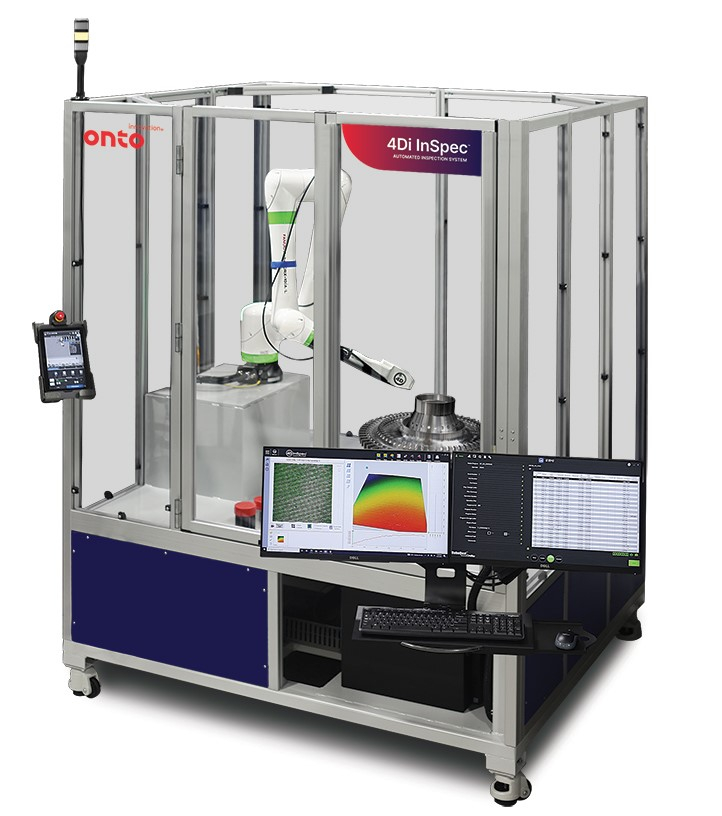
Onto Innovation’s 4Di InSpec automated metrology system uses patented, vibration-immune technology to provide automated surface defect and feature metrology for aviation, aerospace and other applications in the industrial manufacturing market. (Photo: Business Wire)
Onto Innovation’s technology uses non-contact, 3D optical metrology on the production floor to provide what the company calls “new levels of defect inspection with micrometer-level resolution.”
WILMINGTON, Mass.—Amid an ongoing worker shortage, the aviation industry’s focus on safety is driving a renewed emphasis on greater quality control and optimization of labor. A technology that shows promise in achieving these aims is a new automated metrology system from Onto Innovation Inc. and its Tucson, Arizona subsidiary, 4D Technology.
The 4Di InSpec automated metrology system (AMS) uses patented, vibration-immune technology to provide automated surface defect and feature metrology for aviation, aerospace and other applications in the industrial manufacturing market. It enables use of non-contact, three-dimensional (3D) optical metrology on the production floor, providing “new levels of defect inspection with micrometer-level resolution,” according to a release from Onto Innovation.
Onto Innovation and 4D Technology were recently named the winner of FANUC America’s 2024 Innovative System of the Year award for their efforts in developing the technology.
“We are honored to be recognized as an innovator by a robotic industry leader like FANUC America,” said Erik Novak, vice president and general manager of Onto Innovation subsidiary 4D Technology, in the release. “The combination of FANUC robotics with 4Di non-contact sensor technologies provides a unique platform for improving throughput, quality, and delivery times in industrial manufacturing.”
According to the release, visual inspection remains the standard quality control practice for inspection of engines in the aviation industry. This includes time-consuming and subjective repro-rubber and shadowgraph off-line techniques. However, Onto Innovation said the industry can use the 4Di InSpec automated metrology system to achieve significantly higher sampling rates and improved quality control while providing fast, accurate, and reproducible results.
The task of completing 400 typical engine call-out measurements can take weeks using traditional methods. According to Onto Innovation, the 4Di InSpec automated metrology system is capable of accomplishing the task in under 30 minutes, enabling manufacturers to reallocate labor for other critical tasks. The technology has also reportedly demonstrated the ability to reduce scrap and rework by up to 40 percent on engine components.
The 4Di InSpec AMS can be configured for multiple applications, including large, rotary applications, small freeform components such as turbine blades, and multi-sensor applications. Bob Wasilesky, senior director of sales and marketing for Onto Innovation subsidiary 4D Technology, said, “Multi-sensor, automated systems are the next step to delivering increased value to our customers, where one robot, with dual sensors, can measure surface roughness, surface features, and defect inspection all in one system, greatly increasing efficiencies.”
Onto Innovations said that in partnership with OptiPro Systems, it delivered the 4Di InSpec AMS systems to several leading aerospace engine manufacturers in the second half of 2023.
“We look forward to the continued expansion of our automation metrology portfolio to help our customers solve some of the more complex industrial manufacturing challenges in the industry,” Novak added.