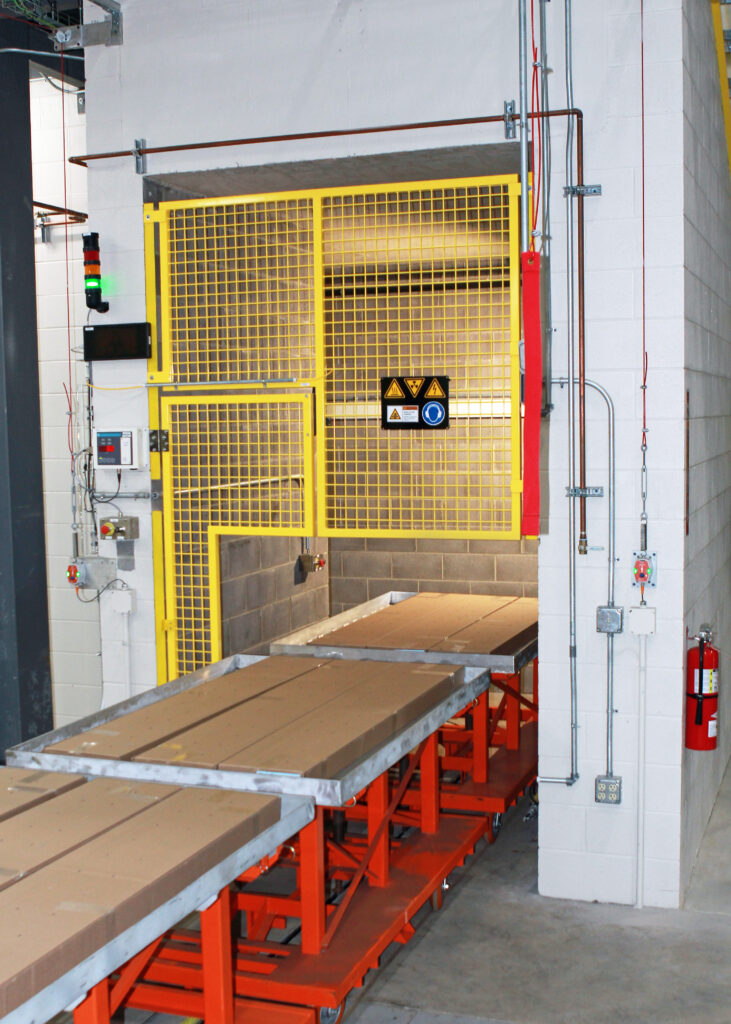
A product enters the electron beam accelerator at Mercury Plastics. (Photo: Business Wire)
A new 10 MeV electron beam accelerator at Mercury Plastics is said to provide increased power and excellent dose uniformity for processing tubing, wire and cable, and rubber products, among others.
MIDDLEFIELD, Ohio—Thermoplastic parts manufacturer Mercury Plastics has long enhanced its customers’ products with the use of electron beam technology. Since 1999, the company has employed a 5 MeV electron beam accelerator to improve long-term part performance in areas like chemical, stress-cracking, and kink resistance; abrasion and wear resistance, and increased temperature capability.
Now, thanks to a $15 million expansion of its facility in northeast Ohio, Mercury Plastics is expanding its electron beam processing capabilities. The company recently added a 10 MeV electron beam accelerator to its operations, making it “one of only a few companies in North America with this technology,” according to a release from Mercury Plastics.
The 10 MeV unit is reported to employ proven accelerator technology, providing increased power and delivering excellent dose uniformity. Mercury undertook a nearly 21,000-square foot expansion to its current facility to make way for the new capability, the company said in the release.
“Mercury Plastics has been on the leading edge of utilizing this type of niche technology in the manufacture of thermoplastic products for decades,” said Jay Burnett, president of Mercury Plastics, in the release. “Investment in a new electron beam accelerator demonstrates our commitment to supporting the long-term growth strategies of our current customers, and it also expands our capacity and ability to bring this unique technology to newer markets.”
A wide range of products are reported to benefit from electron beam processing. Among them are tubing, wire and cable, and molded components for electrical and electronic applications. Other products that benefit include heat shrink film and tubing, heat trace cable, gaskets and foam, rubber products, and sheet film, the company said.
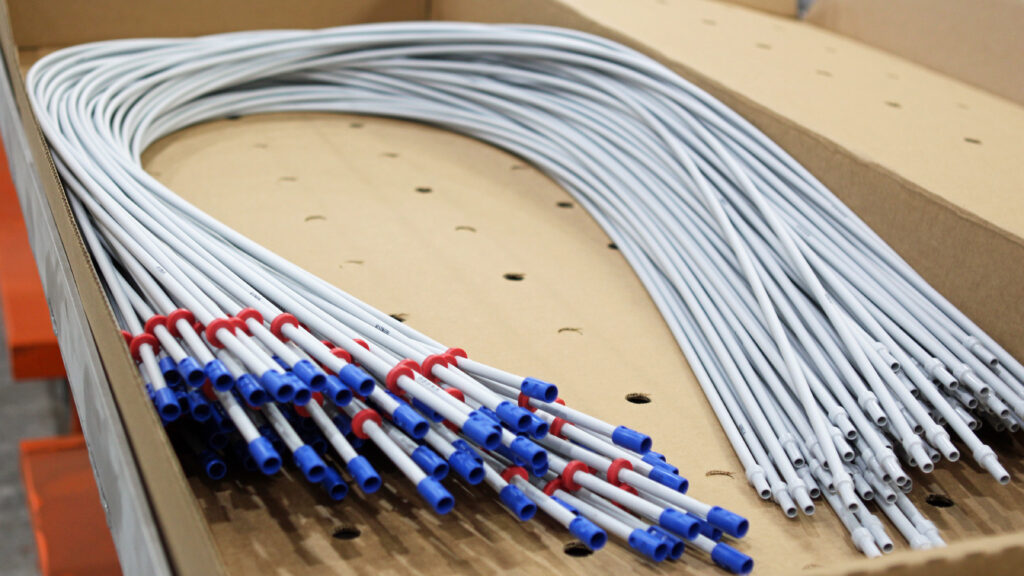
A “beamed” product that has undergone electron beam processing. (Photo: Business Wire)
“The use or electron beam cross-linking eliminates the need for chemical additives in the cross-linking process,” the company’s website stated. “Since there are no chemical additives used, there are no chemical residuals remaining on the cross-linked product, ultimately providing a clean, safe, and environmentally friendly approach to cross-linking.”
Mercury Plastics, a subsidiary of Masco Corporation, prides itself on its unique approaches to providing custom thermoplastic products for numerous markets. The company provides extrusion, injection over-molding, cross-linking, and fabrication operations at its three manufacturing facilities in Middlefield, about 30 miles east of Cleveland. Its customers are reported to include companies in the appliance, automotive, construction, electrical, faucet, and liquid dispensing markets, as well as the marine, medical, off-shore oil exploration, and plumbing markets.
“Our core competencies include custom profile extrusion, extrusion of tubing, injection over-molding, our patented Air-Core® blow molding technology, electron beam processing, and fabrication, such as forming and assembly,” the company said in the release. “We process a variety of materials, including polyethylene, PEX, rigid and flexible PVC, nylon, ABS, polypropylene, thermoplastic elastomers, and polysulfone.”