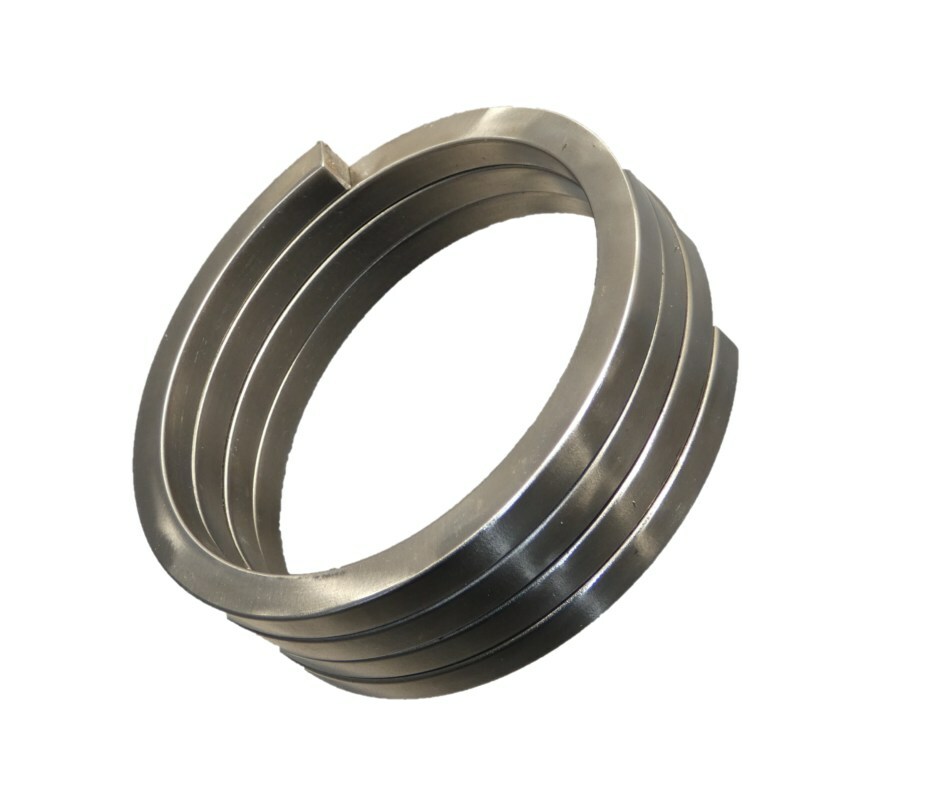
Advanced Magnet Lab’s PM-Wire™ technology is reported to produce non-sintered and sintered permanent magnets at a high rate and high yield. The process is adaptable to a variety of applications, including those that benefit from magnets in unique configurations and material compositions, such as electric motors. (Image courtesy Advanced Magnet Lab)
Advanced Magnet Lab, Inc. is working to meet rising demand for magnets needed in electrical machines, motors, and generators.
MELBOURNE, Fla.—Over the past year, magnet technology developer Advanced Magnet Lab, Inc. (AML) has been working to advance its technology, capabilities, and strategic relationships in preparation for opportunities to commercially manufacture permanent magnet products in the United States.
The company reported recently that it will take its first step into high-rate commercial manufacturing by producing non-sintered permanent magnets in the United States for select commercial and defense customers.
Advanced Magnet Lab said in a release that it has several development programs underway for enabling electric motor applications, including a collaboration with Oak Ridge National Laboratory (ORNL) for an electric vehicle motor. The company plans to co-locate manufacturing with customers or supply chain partners, and said preliminary discussions are underway with several United States jurisdictions for site locations.
Advanced Magnet Lab’s manufacturing capabilities are built on its PM-Wire™ technology, a scalable and modular manufacturing process that reportedly can produce non-sintered and sintered permanent magnets at a high rate and high yield. The process is adaptable to a variety of applications, including those that benefit from magnets in unique configurations and material compositions, such as electric motors, the company said.
According to AML, its collaboration with Oak Ridge National Laboratory is a “gleaming example of the value of PM-Wire.” The technology will replace 2,750 complex Halbach array sintered magnets with eight non-sintered helical magnets and eliminate the need to actively cool the motor rotor with equal motor performance. Advanced Magnet Lab envisions this demonstration as a potential springboard into commercial automotive applications.
The company also said it is working with commercial entities in several other active programs that provide similar benefits to end-use applications in industrial generators, aerospace, and defense.
Looking forward, AML said it plans to continue to expand its development programs and explore new material compositions for sintered and non-sintered magnets at its two locations on Florida’s Space Coast, in Brevard County. The two locations encompass approximately 10,000 square feet and will continue to support customers with prototyping and research and development for alloys and magnets.
Advanced Magnet Lab foresees scaling manufacturing organically in 2024 through strategic partnerships with customers and material providers. The company said it can support an output of approximately 200 mtpa of permanent magnets at its current locations in Florida.
Advanced Magnet Lab’s white paper, “Building a Better Magnet in America,” discusses the importance of creating a new and stable supply chain for the rare earth elements needed to make lighter, more efficient, and lower-cost electrical machines, motors, and generators.