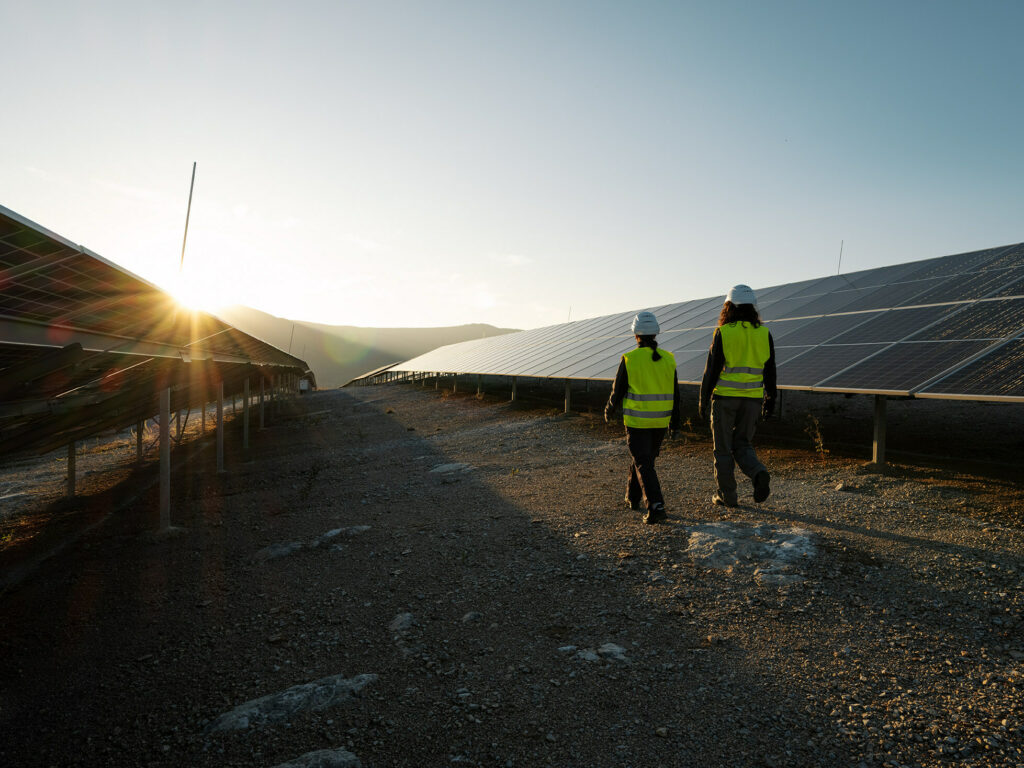
Stäubli North America recently announced major new investments to expand its domestic manufacturing and assembly operations by increasing capacity at its plants in South Carolina and California. (Photo: Stäubli/PRNewswire)
The company is working to support increased demand for domestically made, high-quality connectors and wire harnesses, driven in part by the U.S. Inflation Reduction Act.
WINDSOR, Calif.—Stäubli North America has made “major new investments” to expand its North American manufacturing and assembly operations by increasing capacity at its U.S. plants in South Carolina and California, the company said in an April release.
Known for manufacturing electrical connectors—such as its MC4 connector—for solar photovoltaic (PV) equipment, Stäubli describes itself as “a market leader in connecting more than 50 percent of PV capacity worldwide, ensuring long-lasting and reliable solar power transmission.”
Stäubli established its North American presence in 1980 in Duncan, South Carolina, where it operates a 103,000-square-foot manufacturing and logistics facility to support customers of its Fluid Connectors, Robotics, and Textile Divisions. In 2011, the company expanded with a 43,000-square-foot facility in Windsor, California, that manufactures electrical PV connectors and other products.
“We plan to steadily increase our made-in-America products at these manufacturing facilities,” said Stäubli Head of Renewable Energy North America, Brian Mills, in the release. “Increasing our already established solar connector manufacturing footprint in the U.S. puts Stäubli in a strong position to support the increasing demand for domestically made components, driven in part by the Inflation Reduction Act of 2022.”
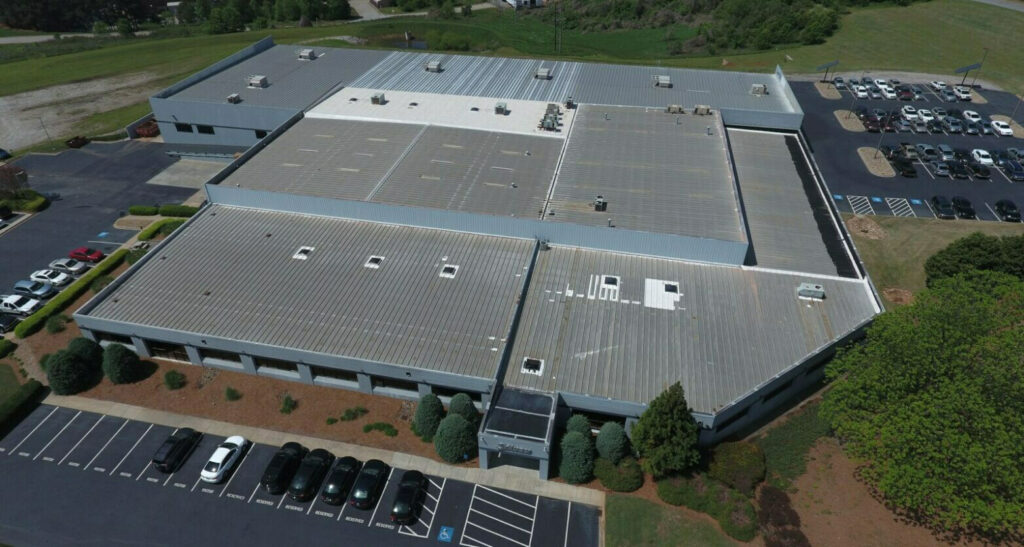
An aerial view of Stäubli’s Duncan, South Carolina facility. (Photo: Stäubli/PRNewswire)
According to the release, Stäubli North America has manufactured PV components in the United States for more than 15 years. The company’s history of domestic manufacturing includes a wide range of solar products, from junction boxes to in-line fuses and eBOS products. Among them are components like Stäubli’s original MC4 and MC4-Evo 2 cable couplers; the first PV cable coupler for 6 AWG; and modular DC wire harnesses.
In addition to its capital investments in domestic manufacturing, Stäubli North America said it has added capabilities to its locally-based field engineers, design engineers, and test lab resources to provide a new customer offering of field services and technical training.
“This comprehensive support is unique in the industry and extends through each critical stage of a solar project: from initial design, through pre-construction and construction, right up to the operational phase,” Mills said in the release. “This includes support of proper product selection and assembly, optimized design for limited waste and power loss, and proper implementation of the product in the field to ensure that our customers achieve safe and reliable solar installations.
“Our advanced manufacturing operations employ the latest automation with 100 percent inspection to maintain the highest standards in quality, performance, safety, and sustainability,” he continued. “Plus, we have the agility to serve specific sectors with customized engineering to-order and make-to-order solutions to meet our customers’ specific requirements.”