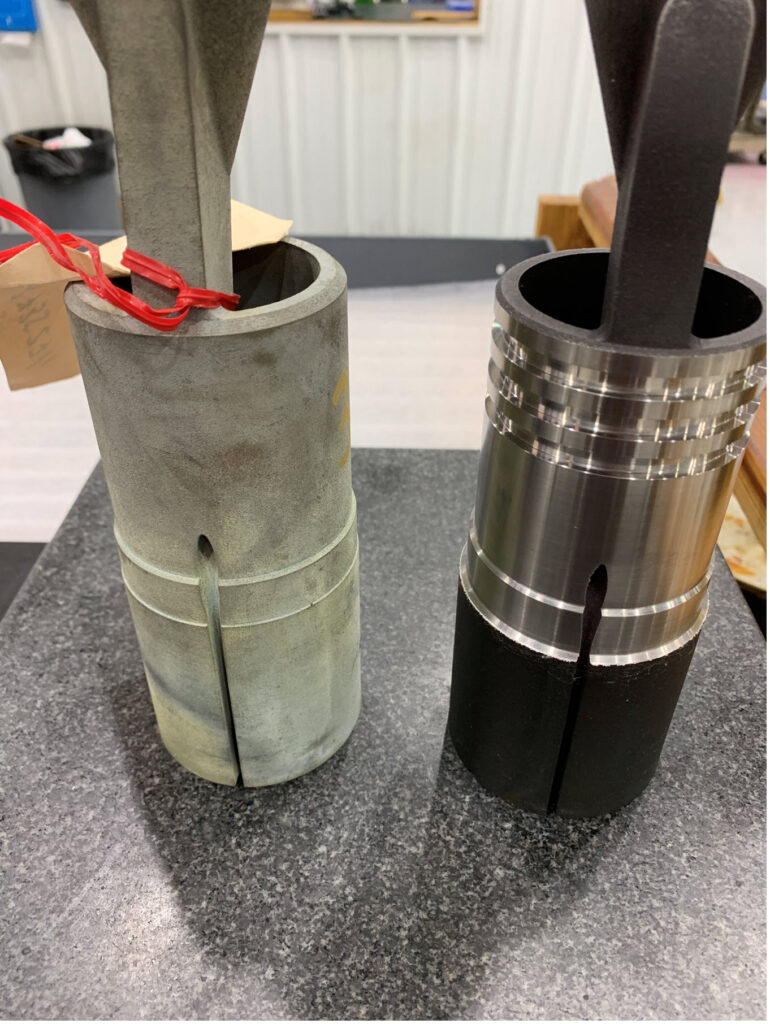
A 3D-printed part (left) used in the oil and gas industry, transformed through precision machining (right) to meet exacting specifications. When bulk parts reach end-of-life, their material can now be recycled using Continuum’s proprietary, single-step Greyhound M2P platform, with new, high-quality materials provided back to the manufacturer via the Continuum Powder as a Service (CPaaS). (Image courtesy Knust-Godwin)
Continuum Powders was selected by contract manufacturer Knust-Godwin for a lifecycle management project involving nickel alloy parts for an oil and gas company.
HOUSTON—Part quality and sustainability are key requirements for companies seeking to recycle metal alloy parts approaching end-of-life. But it’s not always easy to find materials providers who can meet the stringent standards required for recycled metal parts.
A materials company that checks this box is Continuum Powders, a producer of high-performance, sustainable metal powders. Continuum is the creator of The Greyhound M2P (melt to powder) Platform, a patented cradle-to-cradle process of recycling alloyed metal waste-stream products into powder in a single processing step.
According to a release from Continuum Powders, the platform makes it possible for customers to receive the same high-quality spherical metal powder they use today. It also contributes significantly to their decarbonization and sustainability programs by using Continuum Powders’ “nearly carbon-free powder materials.”
“Continuum Powders is the only company that can combine industry-leading quality with extreme alloy flexibility, supply chain independence, and cost competitiveness, while dramatically reducing carbon footprint versus traditional powders,” the company said in the release.
The need for a provider like Continuum Powders became apparent to a large oil and gas company recently when it needed to recycle metal alloy parts. The company had numerous Ni718-grade internal products that were nearing end-of-life and needed a cost-effective means to recycle the parts. The oil and gas company approached contract manufacturer Knust-Godwin, who researched industry offerings to determine the best available solution.
An existing Knust-Godwin customer recommended that the firm evaluate Continuum Powders.
Initially, Knust-Godwin was skeptical of recycled powder. But after multiple mechanical test coupons showed that Continuum Powders’ products met or exceeded other leading non-sustainable powder suppliers, Knust-Godwin selected Continuum Powders as the exclusive metal powders supplier for the project.
“Continuum is doing things that no other metal powders company can currently do when it comes to complete lifecycle management of consumable metal parts,” stated Rob Higby, chief executive officer of Continuum Powders, in the release. “With the incredible advancements we’ve made in converting worn parts into new metal powders, it no longer makes sense to simply scrap those parts and purchase metal powders made from virgin metals.”
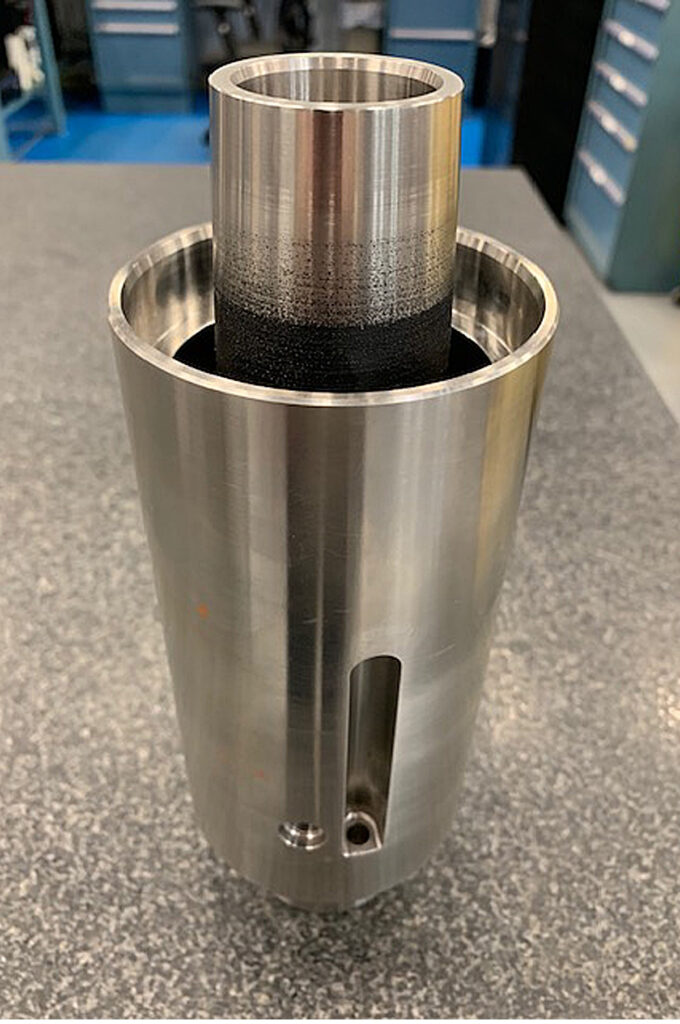
A finished oil and gas component, featuring a specialized coating on the interior diameter to reduce wear and extend operational life. (Image courtesy Knust-Godwin)
Continuum Powders was able to recycle end-of-life bulk parts easily with its proprietary, single-step Greyhound M2P (melt-to-powder) platform. It also supplied Knust-Godwin with new, high-quality Ni718 through its Continuum Powder as a Service (CPaaS), the company said in the release.
Knust-Godwin was then able to manufacture new parts for its customer using a Renishaw RenAM500Q printer. Following this project, Knust-Godwin realized the power of using Continuum’s M2P process for recycling manufacturing by-products like oversized or sieved powder.
“Continuum Powders consecutively proved to have the highest quality powders on the market—equal to or above that of all other manufacturers,” stated Michael Corliss of Knust-Godwin, in the release. “When you combine that level of quality with the level of sustainability they offer and their Powder as a Service offering, it makes them our de facto go-to provider.”
Continuum Powders describes itself as “the only company that can combine industry-leading quality with extreme alloy flexibility, supply chain independence, and cost competitiveness while dramatically reducing carbon footprint versus traditional powders.” The company is a portfolio company of Ara Partners, a global private equity firm focused on decarbonizing the industrial economy.