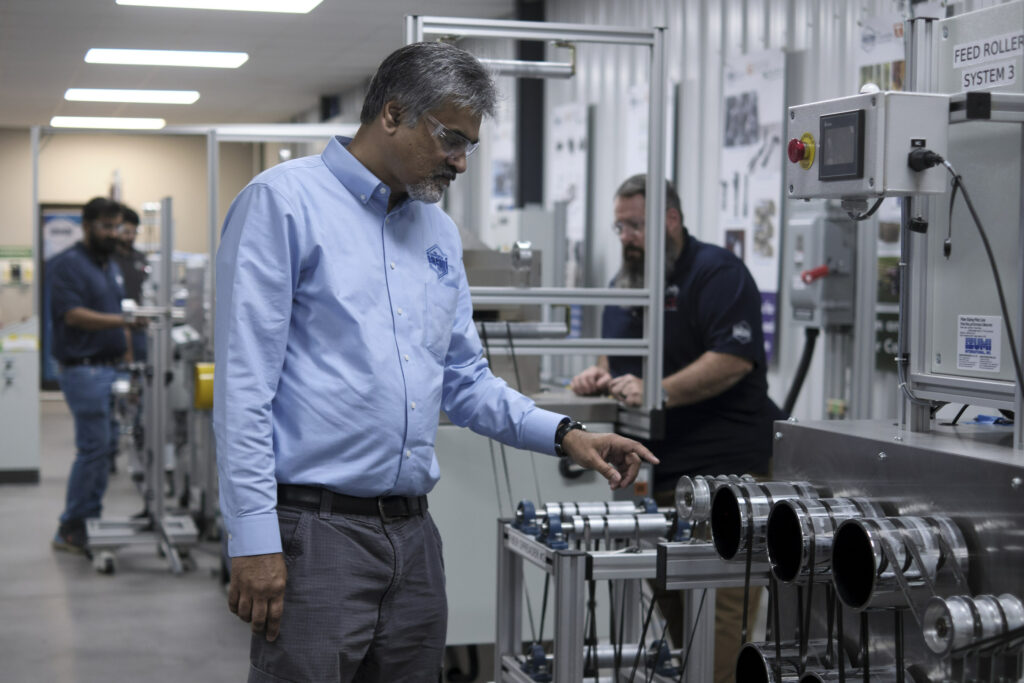
The new Michelman fiber sizing line helps provide a faster path from research to commercialization for IACMI members, according to IACMI’s Chief Technology Officer Uday Vaidya, Ph.D. (Image courtesy IACMI-The Composites Institute/PRNewswire)
A new Michelman fiber sizing line is operational at the IACMI Collaboration Facility in Knoxville.
KNOXVILLE, Tenn.—IACMI – The Composites Institute, in partnership with advanced materials manufacturer Michelman, recently added new equipment that could help IACMI members achieve a faster path to commercialization of innovative composite materials for parts manufacturing. The Michelman fiber sizing line was installed at the IACMI Collaboration Facility in Knoxville, according to a release from IACMI.
The 70-foot, modular system is designed to apply a variety of thin chemical coatings—known as fiber sizings—to fibers during composite manufacturing processes. Applying these coatings provides multiple benefits and is considered an essential step in making composites lighter, stronger, and more versatile, IACMI said in the release.
“I am both grateful and excited to have this line commissioned to benefit multiple stakeholders in the composites ecosystem we’ve built between IACMI, ORNL, UT, and industry,” said IACMI Chief Technology Officer Uday Vaidya, Ph.D., in the release. Vaidya serves as the University of Tennessee–Oak Ridge National Laboratory (UT-ORNL) Governor’s Chair in Advanced Composites Manufacturing.
“We’re not only researching and developing sustainable composites innovations. With the Michelman line, stakeholders can customize their constituent materials for a tailored fiber-matrix interface, which is key to the properties / performance of the composite,” he added.
Ohio-based Michelman manufactures chemicals for agricultural and architectural coatings, digital printing, and packaging, in addition to manufacturing advanced composites for the automotive and aerospace markets. The company’s equipment enables hands-on training for next-generation engineers and is the culmination of many years of collaboration with IACMI, the release said.
“As a leading global supplier of sizing and surface treatments, Michelman is proud to support this collaboration between industry, government, and academia,” said Michelman Director of Global Marketing Steve Bassetti, in the release. “With our purpose of Innovating a Sustainable Future, we are eager to invest in the success of the future workforce. By enabling students to apply classroom knowledge to real world applications, we hope to accelerate students’ learning curves and fuel their passion to join the workforce within the composites industry. Who knows, perhaps some of these students will lead the way in developing the next generation of sustainable composites!”
A fiber sizing is a thin coating of a custom chemical formulation, applied to the fiber to serve several functions. Benefits of sizings include protecting fibers from breaking during manufacturing. They also include tailoring the properties of the surface to maximize interfacial properties between the fiber and the polymer matrix, while also allowing the fiber format to be used or consumed in the multiple types of composite manufacturing processes, according to the release.
Initial work is underway to develop sizings for standard and wide-tow carbon fiber, but there are far more fibers and reinforcements to explore.
“For example, we’re still scratching the surface on what we can do with natural fibers like hemp, flax, and coir, to name a few,” said Vaidya. ”Sky’s the limit for innovations in sizing development.”
The Michelman sizing line was custom-built by Izumi International, Inc., a South Carolina-based manufacturer of equipment for the carbon fiber and composites industry. Its unique features are reported to include the modularity of its design, which allows it to be used for fiber feed, fiber spread measurement, fiber damage assessment, conditioning in-line ovens/heaters, tension guides, wet baths, and a range of other custom features.
One of its key benefits for stakeholders is the ability to offer high-value applications by differentiating fibers and resin offerings based on custom sizing, according to IACMI. The range of potential customers or industries that can benefit from the fiber sizing line is broad, spanning from material suppliers to OEMs, tier suppliers, parts manufacturers, and small companies. The line is also well-suited for continuous R&D in emerging chemistries, such as bio-based polymers and other feedstocks that provide more sustainable options, according to the release.
Vaidya said in the release that sizing solutions for the aerospace market have typically focused on carbon fiber that’s compatible with thermoset epoxy and polyurethane resins. Now, with more focus on sustainability and making composites more recyclable, there’s considerable interest in fiber sizing options that are compatible with thermoplastic resins. Developing options for a broader family of fibers and resins can provide custom solutions for the infrastructure, marine, wind, aerospace, defense, sporting, and healthcare sectors, he noted.