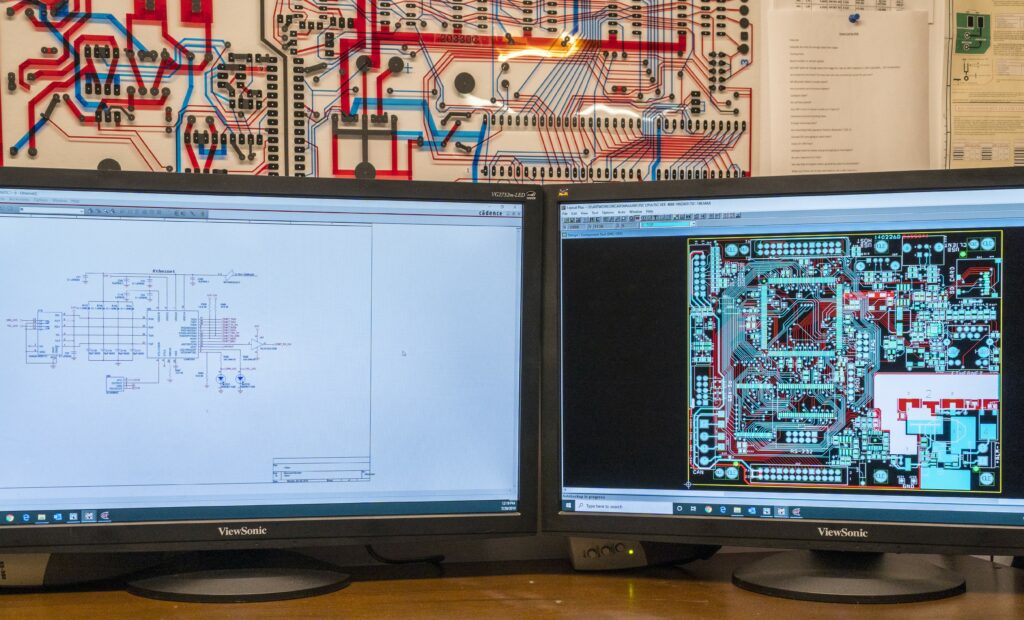
For customers seeking electronic design services, Thomas Instrumentation provides a custom PCB schematic (left) and layout (right). (Image courtesy Thomas Instrumentation, Inc.)
Thomas Instrumentation aims to meet OEMs’ needs for unique devices, shorter supply chains
By Mark Shortt
CAPE MAY COURT HOUSE, N.J.—In recent years, supply chain disruptions have wreaked havoc in industries where electronics play a pivotal role in products. Meanwhile, technological advancements in AI, electric vehicles, medical devices, consumer electronics, industrial machinery, telecommunications, and aerospace and defense equipment are boosting demand for printed circuit boards and their components.
As OEMs vie for market share in industries fueled by electronics innovation, many are seeking an edge by developing products that offer unique features, functionality, or performance. But it’s not an easy task. To get the help they need, they’re partnering with contract manufacturers whose expertise in electronic design, engineering, and manufacturing enables them to safely navigate the perils and pitfalls of creating a custom product.
Product manufacturers are also on the lookout for suppliers who can reduce their risk of supply chain disruptions, lower their project costs, and closely monitor quality at all stages of manufacturing. To achieve these goals, many are choosing to work with contract manufacturers who, by providing a greater number of services in-house, can limit the number of suppliers they contract with.
One company that checks all of the above boxes is Thomas Instrumentation Inc., a family owned and operated electronics firm that provides custom services in electronic design, software development, and electronics manufacturing. The company offers these core services and more from its base of operations in southern New Jersey (known regionally as South Jersey), where it has operated since 1975.
“We’re a one-stop-shop for electronics,” said Thomas Instrumentation CEO Cassandra Gluyas, in an emailed response. “We help make your project concept a reality.”
Its ability to combine the personal touch of a family business with a wide range of in-house technical services remains Thomas Instrumentation’s greatest strength, according to Gluyas, who said that typically, customers need to use a different firm for each of these core services.
“Here, everything is handled seamlessly, which gets our customers to market faster. Our full-service team treats you like family and truly cares about you and your product’s success,” she said.
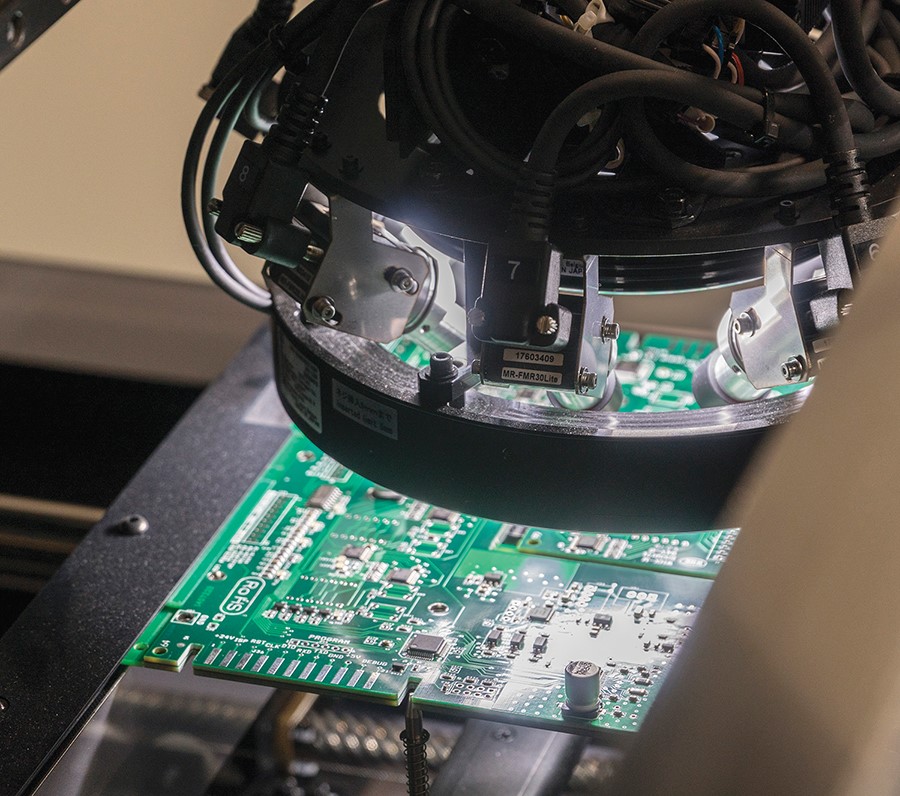
An automated optical inspection (AOI) machine inspects a circuit board at Thomas Instrumentation. (Image courtesy Thomas Instrumentation, Inc.)
Comprehensive in-house services
As an ISO 9001:2015 registered firm that provides RoHS compliant manufacturing, Thomas Instrumentation offers electrical engineering, printed circuit board (PCB) layout, design for manufacturing (DFM), prototyping, inspection, testing, and repair work. Additional services include solder paste stencil artwork, small wire harness assembly, and supply chain management. Customers who come to Thomas Instrumentation for electronic design at the outset can also avail themselves of the company’s software development, prototyping, and production manufacturing services.
For customers seeking electronic design services, Thomas Instrumentation provides a custom PCB schematic, layout, and Gerber files. The company’s electrical engineers combine custom analog, digital, and RF circuitry into the finished schematic. Its PCB layout designer creates the official PCB layout and the Gerber files. Thomas Instrumentation can also manufacture PCB prototypes of these designs for its customers through the contract manufacturing side of its business. (See “Electronics Manufacturer Focuses on Quality,” page 172, February 2021 issue of Design-2-Part)
The company’s software engineering team helps customers by editing existing software, adding new features, or creating entire programs from scratch. Although the team primarily develops embedded software solutions, it can also write programs for a variety of platforms. Its firmware releases are used to program custom electronic controllers for human interface, sensor feedback, and equipment control applications. All of its programs are stored in a backed-up version control system that keeps them safely managed for customers, Gluyas said.
“We’re a one-stop-shop for electronics,” said Thomas Instrumentation CEO Cassandra Gluyas. “We help make your project concept a reality.”
When contract manufacturing is needed, the company can handle the purchasing of all components of a product. As an alternative, customers can supply a parts kit for their run. Thomas’s manufacturing services span surface mount technology (SMT) production; through-hole PCB and wire harness assembly; fabrication; prototyping; inspection; and testing. The company accepts orders of various sizes, ranging from just a few up to 10,000 or more.
Custom electronics for a variety of unique products
Thomas Instrumentation traces its origins to Michigan, where Thomas Gluyas, an electrical engineer, started the company in 1971 before relocating its operations to New Jersey four years later. Tom’s daughter, Cassandra Gluyas, joined the company in 2011 in a dual role as engineer and chief executive officer. After earning a Bachelor of Science degree in electrical engineering, alongside a second major in computer engineering from Virginia Tech, Cassandra worked as an embedded software engineer at Lockheed Martin’s Skunk Works facility in Palmdale, California before joining Thomas Instrumentation, according to her LinkedIn profile.
One might say that Thomas Instrumentation is industry agnostic with respect to the wide variety of companies it serves. Its customers make products for markets as diverse as industrial, commercial, biopharmaceutical, medical laboratory, agricultural, and transportation. Other target markets include animal sciences, amusement parks, multimedia, and military/defense.
“We are happy to work with all industry sectors, as almost all of them require custom electronics,” said Gluyas. “It’s a custom electronics package for each OEM because every device is doing something unique.”
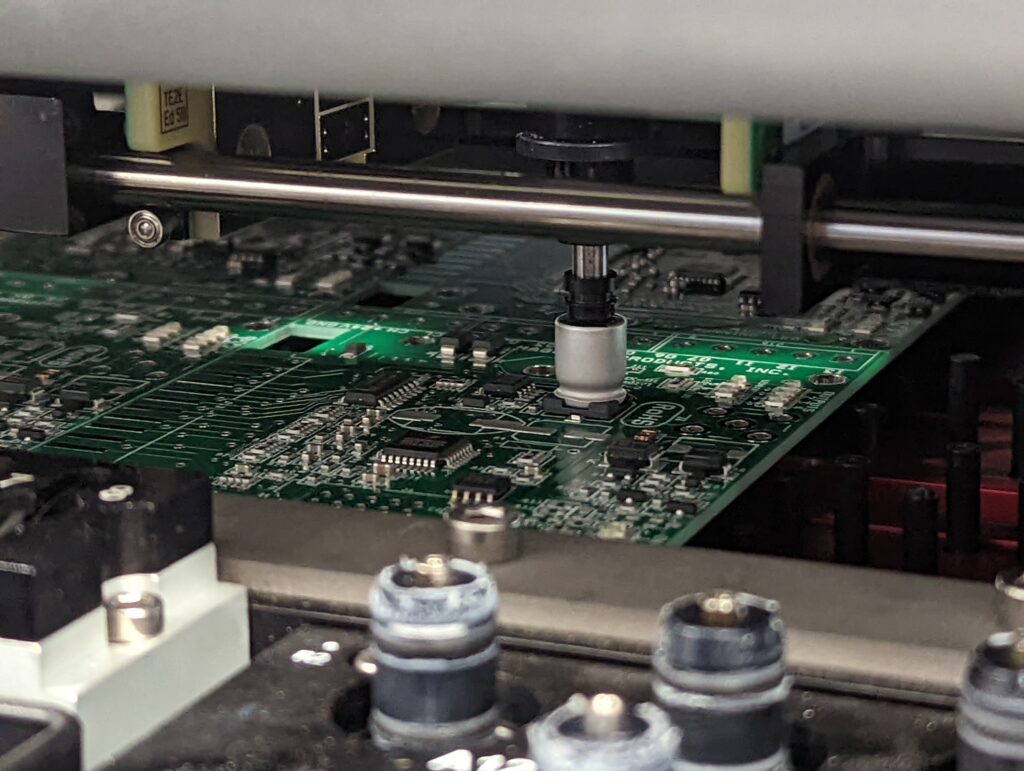
A surface mount technology (SMT) production line places parts on a circuit board at Thomas Instrumentation. (Image courtesy Thomas Instrumentation, Inc.)
Many of the systems produced by the company include a mixture of circuitry and software. Both are needed to run or analyze devices such as motors, fans, heaters, load cells, temperature and pressure sensors, and touch screen displays. They’re also essential in applications like controller area networks (CAN), USB, Wi-Fi, Bluetooth, and battery charging.
“Our manufacturing capabilities include high-complexity designs, mixed SMT and through-hole technology, double-sided boards, and component placements of fine pitch down to BGAs (ball grid arrays), WL-CSP (wafer-level chip-scale packaging), and 01005s,” Gluyas said. “Our manufacturing failure rate has always been less than 1 percent.”
“We are happy to work with all industry sectors, as almost all of them require custom electronics,” said Gluyas. “It’s a custom electronics package for each OEM because every device is doing something unique.”
Gluyas said the company’s manufacturing team has been hand-soldering through-hole components since 1971, updating its processes regularly to meet industry standards. In 2001, the company acquired its first SMT production line, and has continually updated its SMT processes as well. All of Thomas Instrumentation’s SMT production line equipment is updated, maintained, and fully calibrated by the original equipment manufacturers on an annual basis, Gluyas said.
Commitments to advanced equipment, technical training, customer service
Thomas Instrumentation’s manufacturing team operates a variety of advanced manufacturing and test equipment. Among them are the MPM Momentum Solder Screener with Paste Inspection; dual Mycronic MY200 Pick-and-Place machines; a Heller oven; a MEK Automated Optical Inspection machine; and a Creative Electron X-Ray Inspection machine. The company’s manufacturing technicians are given formal training by the manufacturers of the equipment, often spending days and weeks in classes to master the finer points of operating the machines.
“Most of our employees have worked with us for over 20 years, which means customers always have access to highly trained and experienced technicians,” Gluyas said.
In addition to Thomas’s advanced manufacturing equipment and the technical experience of its team, Gluyas counts customer service among the company’s most important strengths. “We always try to create good working relationships by being flexible in our schedule, quick to respond, and honest in our answers,” she told D2P. (See “Electronics Manufacturer Focuses on Quality,” page 174, February 2021 issue of Design-2-Part)
One client came to Thomas Instrumentation seeking improvements to a tiny, printed circuit board for a wildlife tracking device. The PCB is a radio transmitter that’s attached to wildlife, primarily birds, to track their movements and migration patterns.
“They were having a 50 percent manufacturing failure rate,” said Gluyas, referring to the customer’s experience with its previous manufacturing partner. “They told us they would love to see a less than 10 percent failure rate, but would accept anything better than 50 percent at that point.”
Shortly after accepting the challenge, Thomas Instrumentation received the board’s schematic, layout, and assembly instructions from its new customer. The company also received a few operational boards and some defective boards to analyze. Thomas’s electrical engineering team worked with its head manufacturing technician to review all the documents, boards, and previous manufacturing process. These boards were extremely small—less than ¼ inch wide by ½ inch long, Gluyas said—and weighed less than 2 grams.
The customer had been manufacturing 5,000 of the PCBs at a time, so approximately 2,500 of the boards were non-functional upon receipt. But the company had no idea what the root cause of the problem was—all it knew was that something wasn’t working. Thomas’s team knew it needed to review the engineering design and the manufacturing process to determine the root cause and then find a solution for it.
“We noticed that the solar cells on this product were specialty cuts and not a typical SMT component,” Gluyas said. “The layout and placement of this component appeared a bit sloppy. The part also required a jumper component to connect the solar cell to the rest of the circuitry. Our analysis revealed that the sloppy placement of the solar cell, in combination with this jumper component, was shorting the solar cell on the bad boards.”
Thomas Instrumentation’s team rolled up its sleeves and got to work. Its design team worked with the customer to edit the layout and bill of materials to use a more appropriate footprint and a new, larger jumper component. Using custom in-house tooling, the manufacturing team created a specialized tray to hold the solar cell components so that solder paste could be applied evenly to them. This enabled them to increase the accuracy of part-to-board placements. These modifications helped Thomas Instrumentation to reduce its customer’s manufacturing failure rate from 50 percent down to 1 percent, Gluyas said.
“We further analyzed our 1 percent failure rate and identified the solar cells to also have manufacturing defects. The customer was thrilled with our design and process improvements, deeming this a huge success, and it was all made possible by the fact that we have expertise in both electrical engineering and manufacturing.”