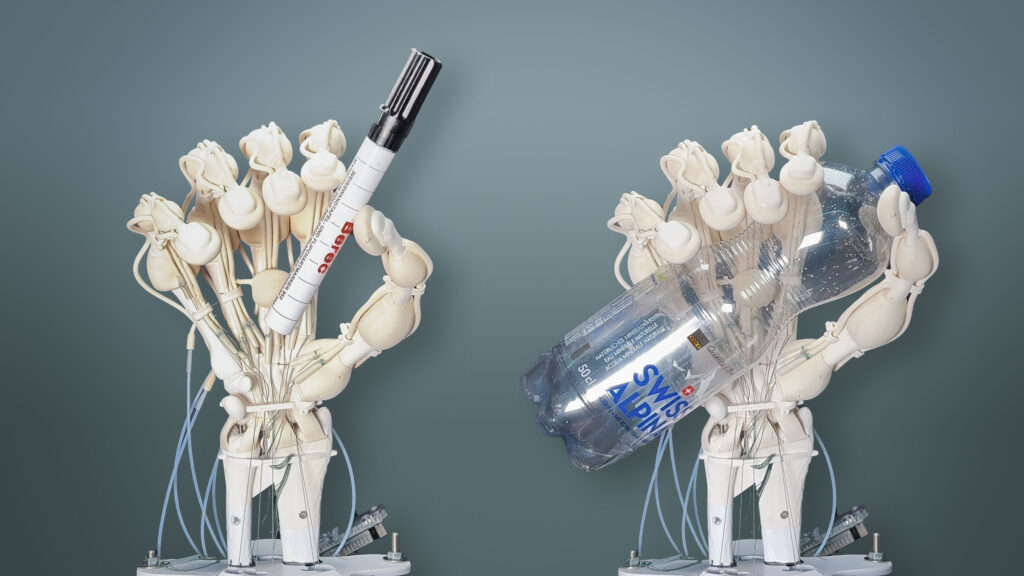
A fully functioning robotic hand made in a single print with Inkbit technology. (Photo: Business Wire)
MEDFORD, Mass.—Traditional manufacturing methods can struggle to fabricate systems that mirror the intricate structures and varied material properties found in nature. To address this challenge, a New England-based additive manufacturing company developed a technology that is reported to offer accurate fabrication of complex, multi-functional systems in a single print, without needing to assemble subcomponents.
A study published in the journal Nature demonstrates the use of the Vision-Controlled Jetting (VCJ) technology created by Inkbit™ to do just that.
The paper, written in collaboration with MIT and the Soft Robotics Lab at ETH Zurich, is titled “Vision-Controlled Jetting for Composite Systems and Robots.” It aims to show how the VCJ technology “opens a new frontier in manufacturing by expanding our capabilities to recreate synthetically the intricate structure and functionality of natural organisms,” according to a release from Inkbit.
“Our VCJ technology is a qualitative change in the field of additive manufacturing,” said Inkbit CEO Davide Marini, in the release. “We are closing the gap between the elegantly sophisticated structures we admire in nature and our ability to replicate them synthetically. This isn’t just a step forward; it’s a leap into a new era of manufacturing.”
Inkbit said its VCJ technology originated from traditional inkjet 3D printing. But by integrating an AI-enabled 3D computer vision scanning system that captures the print geometry of each layer in real time, VCJ can take traditional inkjet 3D printing to a whole new level. Its
digital closed-loop feedback control operation is said to eliminate the need for mechanical planarizers and enable printing with slow-cure chemistries that build the polymer chain more precisely.
As a result, VCJ can directly print intricate, multi-material parts in a wide range of mechanical properties with accuracy and precision, the company said in the release.
The technology’s applications are described as vast. According to Inkbit, Vision-Controlled Jetting not only enhances the resolution and functional capabilities of printed components; it also enables fabrication of intricate internal networks of channels and cavities to carry signals, power, or fluids through the structure. With VCJ, it is now possible to directly fabricate sophisticated, multi-functional systems capable of performing complex physical tasks at scale, the company said.
To demonstrate VCJ’s capabilities, the authors of the Nature article printed a variety of complex systems. Among them were a tendon-driven hand modeled from MRI data, a pneumatically actuated walking manipulator, a pump mimicking a heart, and novel metamaterial structures.
“With Inkbit’s VJC technology and materials, for the first time, we were able to print something as complex as a robotic hand with bones, ligaments, and tendons, mirroring a fully functioning human hand, and do so in one go,” said Thomas Buchner, doctoral student at ETH Zurich, in the release. “Inkbit’s TEPU material has very good elastic properties and [bounces] back to [its] original state much faster after bending than polyacrylates, making it ideal for producing the robotic hand’s elastic ligaments.”
Inkbit said the new technology is “poised to revolutionize the way we think about product design and manufacturing, especially in fields that require multi-step assembly processes and complex supply chains.” According to the company, the study published in Nature marks a significant milestone in additive manufacturing and opens new possibilities in fields like robotics, healthcare, mobility, industrial automation, and defense.