming and trimming operations. The line can run up to 18 strokes per minute, which means up to 10,000 parts can be stamped each day, depending on the size of each part.
After the parts are stamped, they go to quality control for inspection; quality inspectors use special lighting that mimics natural daylight. Parts are then stacked into racks ready for delivery to the body shop production line.
Underneath the press and coil lines are areas that collect the scrap metal gathered after the parts are stamped. As much as 50 tons of scrap are accumulated each day at full volume; a long conveyor moves the scrap, and it is loaded onto 53-foot trailers. All this material is taken off-site to be recycled.
Source: BMW Group
State-of-the-Art Press Shop Will Stamp Sheet Metal Parts for BMW Electric Vehicle
In June, BMW Manufacturing celebrated its 30th anniversary of assembling BMW vehicles at its plant in Spartanburg, South Carolina. As part of the ceremony, the company opened a new state-of-the-art press shop at the facility, where it will begin assembling its newly revealed, all-electric BMW X3 Sports Activity Vehicle in 2026, according to a company release.
The new press shop will stamp sheet metal parts for the new BMW X3, a fourth-generation vehicle that was introduced to attendees at the ceremony. Components to be manufactured at the facility are reported to include hang-on parts such as the vehicle’s four doors, fenders, lift gate, and exterior body sides.
Milan Nedeljković, Ph.D., a member of BMW AG’s Board of Management and responsible for production, delivered remarks at the ceremony in which he emphasized BMW Group’s commitment to manufacturing in the United States, the release stated.
“After 30 years of successful operations, we are further expanding our commitment,” Nedeljković said in his remarks. “At the end of 2026, assembly of all-electric Sports Activity Vehicles will start here in Spartanburg. This is a further step towards strengthening our global resilience.”
The BMW Group said that by 2030, it expects to assemble at least six fully electric models in the United States. High-voltage batteries for future battery-electric vehicles (BEVs) to be assembled at the Spartanburg plant will be produced in nearby Woodruff, where the BMW Group is building an assembly plant for sixth-generation batteries.
The opening of BMW Manufacturing’s new press shop “also contributes to strengthening the U.S. footprint,” the release said.
“The advanced stamping processes on our new press line will ensure the highest quality, efficiency, and consistency in body shop parts for our customers,” said Robert Engelhorn, Ph.D., president, and CEO of BMW Manufacturing, in the release. “Having this press shop onsite fits the BMW Group’s local-for-local strategy where we produce major parts at the location where we need them.”
The BMW Group reported that it invested more than $200 million to construct the 219,000-square-foot press shop. It took 24 months from site work preparation to stamping the first part on the press line, the company said.
The company’s investment is also said to have included more than 200 new jobs for personnel such as tool and die technicians, as well as electrical and mechanical maintenance for automated machinery. Dozens of Plant Spartanburg associates trained at BMW Group press shops in Swindon, in the UK, as well as in Leipzig, Germany, the company said.