U.S. Army Selects American Manufacturer of Rotary Forged Wheel Blanks to Manufacture Aluminum Road Wheel Inserts for Abrams Tank
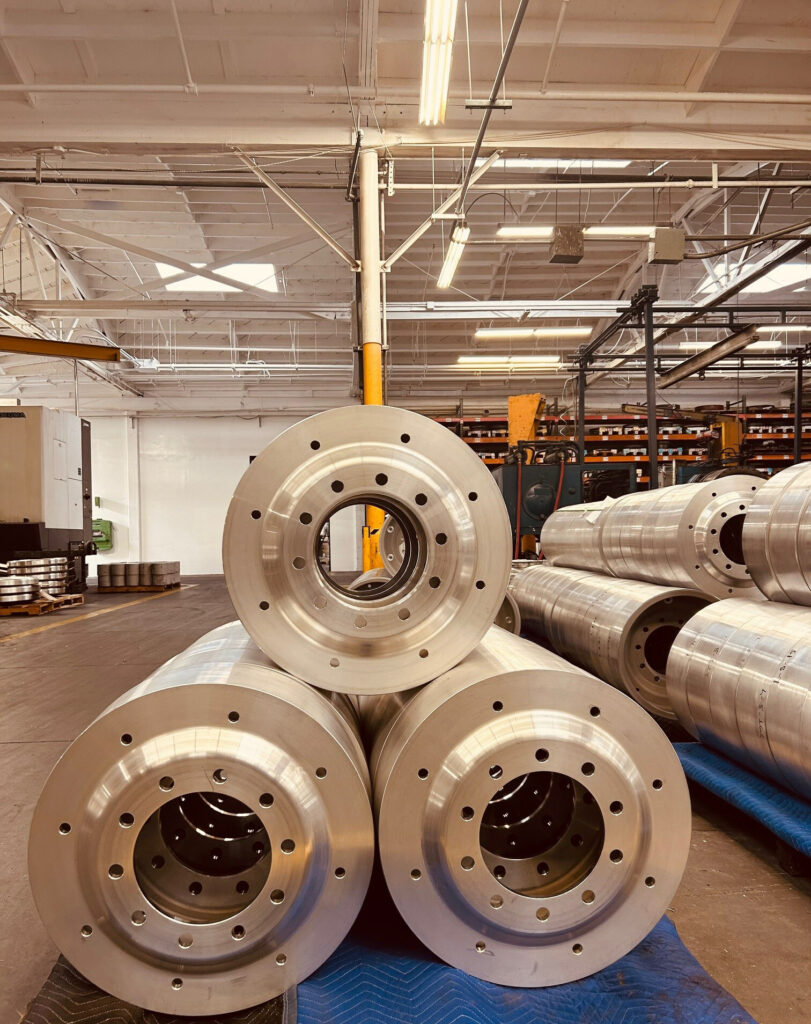
Aluminum road wheels for the M1 Abrams Tank. (Photo: AST/PRNewswire-PRWeb)
An M1 Abrams Tank wheel. (Photo: AST/PRNewswire-PRWeb)
Advanced Structural Technologies was awarded a $10 million small business set-aside contract to manufacture the inserts.
OXNARD, Calif.—In today’s modern defense landscape, military vehicles require a combination of strength, excellent mobility, and durability. A lack of these properties exposes the vehicles—and the people they protect—to high risk, according to a release from Advanced Structural Technologies, Inc. (AST).
“Often, the mechanical properties of the vehicle are the difference between life and death,” AST said in the release.
Advanced Structural Technologies, a metal forming manufacturer with more than 20 years of experience in the aerospace and defense industry, is said to be “known for its expertise in manufacturing seamless liners and cylinders for pressure vessels, and one-piece rocket engine components.” But AST also considers itself a leader in military wheel applications and forged wheels for the automotive aftermarket.
Drawing upon its 20-year legacy in heavy-duty and off-road wheel manufacturing, AST supports the military with forged wheels and “run-flat wheels” for wheeled vehicle applications. Its expertise in this area was rewarded recently by the U.S. Army, which awarded AST in May with a contract for the manufacture and supply of aluminum road wheel inserts for the M1 Abrams tank.
The company said in the release that it was awarded a firm fixed price requirements contract for the manufacture and supply of aluminum M1 Roadwheel Blanks to be delivered to the Red River Army Depot over a three-year period from fiscal year 2024 to fiscal year 2026. The small business set-aside contract has a total estimated value of more than $10 million, with “minimum and maximum order quantities and values specified for the overall contract, as well as for each delivery order and contract line item.” It has an estimated completion date of 2026.
According to the release, the M1 Abrams Tank reaches a maximum speed of approximately 68km/h, and has a cruising range up to 426 km. On the M1A1 Abrams, the torsion bar suspension comprises “seven dual road wheels on each side, with rotary shock-absorbers at the first, second, and seventh road-wheel stations.” All of this power relies on “road wheels” that are mounted on the Abrams before the tank’s track is installed.
Advanced Structural Technologies specializes in rotary forging, metal spinning, and the flow forming of materials like aluminum, copper, titanium, and other alloys into complex shapes. The company reportedly has more than 220,000 square feet of manufacturing facilities in Oxnard, including a new expansion facility. Its experience includes fulfilling a $17 million contract issued in 2019 for Abrams’ aluminum road wheel inserts for the U.S. Army Contracting Command. The company, to date, has reportedly delivered more than 40,000 M1 Abrams tank wheels for the U.S. Army.
Through Strategic Acquisitions, Fairbanks Morse Defense Is Aiming to Reshape the U.S. Shipbuilding Supply Chain
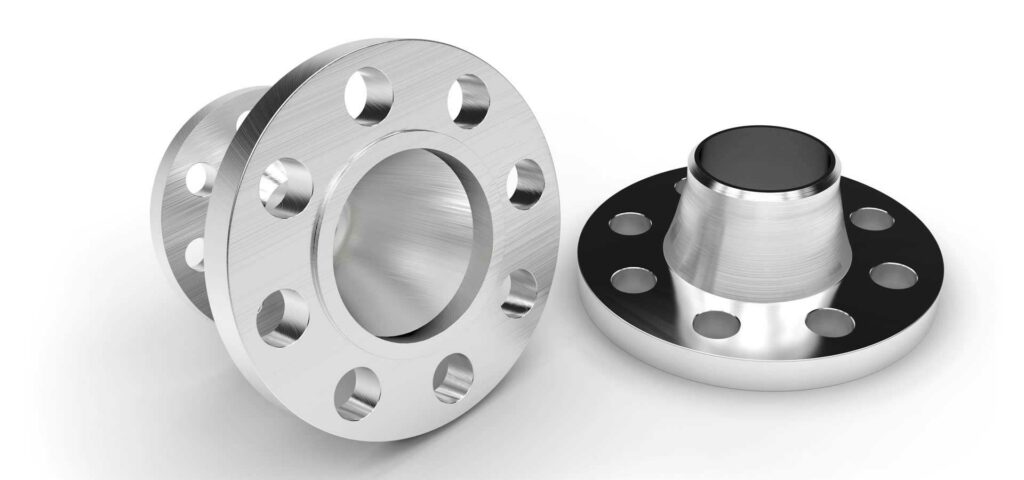
AMMCON’s capabilities include the manufacturing of fittings and assembled components from materials that include plastics, bronze, aluminum, and stainless steel. (Image courtesy FMD/AMMCON)
The company said it is taking steps to ensure unimpeded access to essential marine equipment.
BELOIT, Wis.—Supply chain challenges in recent years, from the Covid-19 pandemic to conflicts in Ukraine and the Red Sea, have brought home the realization that the United States cannot afford to be overly reliant on foreign sources for critical national defense equipment.
Fairbanks Morse Defense (FMD), the builder of trusted naval power and propulsion systems, is responding to the challenge. The defense contractor said in a release that it is “taking steps to bolster the domestic shipbuilding supply chain with acquisitions that ensure a continuous supply of critical components and equipment are available for maritime defense.”
“Revitalizing the U.S. shipbuilding industry requires us to adopt a new approach, but we can’t do that if we don’t have control over our national defense supply chain,” said Fairbanks Morse Defense CEO George Whittier, in the release. “Through our expansion and acquisitions, Fairbanks Morse Defense is taking steps to ensure unimpeded access to essential marine equipment.”
For nearly a century, the company said, Fairbanks Morse Defense has been a principal supplier of a growing array of leading marine technologies, OEM parts, and turnkey services to the U.S. Navy, U.S. Coast Guard, Military Sealift Command, and Canadian Coast Guard. Although it has been known traditionally as an engine manufacturer, Fairbanks Morse Defense has acquired 11 companies since the end of 2020. The manufacturer said it has added “domestically produced motors, valves, water filtration equipment, fans, blowers, electrical system hardware, and more to its product portfolio for U.S. maritime defense customers.”
The state of American shipbuilding
According to the manufacturer, U.S. shipbuilding has declined since the 1980s, when Federal policies supporting a robust American shipbuilding industry were abandoned. Of the six U.S. companies manufacturing large medium-speed diesel engines before 1980, Fairbanks Morse Defense is the only remaining domestic producer, the company said.
Today, China is reported to produce approximately 50 percent of the world’s commercial ships, whereas 0.5 percent are produced by companies in the United States. This production imbalance not only favors China economically but also provides a substantial reservoir of commercial vessels that could be mobilized to support a naval fleet of 350 ships, versus a U.S. fleet of about 290 vessels, according to FMD.
“Despite the superior power, capabilities, extremely well-trained sailors, and technology of U.S. vessels, the sheer numerical advantage of the Chinese fleet poses a considerable threat, potentially overwhelming adversaries,” the company said in the release.
To compete successfully with China requires a revitalization of American shipbuilding, according to FMD. Several big challenges must be met to achieve this objective, but solutions cannot be pursued without domestic control of the supply chain, the company said.
“Many voices in the industry believe that securing foreign-made parts is the only way to get their job done on time and within budget,” FMD said in the release. “In some cases, there have not been any choices. According to the Naval Supply Systems Command, 20 percent of defense sector suppliers left the industry from 2015 to 2020 due to supply chain, economic, and labor challenges, with few new U.S. companies to replace them. Many of these vendors were small-to-mid-sized companies that provided essential ‘niche’ parts or services to the military and shipbuilders that could not be procured from another domestic supplier.”
Fairbanks Morse Defense said its acquisitions of small-to-mid-sized companies, such as American Fan and Maxim Watermakers, are a few examples of how it is stepping in to preserve the domestic supply chain by ensuring that these vendors continue to provide products and services for national defense.
Reshoring American manufacturing
The defense contractor said that some larger companies, spurred by trade policies that view China as an adversary rather than a peer, are drawing their resources out of Asia and bringing them back to the United States. In some instances, companies are reshoring as a result of incentives provided by the U.S. through legislation such as the CHIPS Act. “Buy America provisions in the National Defense Authorization Act also send a demand signal to the industry that would encourage reshoring of critical military equipment,” the company said.
However, even with incentives and “Made in the USA” trade policies, reshoring of manufacturing operations can require massive infrastructure investment, according to FMD.
“Exploring the regulations around domestic manufacturing capabilities and considering tax and other incentives to support domestic onshoring as a complement to Defense Production Act grantmaking would provide much-needed financial support for these companies to bring their manufacturing back to the U.S.,” the company said.
Technology and the supply chain
Another way of controlling the domestic supply chain is by leveraging technology. One of the biggest constraints around U.S. shipbuilding is casting. As the world’s leading producer of castings, China is said to produce more than the combined total output of the next seven countries and five times more than the United States.
Through Hunt Valve, Fairbanks Morse Defense is working with the Maritime Sustainment Technology and Innovation Consortium (MSTIC) to develop what will reportedly be the first 3D-printed valve assembly to be installed in a U.S. submarine (see Defense Contractor Hunt Valve To Produce 3D Printed Valve Assembly for U.S. Submarines.)
The 70-pund valve assembly is expected to provide the U.S. Navy with “a product that meets or exceeds the quality produced through traditional sand-casting, in about two-thirds less time,” FMD said in an April release.
Additive manufacturing for submarine components has only been possible for small parts and pieces until recently. Applications for challenging alloys, such as copper-nickel, have been rare. Sand-casted copper-nickel is highly porous and often results in a high fall-out rate that challenges delivery timelines, according to FMD.
However, valve bodies created through 3D printing are reported to have drastically higher first-time yields. This ultimately accelerates the production and delivery timeframe because the manufacturer no longer needs to build in additional production time to account for the fall-out rate, the company said.
Hunt Valve’s contract with MSTIC will reportedly permit the 3D printed valve to be installed on any U.S. submarine class.
“Innovative technologies, such as additive manufacturing, are essential for building the submarine industrial base to overcome supply chain challenges,” said Andrew Pfister, vice president, aftermarket and product development at Fairbanks Morse Defense, in a statement. “By scaling additive manufacturing, we can reduce shipping from other parts of the world and increase the speed of production at home—which positively impacts the Navy’s overall strategic goal to deliver a 300+ fleet.”
Fairbanks Morse Defense said that its recent acquisition of AMMCON—a manufacturer of fittings and assembled components for marine customers—provides it with the infrastructure needed for the fittings that will be used to install the 3D printed valve in a U.S. submarine. AMMCON, based in Jacksonville, Florida, provides critical fittings and other products used on the Virginia and Columbia Class submarine programs, as well as the Ford Class aircraft carrier program, according to an FMD release reporting the acquisition.
“Fairbanks Morse Defense is working to build fully integrated products and services that will meet every need of maritime defense, and to accomplish this, we must continue to identify cutting-edge providers who share our commitment to serving as a defense contractor of the first rank,” said FMD’s Whittier, in the release. “Working together, we are delivering value far beyond the cost of our services and, in the process, ensuring our marine fleets are always mission ready.”
The acquisition enables AMMCON to expand its products to additional platforms and customers across the U.S. Navy, Coast Guard, and Military Sealift Command. It marks FMD’s eleventh acquisition since beginning its expansion in December 2020 to serve the maritime defense industry with turnkey solutions, the company said.
Fairbanks Morse’s acquisitions include companies such as American Fan (fans and blowers); Federal Equipment Company (cranes and specialized material handling); and Hunt Valve (actuators and valves). Maxim Watermakers (water treatment and purification); Research Tool & Die (electrical systems hardware); Samtan Engineering (electrical systems hardware); and Ward Leonard (controllers and motors) are among the others.
Startup Delivers AI-Driven Hypersonic Aerothermodynamics Capabilities to U.S. Air Force
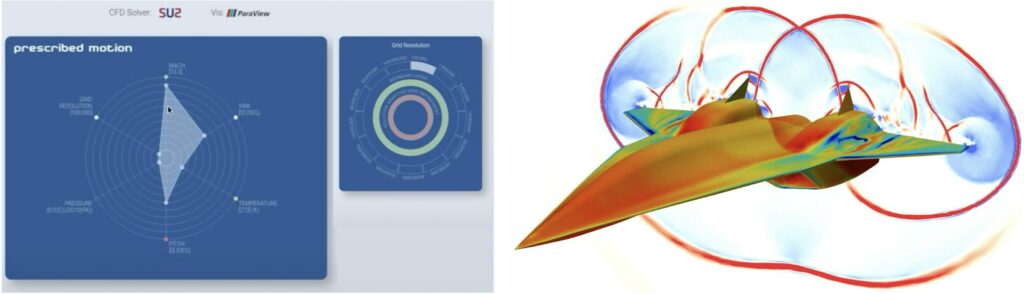
GURU autonomously sets up and runs high speed airplane design simulations for the Air Force. (Image: MSBAI/PRNewswire) Video: https://youtu.be/X_4X9lKSpJ4
LOS ANGELES—A digital engineering startup with a vision to bring the power of AI to simulations recently achieved a milestone that is reported to represent a significant advancement in the U.S. Air Force’s digital engineering capabilities for next-generation supersonic and hypersonic aircraft development.
As it successfully completed its AFWERX Phase 2 SBIR contract, titled “GURU Owns the Modeling and Simulation Tech Stack,” MSBAI said it is unlocking the power of Air Force High Performance Computing (HPC).
MSBAI, an Air Force Techstars 2020 company, said in a release that it was awarded the contract under the 2021 Air Force Digital Engineering Pitch Day initiative. According to MSBAI, it has delivered a “groundbreaking autonomous solution that can set up computational fluid dynamics (CFD) simulations for high-speed aircraft in a matter of minutes—a process that traditionally takes hours to complete.”
The capability, which MSBAI calls “transformative,” is embodied in MSBAI’s GURU platform. It responds to the U.S. Department of Defense’s imperative to accelerate AI adoption, as recently outlined by William W. Streilein, Ph.D., chief technology officer for DoD’s Chief Digital and Artificial Intelligence Office (CDAO).
The Digital Engineering Pitch Day initiative was launched to identify and accelerate the development of novel digital engineering capabilities that could benefit the U.S. Air Force. AFWERX, the innovation arm of the Department of the Air Force and powered by the Air Force Research Laboratory (AFRL), was seeking innovations that could advance the Air Force’s digital transformation and improve its ability to rapidly design, develop, test, and field new systems.
“Digital engineering isn’t an option. It’s essential. It’s faster, it’s cheaper, it’s better,” said Air Force Secretary Barbara Barrett, in a release from MSBAI.
“The digital engineering pitch day was a critical step in accelerating the Air Force’s digital transformation,” said J. Kyle Hurst, Chief of the Department of the Air Force Digital Transformation office (DAF DTO), in the release. “By tapping into the innovative capabilities of non-traditional defense companies, we were able to identify solutions that can truly revolutionize how we design, develop and field new systems.”
The successful delivery of GURU, now operational at the Air Force Research Laboratory’s DoD Supercomputing Resource Center (AFRL DSRC), marks a critical milestone in the Air Force’s digital transformation efforts, according to the release. Vince “Swath” Pecoraro, lead program Manager at DTO, commended the MSBAI team.
“Great leadership is in place, and the GURU product continues to impress,” Pecoraro said in the release.
Now that its contract has been successfully completed, MSBAI said it is “poised to further expand its transformative AI-driven capabilities to support the U.S. Air Force and American high speed aircraft designers in their pursuit of next-generation air superiority.”