Pico MES software is said to enable small- to-mid-sized manufacturers to increase and better measure their productivity.
SAN FRANCISCO—When MORryde, an Elkhart, Indiana-based metal fabricator and manufacturer of RV products, first implemented the Pico MES software platform, it was trying to improve its quality control while installing drivelines on motor homes. But after seeing immediate value, MORryde quickly expanded the software into its general assembly department. There, more than 1,000 part numbers are now digitized and managed through the platform, according to a release from Pico MES.
Pico MES is described as a no-code IoT platform that connects tools and machines with the people who use them. It measures shop-floor processes, creates a digital twin of assembly processes, and provides real-time data analytics to drive continuous improvement. Designed with the average factory worker in mind, it reportedly ensures “ease of use and faster adoption rates.” The software’s open API (application programming interface) enables integration with other essential systems on the shop floor, the developer said in the release.
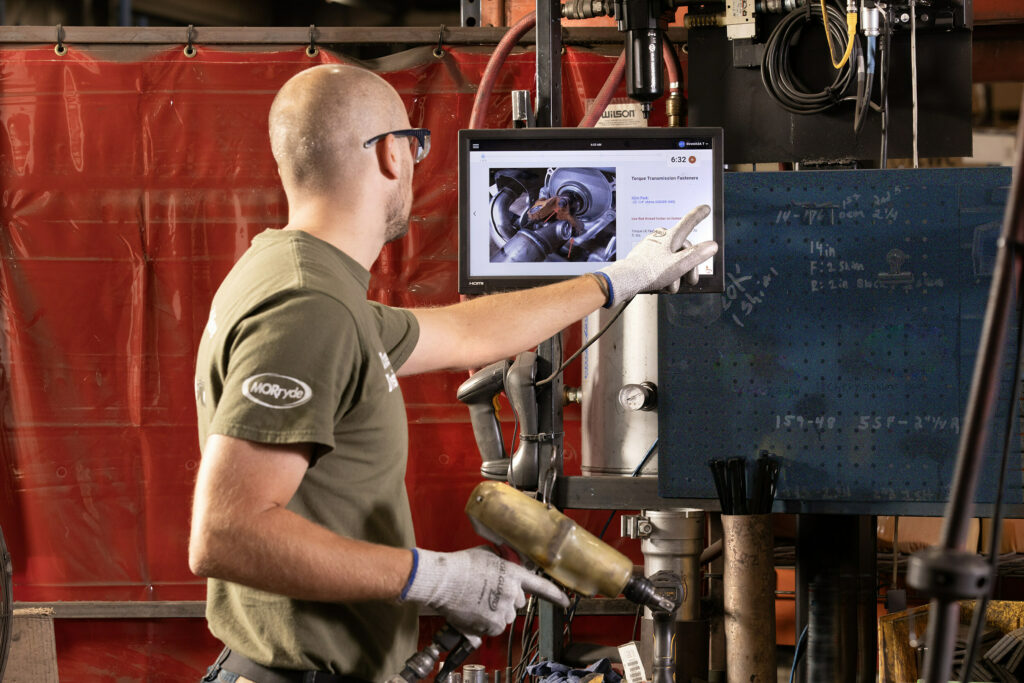
Jarrett Hullinger, quality engineer at MORryde, uses Pico MES daily. The software connects directly to a library of torque tools and validates that every fastener has been torqued to specification. Quality control is integrated directly into the workflow of Pico MES. (PRNewswire image courtesy Pico MES, MORryde)
In the 18 months since installing Pico MES, MORryde said it migrated more than 500 complex assembly processes from paper to digital. The manufacturer achieved a measurable 50 percent increase in production output and reportedly manufactured more than 2,400 chassis “without any quality concerns.” MORryde also said that it fully integrated Pico MES with its ERP (enterprise resource planning) system and achieved “100 percent backward traceability in all areas of assembly where Pico MES is installed.”
“MORryde is proud to be an American manufacturer anchored on quality, first,” said Greg Whitt, process improvement engineer at MORryde, in the release. “We have thrived over the past 50 years because of our ability to adopt innovative solutions. With over 13 manufacturing plants culminating in over 900,000 square feet in Elkhart, enrolling our employees into a new way of doing things can be difficult.
“Pico MES has been easy to adopt across our assembly area—it serves as a guide in the background, providing incremental productivity gains that culminate into larger efficiency gains,” Whitt continued. “We now ask the question: Where else can we use Pico MES to capture value?”
According to Pico MES, some 98 percent of American factories are operating with 500 or fewer factory workers. The Pico MES software platform is said to help manufacturers increase and better measure their productivity—a benefit when addressing current labor challenges for production of advanced products. The company said its new customer data demonstrates how its software capabilities create connected factories and bridge the manufacturing skills gap.
“Given the tight labor market, providing the supply base with solutions that are easy for the average factory worker to use is critical to the resurgence of American manufacturing,” said Pico MES CEO and Co-founder Ryan Kuhlenbeck, in a statement. “Anybody of any background can learn assembly processes of advanced products by using Pico MES.”
Kuhlenbeck, who had previously worked at Tesla and General Motors, started Pico MES in 2019 after recognizing that most manufacturing technology was developed to meet the needs of large-scale enterprise operations.
“When many people imagine a smart factory, they envision something complicated and expensive,” Kuhlenbeck said. “That paradigm is largely driven by legacy enterprise systems. Pico MES facilitates the digital transformation for small- to mid-sized factories by helping them measure and improve productivity.”
Today, rising demand for higher domestic production capacity has led to increased factory construction and re-shoring. But according to Pico MES, operational transparency challenges are hindering many manufacturers from meeting this demand. About 90 percent of factories use outdated tracking methods, the company said.
“Pico MES is at the forefront of the digital transformation of mid-sized factories,” said Michael Dolbec, managing partner of the venture capital firm Momenta, in a statement. Momenta was one of several firms, including lead investor Bosch Ventures, that participated recently in a $12 million Series A investment in Pico MES. “We firmly believe that manufacturing cannot thrive without a strong supply base. With its ability to connect factories with OEM customers and provide end-to-end visibility in the supply chain, Pico MES is poised to unlock new levels of efficiency gains for all stakeholders.”
The new funding will enable Pico MES to expand its platform to more factories, accelerating the digital transformation of American manufacturing and establishing more interconnected supply chains. In the four years since its launch, Pico MES software “has been deployed in dozens of factories that operate as Tier 1, 2, or Tier 3 suppliers to larger OEMs in the EV, aerospace, and battery industries,” the company said in a release detailing the funding.
“In order for factories to remain competitive, they need to digitize their labor-intensive production setups,” said Ingo Ramesohl, managing director of Bosch Ventures, in the release. “Bosch has a large network of suppliers and, like many enterprises, drives towards increased transparency in the deeper supply chains. Pico MES emerges as the catalytic force and has the potential to set new standards for transparency, collaboration, and operational excellence for all stakeholders within this ecosystem.”