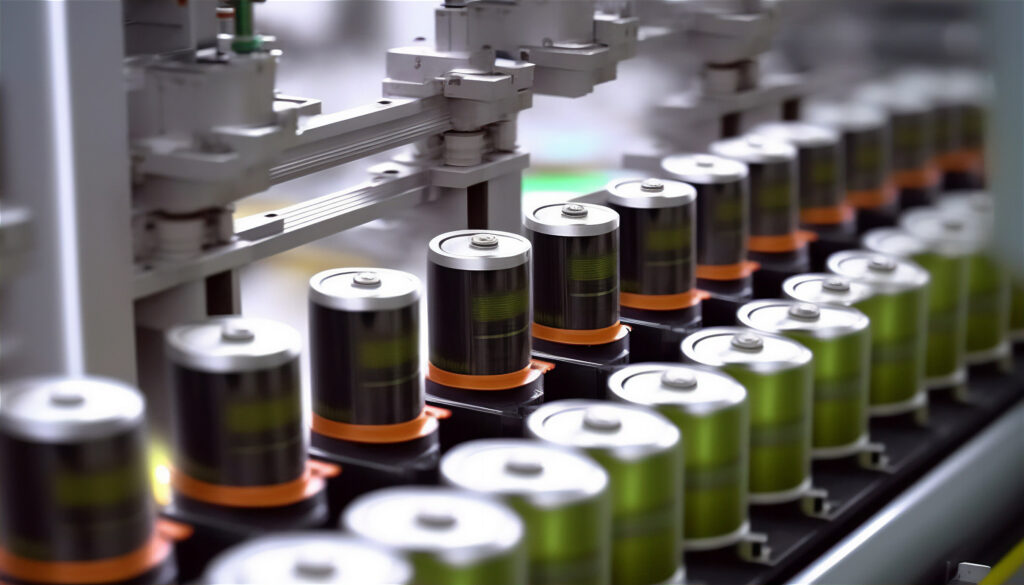
Honeywell’s Battery MXP is designed to cut time to full production, reduce material scrap, and increase delivery rates for battery manufacturers. (Image: Honeywell/PRNewswire)
Honeywell’s platform could reduce cell manufacturing costs, compress production ramp-up cycles, and cut material waste by 60 percent at startup, the company said.
HOUSTON—A new artificial intelligence (AI)-powered software platform developed by Honeywell is designed to optimize the operation of gigafactories by improving battery cell yields and expediting facility startups for manufacturers, Honeywell said in a release.
With traditional standalone software, battery manufacturers’ material scrap rates can be as high as 30 percent at steady state and even higher during the facility startup process, according to the report, Automotive Lithium-ion Cell Manufacturing: Regional Cost Structures and Supply Chain Considerations (nrel.gov).
“This practice can lead to millions of dollars of wasted energy and material while a gigafactory slowly scales to a more efficient and profitable production over several years,” according to the release.
Honeywell’s Battery Manufacturing Excellence Platform (Battery MXP) incorporates AI techniques in the manufacturing process, enabling the detection and remediation of quality issues before they result in scrapped material. The platform then uses machine learning to identify conditions that lead to quality issues and turns this data into action-oriented insights that manufacturers can use to improve efficiency and productivity, the company said in the release.
Battery MXP is reported to deliver “powerful data that can improve quality control and decision making on the plant floor.” As such, it is designed to help manufacturers cut production ramp-up time, reduce startup material scrap rates by 60 percent, and increase delivery rates to meet the growing demand for lithium-based batteries, according to Honeywell’s internal data testing of the Battery MXP in its pilot phase.
“With Honeywell’s Battery MXP and its automation capabilities, we will be able to quickly and effectively establish a foundation for our network of gigafactories,” said John Kem, president of American Battery Factory, in the release. “This solution is vital in our manufacturing operation because it allows us to reduce scrap and scale up quickly, while also ensuring we meet the U.S. and international demand for high quality lithium iron phosphate batteries as we prepare for the unprecedented surge expected over the next decade.”
By providing bidirectional traceability and genealogy, Battery MXP is said to track battery cells from raw material to finished product in real time, helping to ensure product quality at every step. The platform is also said to help address other key challenges faced by battery manufacturers by offering solutions for process controls, workforce management, and prevention of battery fires caused by thermal runaway. These safety elements help operators in the gigafactory and end-users of the batteries to stay safe, the company said.
“The electrification of everyday life continues to increase global demand for quality lithium-ion batteries to power electric vehicles, consumer electronics, and battery energy storage systems,” said Pramesh Maheshwari, president of Honeywell Process Solutions, in the release. “With the construction of more than 400 gigafactories planned worldwide by 2030, Honeywell’s Battery MXP is a crucial technology that enables manufacturers to maximize cell yields and reach peak production much quicker than traditional methods.”
According to Honeywell, the use of automation to advance the world’s electrification journey supports its alignment of its portfolio to the automation and energy transition megatrends. The company said that as a key player in the global energy transition, it is “applying its complete portfolio in industrial automation, cyber secure IoT (Internet of Things), material handling, building automation, and safety solutions to help battery manufacturers bring reliable products to the market as quickly as possible to meet the projected demand for battery cells.”