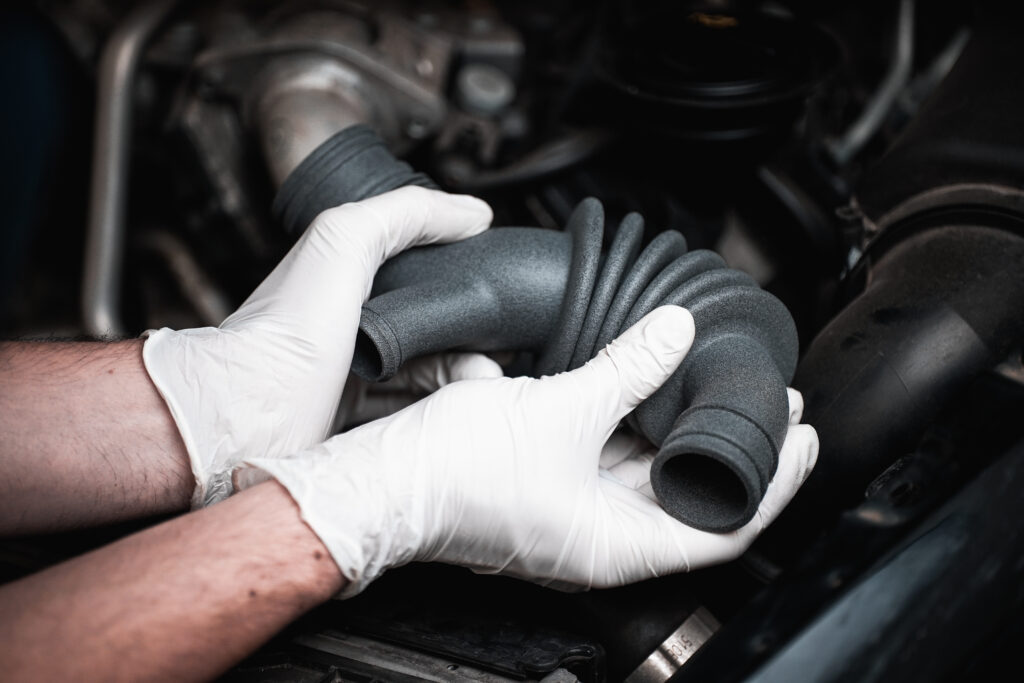
A flexible automotive component produced with SAF™ PP on the Stratasys H350™, suitable for tight and chemical resistance applications. (Photo: Business Wire)
Stratasys and BASF are partnering to deliver the new polypropylene material for Stratasys SAF Technology.
EDEN PRAIRIE, Minn. And REHOVOT, Israel—Stratasys Ltd. is set to launch a new polypropylene material for use on the Stratasys H350™ printer in the fourth quarter of 2024, the company said in a release.
The new material, Stratasys SAF™ Polypropylene (PP), is offered in partnership with BASF Forward AM to provide greater cost efficiency and superior part quality in Powder Bed Fusion technologies. According to Stratasys, the material “offers a lower cost per part and exceptional surface aesthetics” versus existing materials. It is said to be designed to meet the rigorous demands of high-volume production while maintaining exceptional overall quality, the company said in the release.
“With superior nesting ability and a total turnaround time of less than 36 hours, SAF PP allows customers to produce hundreds of parts in a single build,” said Stratasys Vice President of Additive Manufacturing Technology Neil Hopkinson, in the release. “This boosts productivity and cost efficiency, delivering high-quality parts at a lower cost.”
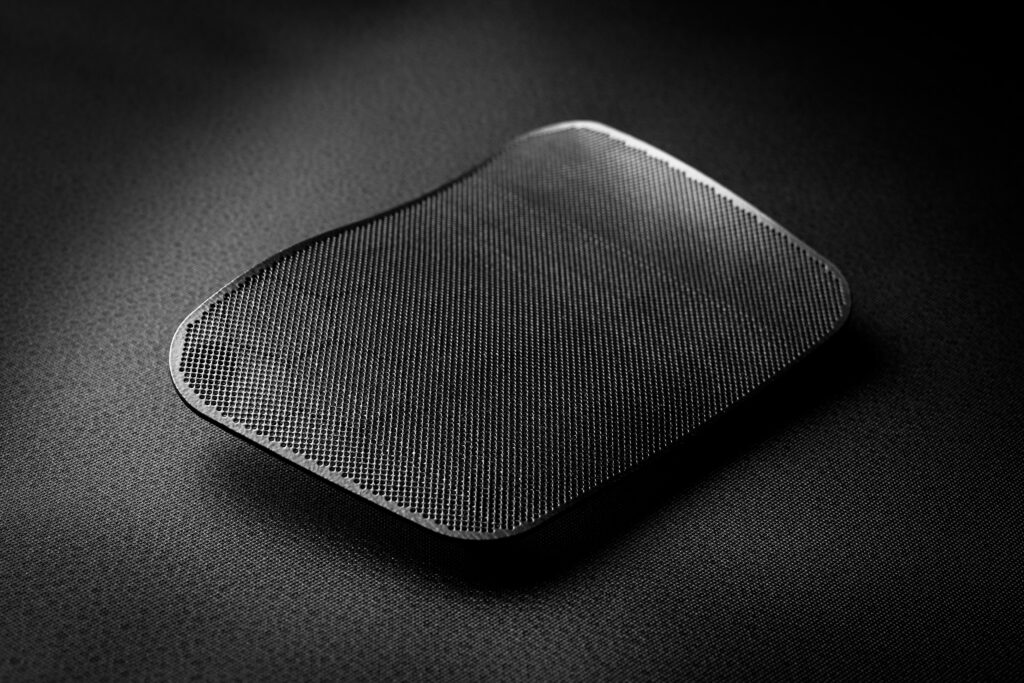
An automotive speaker grill printed with SAF™ PP on a Stratasys H350™ printer and finished with the VaporFuse Surfacing process using the Powerfuse S PP machine from DyeMansion. (Photo: Business Wire)
Stratasys SAF PP is engineered for a wide range of applications in diverse markets, including automotive, medical, consumer sports, and industrial sectors. The polypropylene material is reported to provide durability, chemical resistance, and flexibility for automotive components, such as housings and ducting, as well as orthotic devices and consumer sports gear, including shin guards. Its lightweight nature, and water and air tightness, make it suitable for producing intricate, high-quality parts across various applications, the company said.
“We are pleased to collaborate with Stratasys on the development of this new polypropylene material, optimized for their SAF 3D printing technology,” said BASF Forward AM CEO Martin Back, in the release. “This partnership underscores our commitment to providing robust AM solutions tailored to the needs of industrial manufacturers. Together, we aim to broaden the adoption of AM technologies to make our customers more successful.”
The new material has also reportedly demonstrated the capability to produce “robust, defect-free parts with complex geometries, such as flexible tight pipes and intricate sensor mounts,” according to the release.
“The surface finish of SAF™ PP parts is unparalleled,” said Philipp Götz, CEO of Götz Maschinenbau GmbH & Co. KG, a beta customer of the material, in the release. “The fine detail resolution and uniform appearance are far superior to any other PBF printed PP we have seen, significantly enhancing the visual appeal of our final products.”
“The consistent quality of SAF™ PP is exceptional,” said Sun Digital Application Engineer Jennifer Govea, in the release. “Its airtight and watertight properties ensure reliable performance across various applications. With SAF PP, we can now bring a wide array of additive manufacturing benefits to unlimited applications that use PP today in traditional manufacturing.”