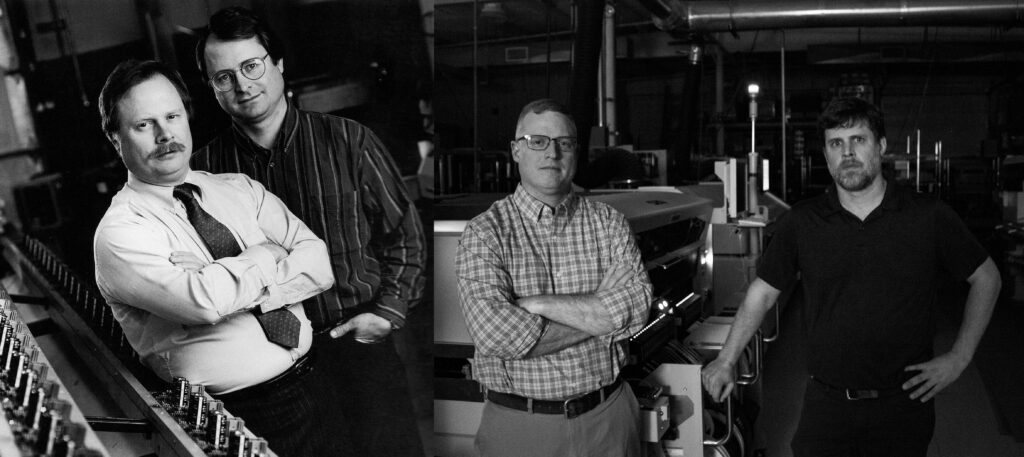
Two generations in electronics design and manufacturing at Divelbiss Corporation. Left: Terry and Alan Divelbiss, in the 1990s. Right: Don and David Divelbiss in 2022. (Image courtesy Divelbiss Corporation)
Divelbiss Corporation has developed a patented PLC on a Chip™ technology that could help open new markets for single-chip programmable logic controllers.
By Mark Shortt
Divelbiss Corporation has been manufacturing custom electronics and industrial electronic control products since it began in 1974. Fifty years after its founding, the company employs 32 at its 17,000-square-foot production facility in Fredericktown, Ohio, where it designs and manufactures printed circuit board (PCB) assemblies, box builds, control panels, custom programmable logic controllers (PLCs), and electromechanical assemblies for OEMs in numerous industries.
Vice President of Engineering Don Divelbiss describes the company’s customer base as “very diverse,” spanning markets from industrial to consumer products and electronic contract manufacturing. The company also supports customers in the mobile equipment, construction and mining, oil and gas, fluid handling, and agriculture industries, as well as manufacturers of HAZLOC products—devices that are designed to be used safely in hazardous locations.
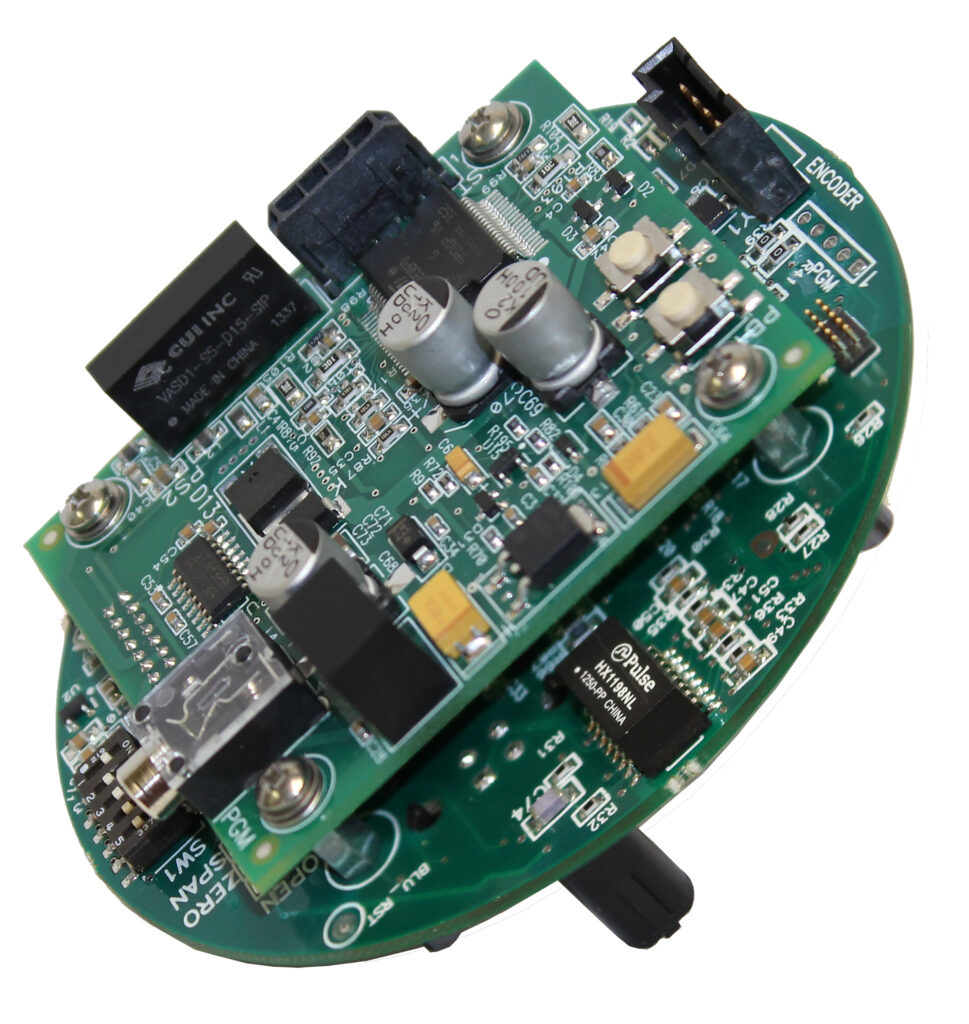
Divelbiss provides custom electronics product engineering to OEMs’ requirements, from specification development through printed circuit board layout to final product manufacturing. (Image courtesy Divelbiss Corporation)
“Applications vary from customer to customer, but generally, the assemblies we produce are used in industrial, heavy equipment, test and measurement, HAZLOC, military, and consumer products,” Divelbiss said in an emailed response to Design-2-Part.
As a contract manufacturer, Divelbiss offers full surface mount technology (SMT) assembly capabilities for parts as small as 0201 (0.020 inch x 0.010 inch), as well as ball grid arrays (BGAs) and other fine-pitch components. The company provides product calibrations to NIST calibrated standards where specified by its customers. Divelbiss also offers selective solder, automated conformal coating, automated optical inspection (AOI), potting and encapsulation, and testing. Assemblies are serialized and can be tracked through assembly, test, and shipment.
“Our biggest strength is that we are nimble and have a broad background in many industries that gives us a large knowledge base to draw from,” Divelbiss said. “With our in-house engineering team, we can work with customers to solve supply chain problems rapidly.”
Deep Bench of Engineering Talent
The company’s ability to work with customers in this way includes the development of new products, where its team of 10 engineers is essential in taking product concepts all the way through to production in an expeditious manner. Divelbiss can also guide products through agency certifications and compliance testing.
“We support many OEMs by taking products from initial concept through specification, development, qualification testing, agency certifications, and into production in low-to-mid volumes,” Divelbiss explained, adding that production volumes could range from about 100 to 50,000.
For many manufacturers today, the ability to deftly navigate supply chains is crucial to their success. Divelbiss said the company’s purchasing staff are industry veterans who source parts from global suppliers and are experts in managing materials to meet production goals. “Our MRP system allows us to push and pull parts deliveries to meet customer requirements,” he added.
The company’s deep bench of engineering talent gives Divelbiss the technical experience and flexibility to produce standard (stock) and custom products for its customers, depending on their needs. Although Divelbiss has supplied off-the-shelf programmable logic controllers (PLCs) under its own brand for decades, it has also developed “client-specific products from simple relay panels to a complex SCADA (supervisory control and data acquisition) system for test and monitoring of the emergency warning network surrounding nuclear power facilities,” according to the company’s website.
“We here at Divelbiss welcome the opportunity to work with your engineering [team] to arrive at the best solution when off-the-shelf just doesn’t fit,” the website stated. “Our extensive body of technical knowledge, attention to detail, and our commitment to quality has caused many of our OEM clients to utilize our staff as an extension of their own.”
Customers also benefit from the Divelbiss team’s knowledge of design for manufacturability (DFM), an engineering practice that can simplify a manufacturing operation and reduce its costs. Divelbiss provides its customers with designs that are optimized for their production goals.
“We understand that the requirements are different for a 100-piece production run versus a 10,000-piece run, and we will optimize the design for the anticipated production volume to provide our customers with the best value possible,” said the company’s vice president of engineering. “This also includes ensuring that the design is optimized for compatibility with PCB assembly processes and [optimized] to minimize setup and run time through intelligent design.”
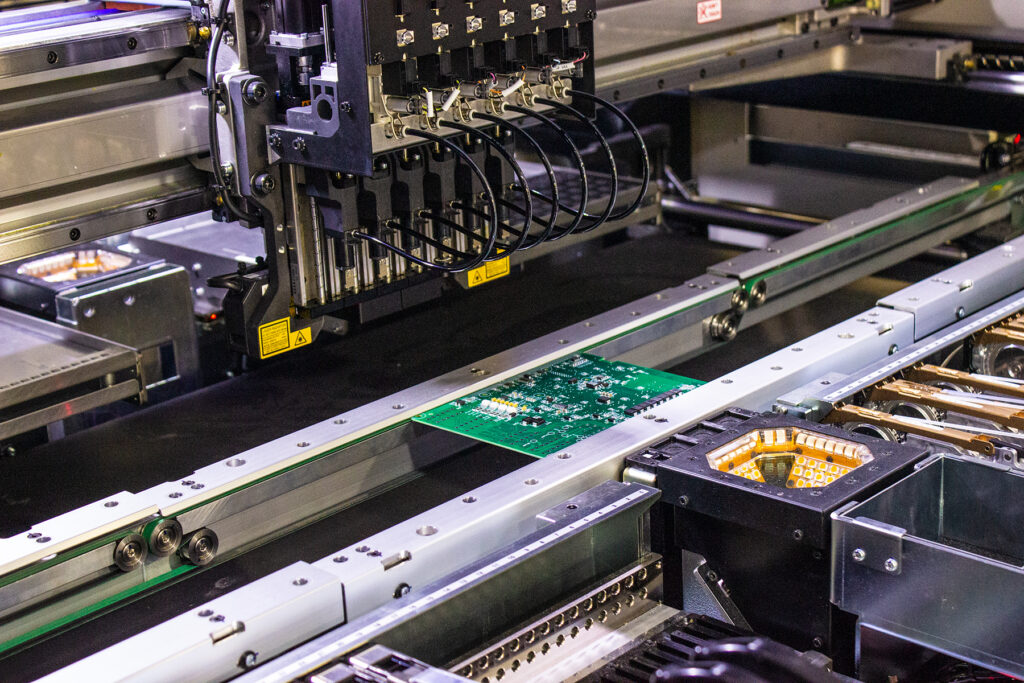
Placing surface mount technology (SMT) components (as small as 0201 & micro BGA) on a printed circuit board, using automated pick-and-place technology. (Image courtesy Divelbiss Corporation)
A Commitment to Quality and Customer Service
The manufacturer’s quality management system is certified to ISO 9001:2015 with Design, a certification that applies to the design and manufacture of industrial electronic controls, according to the company’s certificate of approval.
“Many of our team members have been with us for 10-to-20 years, and it shows in our quality,” Divelbiss said. He explained that Divelbiss Corporation is a “relationship company” that focuses on supporting its customers for the long run. From a manufacturing perspective, that means maintaining an intense commitment to quality and customer service.
“We strive to provide our customers with the best solutions to meet their quality, lead-time, and pricing needs. We have customers that have been with us for 20, 30, and even 40 years. One of our original customers from 1974—50 years ago!—is still with us and just started a new product development program in 2024.”
All of the company’s assemblies are built to the IPC-A-610 Standard for Acceptability of Electronic Assemblies. The standard was developed by the IPC, a global association of member companies that provides industry standards and intelligence, training, and public policy advocacy for OEMs, electronics manufacturing services (EMS) providers, PCB manufacturers, and suppliers throughout the electronics industry supply chain.
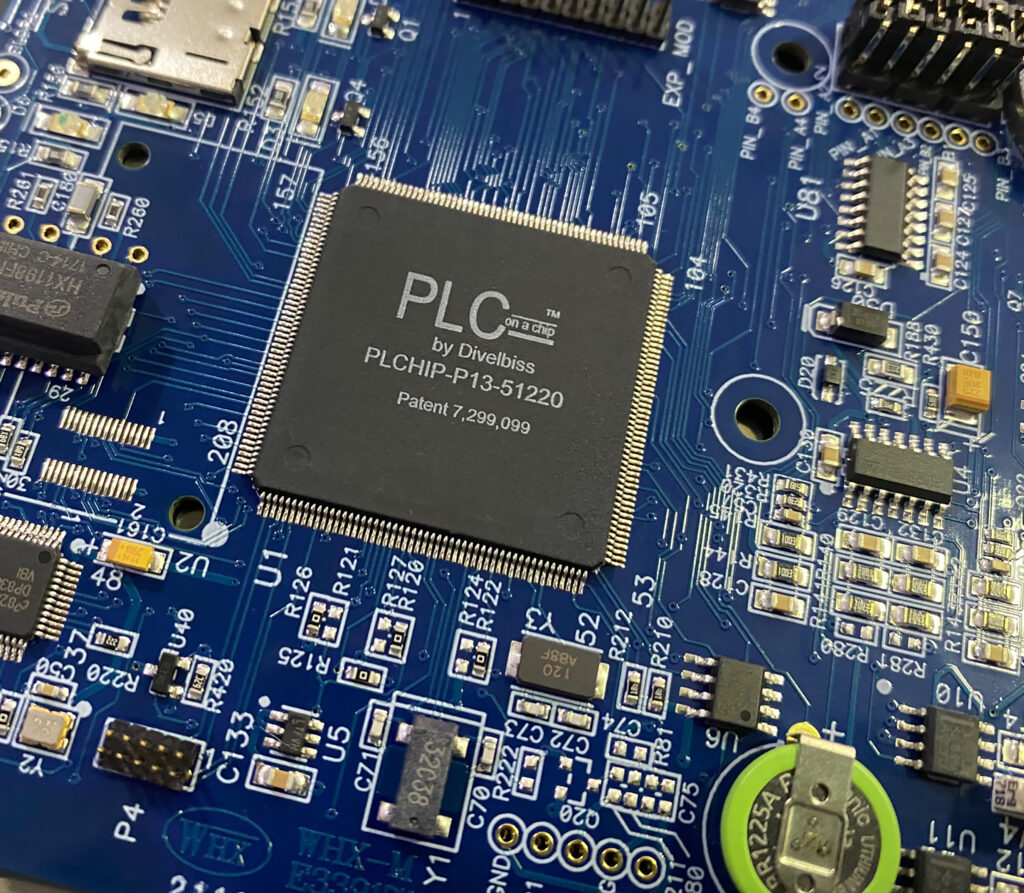
A custom printed circuit board design features Divelbiss’s patented PLC on a Chip™ technology. The technology allows for quick design and programming, with no low-level coding required. (Image courtesy Divelbiss Corporation)
The company “100 percent inspects” its products, Don Divelbiss said. “This is typically done with automated optical inspection (AOI), checking each PCB for part placement, part markings, rotation, and solder joint integrity. Where applicable, additional inspection techniques and technologies are used.” Divelbiss also performs routine production testing when specified by its customers. If needed, the company can assist customers with the development of production test fixtures.
Divelbiss Corporation retooled its entire production facility in 2020, adding new Yamaha SMT assembly equipment, RPS selective soldering, and board washing equipment. Two years later, the company rolled out new enterprise resource planning (ERP) software that touches all aspects of business, including material requirements planning (MRP), and is said to have greatly improved Divelbiss’s operational efficiency. This year, the company has already added a new fully automated conformal coating line.
The broad capabilities of its engineering team enable Divelbiss to provide a wide array of engineering services, including embedded hardware design, embedded software design, mobile app design and development, and cloud software integration. The team’s expertise also extends to various industrial network protocols; HAZLOC product design to meet intrinsic safety (IS), non-incendive, and explosion-proof requirements; environmental testing in its in-house lab; and custom PLCs.
“With a 50-year history of electronic design work, we have extensive circuit libraries to draw from,” Divelbiss said.
New Possibilities for Single-Chip PLCs
But Divelbiss is by no means resting on its laurels. In 2004, the company introduced its patented PLC on a Chip™ technology for embedded control. In a white paper published on the company’s website, “What Can an Embedded PLC Do for Your Controls Solution?” Don Divelbiss discusses some of the potential benefits of—and new possibilities for—single-chip PLCs, including the Divelbiss PLC on a Chip.
He described single-chip PLCs as “essentially programmable embedded controllers realized on an integrated circuit (IC)” that can be used in “markets previously not associated with PLCs,” such as “commercial appliances, special purpose printers, and motor drives.”
“There are many benefits to using an embedded PLC as part of the design of an OEM control system, as the level of flexibility brought to a design by this technology allows for custom control solutions that fit exact system requirements, lower design and system cost, simplify software support, and increase reliability,” Divelbiss wrote. “In addition, a system utilizing an embedded PLC can meet the most demanding environmental requirements and provide a scalable platform that can support future product features.”
Divelbiss went on to write more about the types of applications where single-chip PLCs can fit the bill.
“Using the PLC on a Chip as a benchmark, single-chip PLCs are available with a base temperature range of -40°C to 85°C, with extended temperature variants available on a per-application basis,” he wrote. “The alternate ruggedization options of embeddable PLCs enable them to operate in applications that require high tolerance to humidity, shock, and vibration, and excessive G forces resulting from constant acceleration, making them a flexible solution for applications that range from mobile equipment to MIL-SPEC systems.”
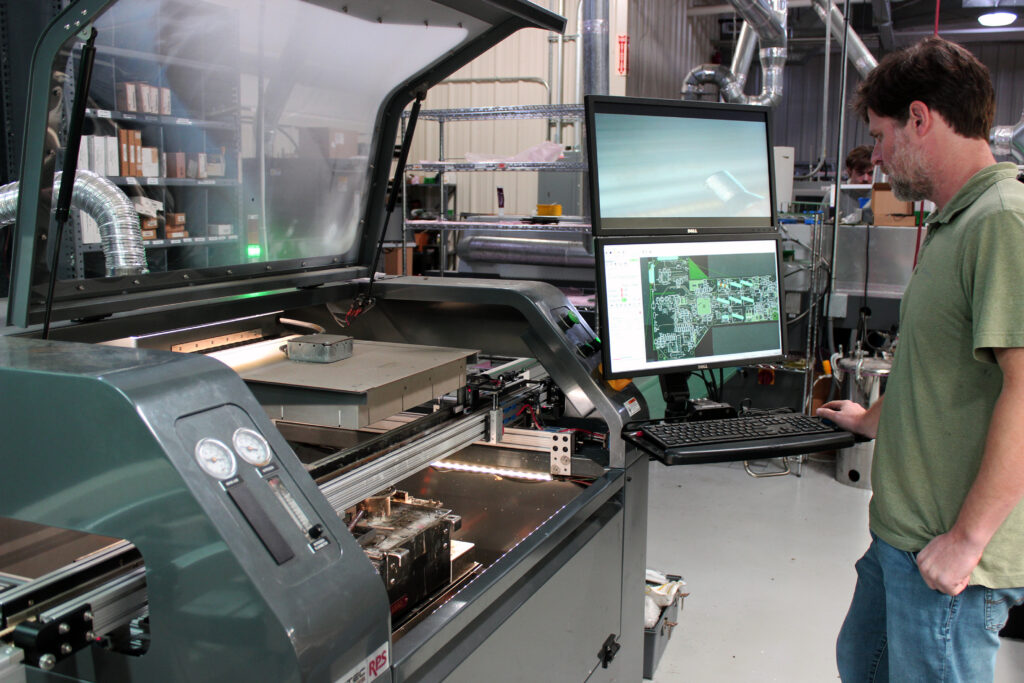
Soldering thru-hole components and connectors on a printed circuit board assembly, using a selective soldering station. (Image courtesy Divelbiss Corporation)
A Battery-Powered Monitoring Device
An example of the company’s ability to solve a technical challenge is its design and manufacture of a battery-powered monitoring device for the valve industry. In addition to incorporating a variety of technologies, the product needed to achieve HAZLOC Intrinsic Safety (IS) certification because it would be used in explosive atmospheres.
“The design of Intrinsically Safe products is not a trivial undertaking,” said Don Divelbiss. “Our team is experienced in this area and familiar with the various global standards that must be met when designing devices for HAZLOC applications.”
The device monitors the position of an enclosed valve without entering the pressure cavity—a requirement because the valve is constructed in such a way that no seals or moving parts exit the valve housing. It is also used for a wide variety of applications, including steam and corrosive gases, Divelbiss said.
The design consists of an electronic assembly in a plastic injection molded housing. One of the requirements of the project was the development of an app to run on Android and iOS devices, enabling users to access live and historical performance data.
“Divelbiss was responsible for the design of the device from the initial concept, through development, prototyping, qualification, and agency certification,” he said.
A five-year minimum battery life was required, and the device has options for 4-20mA output, Wireless HART, and ISA100 wireless connectivity. It was required to operate over a temperature range of -40°C to 80°C while meeting all of the stated requirements, according to Divelbiss.
To meet the application requirements, Divelbiss applied its skills in a variety of ways, including sensor design. The company’s engineering team developed a custom sensor that measured valve parameters while remaining outside of the valve housing. Their expertise in low power systems enabled them to design a system that met the customer’s battery life requirements. And with extensive experience in a variety of wireless and industrial protocols, Divelbiss implemented WiHART and ISA100 protocols on the device.
A mobile app was another key piece of the puzzle. The app that Divelbiss developed is used for device installation, setup, and data collection.
“Our software engineers developed a customized cross-platform app that connects to the monitor via BLE and allows users a live view of valve parameters,” Divelbiss said. Users also employ the app for calibration and to access documentation and download historical data, he added.
Testing for environmental performance was also critical. Divelbiss used its in-house environmental lab to perform qualification testing of the design, sensor validation, and battery characterization over the entire operating range of -40°C to 80°C.
Although the project posed a variety of technical challenges, the HAZLOC Intrinsic Safety requirements drove the design more than any of the other requirements, Divelbiss said.
“Balancing Intrinsic Safety requirements versus product performance, while meeting the specifications for the product, required very detailed implementation and analysis of the product design,” he explained.
Divelbiss is performing the PCB assembly and box build of the final unit.
“Since it is a HAZLOC product, quarterly surveillance audits by CSA and quality system processes are in place to ensure not only CSA compliance, but also that it meets the manufacturing quality system requirements demanded for ATEX and IECEx devices,” Divelbiss said.