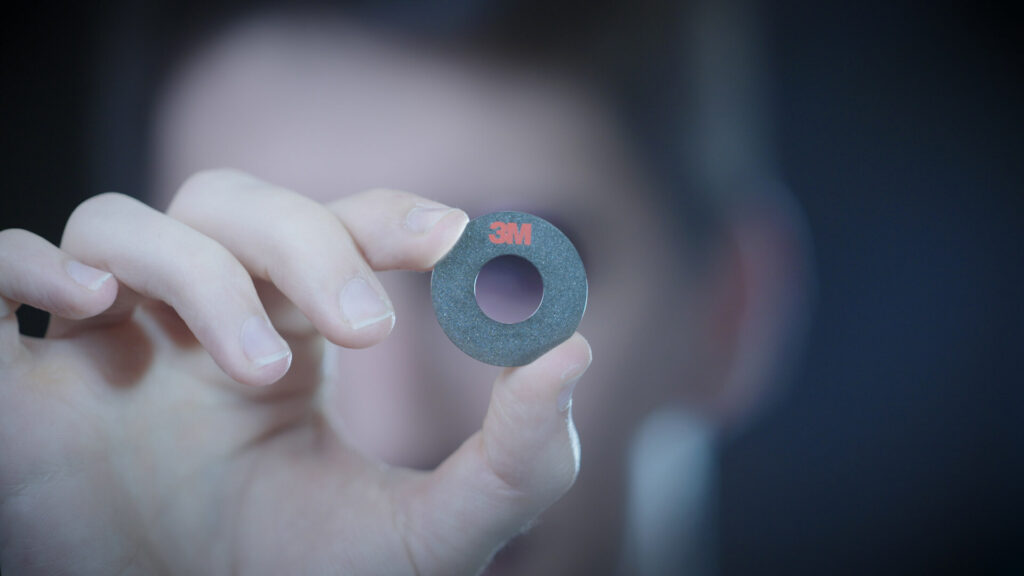
The 3M™ Friction Shims are reported to increase maximum load and peak torque in bolted connections without additional fasteners or redesigns. (Photo courtesy 3M/PRNewswire)
3M’s Friction Shims are said to fit within most engineering tolerances, allowing for lightweight, compact designs in demanding automotive applications.
ST. PAUL, Minn.—Despite their size, the small, thin steel shims manufactured by 3M Company are having a big impact in demanding automotive, wind energy, and aerospace applications.
The company said in a release that it has made and sold more than 300 million 3M™ Friction Shims worldwide. The friction shims are reported to increase maximum load and peak torque in bolted connections without additional fasteners or redesigns.
“This is a significant milestone for us because we know 3M Friction Shims help our customers improve their design,” said Amy McLaughlin, president of 3M’s Advanced Materials Division, in the release. “We are very proud that we’ve now made and sold more than 300 million worldwide. 3M Friction Shims are a simple solution for stronger and more stable bolted connections.”
The 3M Friction Shims are said to increase friction coefficients in torsional and static joints, particularly in demanding automotive applications. Nickel-coated steel shims contain partially embedded diamond particles that resist breakage. When applied with pressure between two mating surfaces, the diamonds “bite” into each surface to create a microform fit, the company said in the release.
This is said to allow for a coefficient of static friction up to five times greater than in a conventional bolted connection—especially valuable as electric vehicles take center stage in the global marketplace. Heavy lithium-ion battery packs, combined with higher torque, can often put considerably more strain on critical chassis and battery mount joints, according to 3M.
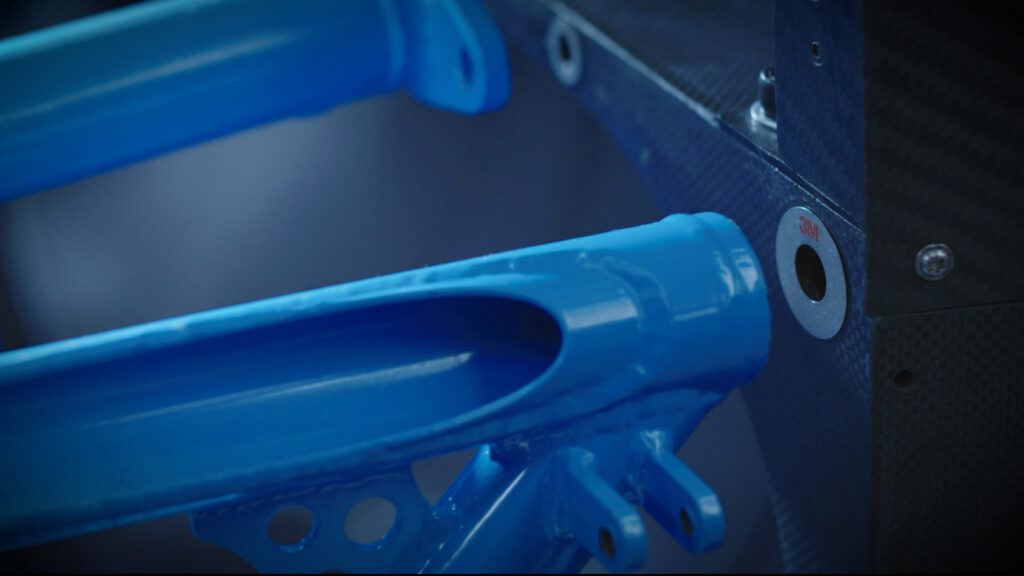
The shims increase friction coefficients in torsional and static joints, particularly in demanding automotive applications. (Photo courtesy 3M/PRNewswire)
The small, thin shims reportedly fit within most engineering tolerances, allowing for lightweight, compact designs. They can also be used as a drop-in solution to stabilize joints further down the manufacturing chain. Friction Shims can be used in a wide range of applications, including shear joints in automotive chassis; torsional joints; flange joints; joints with a central bolt; bolted connections; and fastener systems.
According to 3M, engineers can use the friction shims to secure critical joints in chassis, battery mounts, suspensions, and other critical areas in internal combustion and electric vehicles. They can use them to optimize design for multi-material automotive structures to withstand higher force loads without changing parts or part sizes.
Engineers can also use the shims to enhance their pursuit of lightweighting goals by achieving the same shear and peak load performance using fewer smaller and lighter mechanical fasteners. Another use is to manage noise, vibration, and harshness (NVH) by dampening micromovements in bolted joints—a tactic that enhances passenger experiences and increases joint life, the company said.
3M supplies its Friction Shims in various grades for specific friction coefficients and related shear or torque requirements. The shims can be specified for ultra-thin torsional crankshaft or camshaft assemblies, or to create form fits even through e-coatings and rough surfaces.
According to the company, pre-assembly solutions include inner clips for faster installation. Friction Shims can also be disassembled and reused.