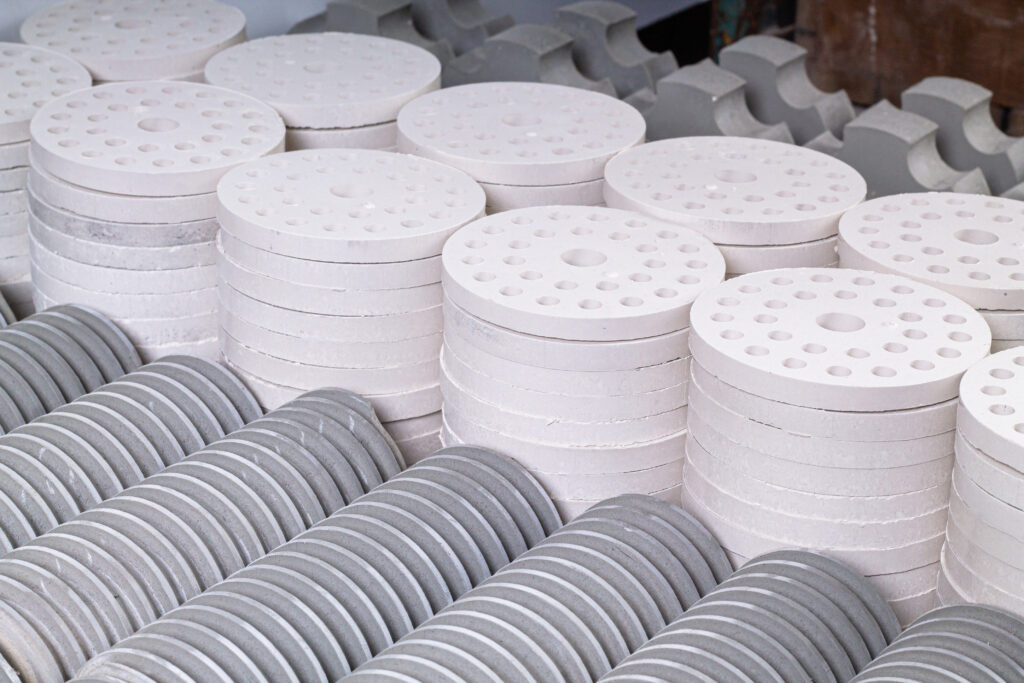
Ceramics require specialized precision grinding to achieve required tolerances due to the material’s exceptionally hard, dense, and brittle characteristics. (Image courtesy DCM Tech)
To combat the loss of seasoned operators to retirement, job shops are turning to more modern, automated surface grinders.
By Del Williams
Machine shops that grind ceramic workpieces flat to remove material or achieve a precise thickness now have “endless possibilities” to improve their capabilities—as well as production speed and control—with more advanced, automated equipment.
Today, ceramics are used in a range of industrial, commercial, and consumer products. With ceramics, some of which can be quite hard, grinding is an essential process to achieve closer tolerances. The extreme hardness, as well as strength, of some ceramics makes them difficult to grind. Due to the material’s exceptionally hard, dense, and brittle characteristics, ceramics require specialized precision grinding to achieve required tolerances.
However, due to the brittleness of ceramics, particular care must be taken to avoid surface damage, edge chipping, and pitting, as well as microcracks and fissures that can render a workpiece useless.
Modern rotary surface grinders offer sensors and controls that can contribute to achieving tighter dimensional tolerances, flatness, parallelism, and surface finish in much less time. The equipment can be used to planarize ceramic materials to close dimensional tolerances prior to lapping. Unlike traditional grinding, ceramic grinding involves using a metal-bonded diamond grinding wheel to remove stock from the surface of the material.
Operator control over the process is unsurpassed with the new automated grinders. The user can enter the specific machine parameters—for example: 712 RPMs on the spindle, 22 RPMs on the table, with a down-feed rate of 0.003 inch per minute, with a certain dwell time in seconds. Essentially, the machine parameters are infinitely variable.
Compared to traditional grinding equipment with manual controls that require experienced machinists familiar with the nuances of each machine, these automated units consistently produce higher quality parts in less time. As a result, a growing number of machine shops are installing new grinders that can be operated by less experienced personnel while still achieving the desired results.
Solving the skilled operator retirement problem
In machine shops that work with ceramic workpieces, factors such as thickness, parallelism, and surface condition are specified on a drawing. Grinding is utilized to remove stock to bring a workpiece to the stated dimensional specifications.
The use of older rotary surface grinders is a method for grinding ceramic, but can be problematic in the hands of less experienced operators. With limited control of spindle speeds, as well as manual controls, the older equipment requires experienced operators who can factor in complex considerations. Considerable expertise and experience are required, which can be a challenge as skilled operators retire.
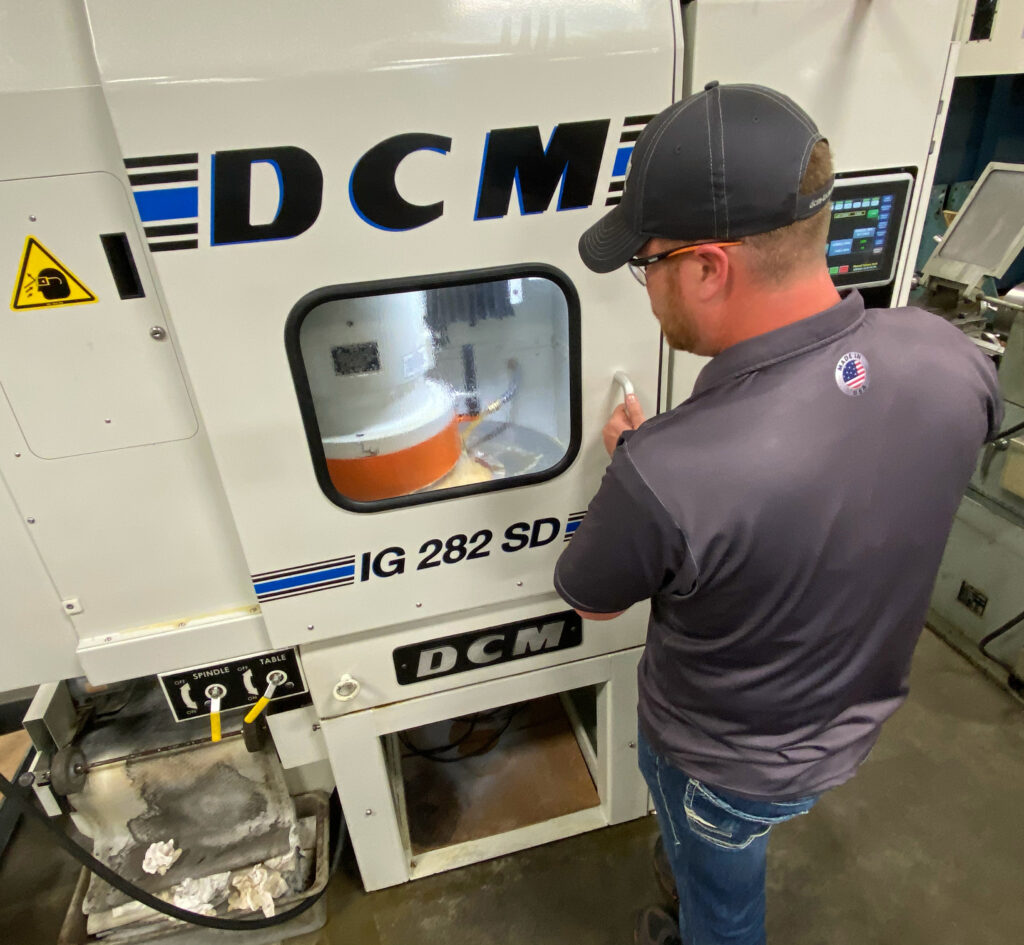
Advanced rotary surface grinders can be used to grind flat ceramic materials to precise dimensions before polishing. (Image courtesy DCM Tech)
Automated rotary surface grinders
In modern vertical spindle, rotary table surface grinders, the table rotates with the workpiece held firmly in place underneath a vertical spindle. The grinding is not performed by the peripheral edge of the wheel, but by the entire diameter of the abrasive surface, which facilitates grinding performance and consistency.
“With rotary table surface grinders, the entire part passes through the wheel, which is more efficient than reciprocating table grinders that may have workpieces wider than the grinding wheel,” said Erik Lawson, engineering manager at Winona, Minnesota-based DCM Tech, a designer and builder of industrial rotary surface grinders.
Today, surface grinders are designed with much more advanced sensors and controls that automatically maintain close tolerances via machine z-axis feed resolution of one ten-thousandth of an inch. Digital technology allows for an interface with easy-to-use touchscreen controls. When combined with automation, surface grinder operators are no longer required to be seasoned technicians.
For example, rotary units such as DCM Tech’s IG 282 SD, with a 24-inch variable speed table and 20HP variable speed grinding spindle motor, make it possible for virtually anyone to successfully operate a unit. One example of innovation available in this model involves the automation of the initial contact between the abrasive wheel and the part, which typically had to be finessed by the operator. When the machine senses the abrasive wheel has contacted the part, it automatically begins the grind cycle.
“Automatic part detection eliminates the need for the operator to do time consuming, error prone ‘manual touch offs,’ where they would manually feed the grinding machine until it just touches the surface of the part before backing off and restarting it,” said Lawson.
With regard to production efficiency, the advanced rotary surface grinders are also much faster than reciprocating grinders because the units can get closer to the required thickness dimensions prior to lap and polish operations. This capability can reduce or even eliminate lap and polish times.
“A rotary surface grinder will usually finish the work of a reciprocating grinder in a fraction of the time,” said Lawson.
The rotary grinder process also consistently achieves high throughput and can reduce variability, which enables machine shops to predictably generate targeted workpiece specifications, batch after batch.
In addition, programmable human machine interface (HMI) controls allow operators to enter machine operation parameters via fixed fields of entry on a thin-film-transistor, liquid-crystal display (TFT LCD) touch screen.
For routine processes, the use of a variety of grind “recipes” can be saved on the machine control memory, which provides process repeatability when differing—but recurring—jobs come to the machine.
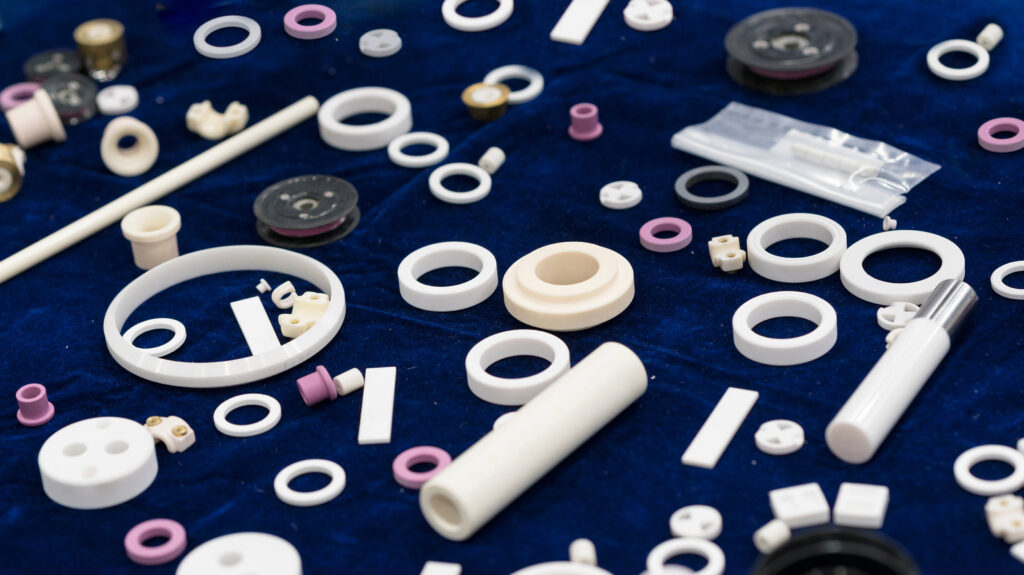
Due to the brittleness of ceramics, particular care must be taken to avoid surface damage, edge chipping, and pitting, as well as microcracks and fissures that can render a workpiece useless. (Image courtesy DCM Tech)
“Different grind recipes can be named for different customer jobs, material types, or even part numbers so complex programming or data does not need to be entered at the start of each job. A new recipe can be created for job variations, such as a different finish or number of parts on the table,” explained Lawson.
The grinder can also be programmed to make subsequent passes if the workpiece is not to size on the first pass. There is no need to touch off on the workpiece on subsequent grind sequences. The machine recalls position from the previous grind sequence and picks up where it left off.
According to Lawson, the automation provided by advanced rotary grinders allows operators to set up the machine and then attend to other tasks. The machine does not need to be constantly monitored because it has built-in load monitoring.
“Load monitoring allows the user to set limits to pause the auto-feed motion if the selected spindle load limit value is met during the grinding process. During the auto-feed pause, the spindle load will typically drop due to the wheel breaking down or material removal from the workpiece. When the load drops below the programmed load limit, the auto-feed will automatically resume at the programmed feed rate,” said Lawson.
He added that the automated units also contribute to a safer, cleaner shop environment because the grinding is accomplished inside an enclosed shroud that contains the debris and prevents it from entering the work area.
As the tolerances for ceramic grinding become tighter, and production requirements more demanding, machine shops that take advantage of advanced, automated rotary surface grinders can meet or beat current productivity levels as experienced operators retire.
“With automated rotary surface grinders, a machinist can be trained to be proficient at operating the equipment by lunch on their first day on the machine,” said Lawson. “It just takes a few hours of training—not decades of experience, as with older machines.” He added that systems incorporating full automation have been placed that use a robot to load and unload parts without an operator.
Del Williams is a technical writer based in Torrance, California.