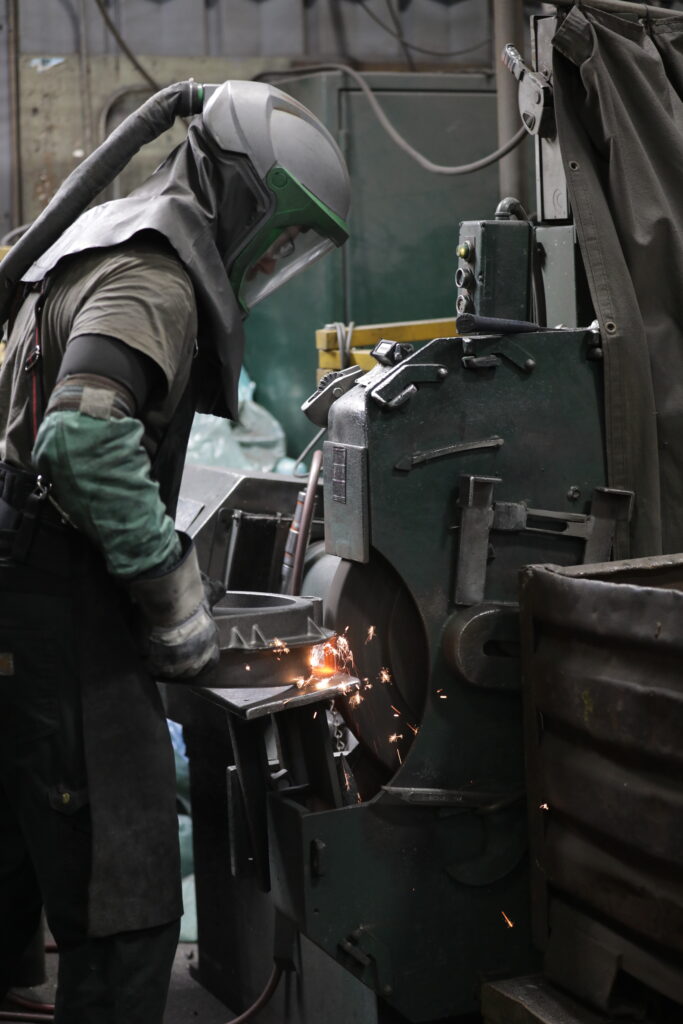
A Baker Casting team member grinds a cast part the company’s Evansville, Wis., facility. (Photo courtesy Baker Casting Division, Baker Manufacturing Company, LLC)
Offering a foundry, machine shop, and finishing capabilities, the custom iron casting specialist provides sole sourcing for machined castings.
By Mark Shortt
EVANSVILLE, Wis.—Baker Casting, a division of Baker Manufacturing Company, LLC, produces a variety of custom gray, ductile, and austempered ductile iron castings for OEMs and machine shops, based on its customers’ drawings. Along with handling castings up to 150 pounds, Baker Casting has multi-core capability, said Jennifer Willger, director of sales at Baker Casting Division, in an emailed response to Design-2-Part.
Baker uses a range of manufacturing processes to meet specific application needs. All of the items it produces are cast in the company’s foundry, then subjected to blasting, grinding, and brinelling.
“Our foundry, machine shop, and finishing capabilities enable us to offer sole sourcing for machined castings. We prioritize quality/process control, metallurgical capabilities, and timely delivery, which are highly valued by our customers,” Willger said.
Examples of castings produced by Baker include ductile iron bell crank castings for agricultural sprayer equipment; ductile iron rear axle castings used in commercial-grade turf care equipment; and gray iron gear train housings used in dozer equipment to withstand heavy-duty operations.
Baker also manufactures gray iron elbow castings that play a crucial role in industrial diesel engines; gray iron volute castings used in centrifugal pumps; and ductile iron link castings that are used in conveyors to support material handling processes.
“Our commitment to quality casting and finishing ensures that these parts meet the rigorous demands of their respective applications, providing reliability, durability, and performance to our customers across diverse industries,” Willger said.
Baker Casting is one of three divisions of Baker Manufacturing, an Evansville-based company founded in 1873 that prides itself on providing comprehensive design, engineering, and manufacturing services to support numerous industries. Baker Water Systems produces “water well accessories and filtration products for residential use; pitless units and booster stations for municipal and industrial use; and well monitoring products for environmental use.” Haight Pump focuses on designing and manufacturing “gear pumps and positive displacement pumps for the OEM and process market,” according to Baker Manufacturing’s LinkedIn page.
As a supplier and partner to OEMs and product manufacturers, Baker maintains an unwavering commitment to quality, efficiency, and reliability. That commitment, Willger said, is the company’s greatest strength and the reason why customers consistently choose its parts and services.
Baker Casting’s dedication to quality workmanship is backed by extensive metallurgical capabilities and stringent process control, ensuring that each component meets the highest standards. Its commitment to quality—also evident in its ISO 9001:205 certification and ITAR registration—is said to guarantee superior performance and enhance the longevity and reliability of the parts it produces, ultimately providing value to its customers.
Baker’s focus on providing timely delivery is also paramount, Willger said.
“We understand the importance of meeting deadlines and strive to ensure that our customers receive their orders promptly and efficiently. This reliability in delivery schedules instills confidence and trust among our clients, making us their preferred choice time and time again,” she explained.
Baker Casting’s comprehensive suite of services is specifically designed to meet the diverse needs of design engineers, manufacturing engineers, and purchasers. The company’s on-site machining capabilities include expert fixture design and fabrication, to support customers’ projects from conception to completion. Baker also offers on-site application of non-VOC water-based primers, paints, and rust preventatives.
The company’s versatility in handling order quantities, ranging from service-level quantities to medium-scale production runs, underscores Baker’s adaptability to meet the diverse needs of its customers. “Whether it’s a small batch or a higher-volume order, we have the capabilities and expertise to deliver,” Willger said.
Baker facilitates the transfer of customers’ existing patterns to its molding centers, thereby saving time and money for its customers. This process demonstrates Baker’s commitment to cost-effectiveness and efficiency, further reinforcing its position as a trusted partner in their supply chain, Willger noted.
“Our in-house Pattern Shop can seamlessly integrate your existing tooling with our equipment and processes, offering rigging, gating, and adaptation services. For projects requiring significant modifications or brand-new tooling, we leverage our longstanding relationships with trusted pattern companies to meet your needs.”
By maintaining relationships with various trusted partners, Baker offers a range of additional services that include heat treatment, powder coating, plating, e-coating, and galvanizing.
“Our versatility in handling order quantities, ranging from service-level quantities to medium-scale production runs, underscores our adaptability to meet the diverse needs of our customers. Whether it’s a small batch or a higher-volume order, we have the capabilities and expertise to deliver,” Willger said.
Baker recently introduced three new systems that are creating positive impacts in areas like quality, safety, efficiency, and productivity. One is a robotic grinding cell that combines the precision and consistency of robotic automation with advanced grinding technologies. Described as particularly beneficial for handling complex geometries and repetitive tasks, the robotic grinding cell provides improved surface finishes, consistent quality across batches, and increased safety by reducing human exposure to hazardous grinding environments, Willger said.
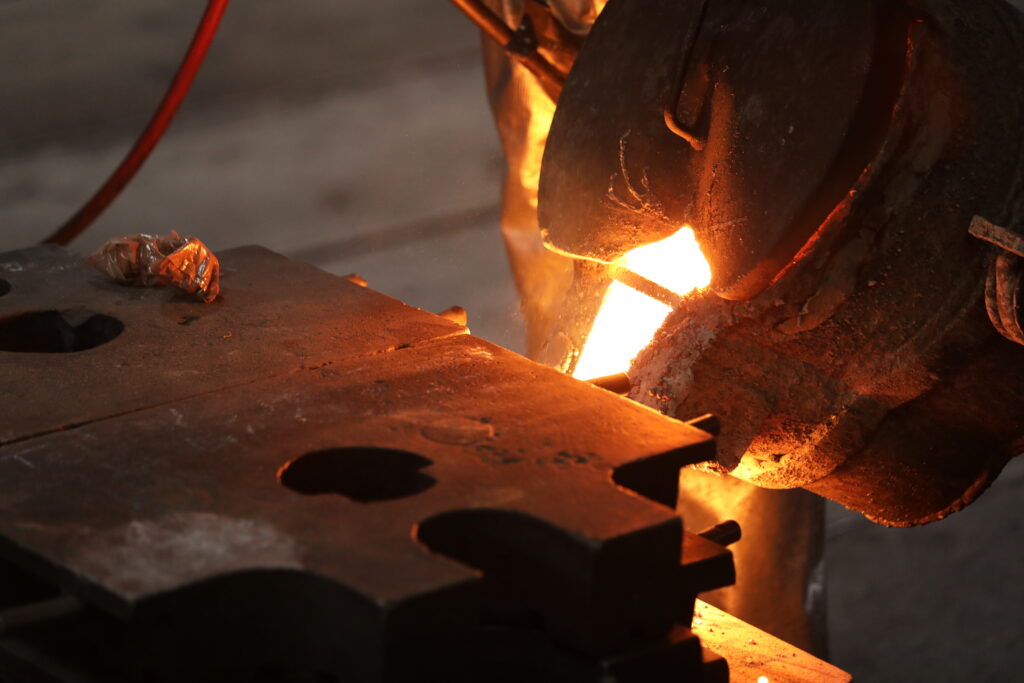
Filling a mold at Baker Casting. (Photo courtesy Baker Casting Division, Baker Manufacturing Company, LLC)
Another is a Mazak Robotic Machining Cell, said to offer exceptional flexibility for unmanned operation over extended periods. Integrating this cell into Baker’s operations has led to significant improvements in productivity, consistent part quality, and reduced cycle times. Willger said the automation enables adaptive machining capabilities. “The machine can adjust operations in real-time for optimal performance,” she noted.
Baker also added a Mazak Palletech Machining System, which integrates machining centers with an automated pallet transfer and storage system. Designed to maximize machine use, the system offers the ability to run a diverse range of parts in unattended operations, significantly increasing throughput. It is said to provide flexibility in production planning and scheduling, reduce setup times, and allow for just-in-time manufacturing processes.
Willger said that Baker excels at addressing technical challenges with innovative solutions—a claim backed by the company’s track record of resolving issues for customers who faced difficulties with parts produced at other foundries. She noted two examples: improving the soundness of cast parts. and enhancing the machinability of thinner walled castings.
To enhance part soundness, Baker’s solution leverages the strategic use of risers and/or chills to mitigate issues related to internal porosity and structural integrity. “This approach ensures that the final castings meet the quality standards required by our clients, illustrating our adeptness in applying foundry science to solve real-world problems,” she said.
Maintaining dimensional accuracy and surface finish can be particularly challenging when machining thinner walled castings. Willger explained that by carefully selecting the best alloys and inoculants, Baker can optimize the castings’ machinability.
“This process is supported by a rigorous analysis conducted by our senior metallurgist and foundry quality technician, ensuring that the chosen materials facilitate easier machining and also adhere to the performance requirements of the application.”
Willger added that the solutions are possible through the collaborative efforts of Baker’s team, including its senior metallurgist, foundry quality technician, quality CMM technician, technical sales manager, and foundry supervisors. She also noted that Baker Casting Senior Metallurgical Engineer Julia Scruton was recently honored with the 2024 Outstanding New Committee Member Award by the American Foundry Society (AFS).